Cutting maintenance costs is easy. Just stop doing the work and the costs are gone. Most industrial plants will keep running longer than we think when we adopt this type of indiscriminate maintenance cost reduction. But chances are we’ve all experienced the longer-term effects of bad decisions when it comes to reducing maintenance costs like that. With COVID-19 the pressure is on once again as all industries struggle to work through this global economic downturn. But instead of indiscriminate cutting, how about this time we adopt a more sustainable way to reduce equipment maintenance costs?
Let me provide you with a simple framework with 4 Steps to Sustainable Maintenance Cost Reduction. You can either read the article, watch the video or do both!
The Pressure is on to Reduce Equipment Maintenance Costs
As of 2021, maintenance costs are under pressure. To be honest, they’re pretty much always under pressure, right?
But, in the current economic climate with a global pandemic, the pressure is really on the maintenance department and maintenance managers to lower costs. Apart from the tragic, tragic impact on people’s health and lives around the world, there has also been a massive impact on the economy. Many jobs have been lost and most countries, if not all, are experiencing harsh economic downturns.
The Bank of England, even, has declared that the UK has not seen an economic downturn like this for close to 300 years. 300 years. A bit closer to home, at least for me, Australia announced last year that it was officially in recession. That’s the first recession in a good 29 years.
So we all know the environment we’re in.
We all know that we have to reduce equipment maintenance costs.
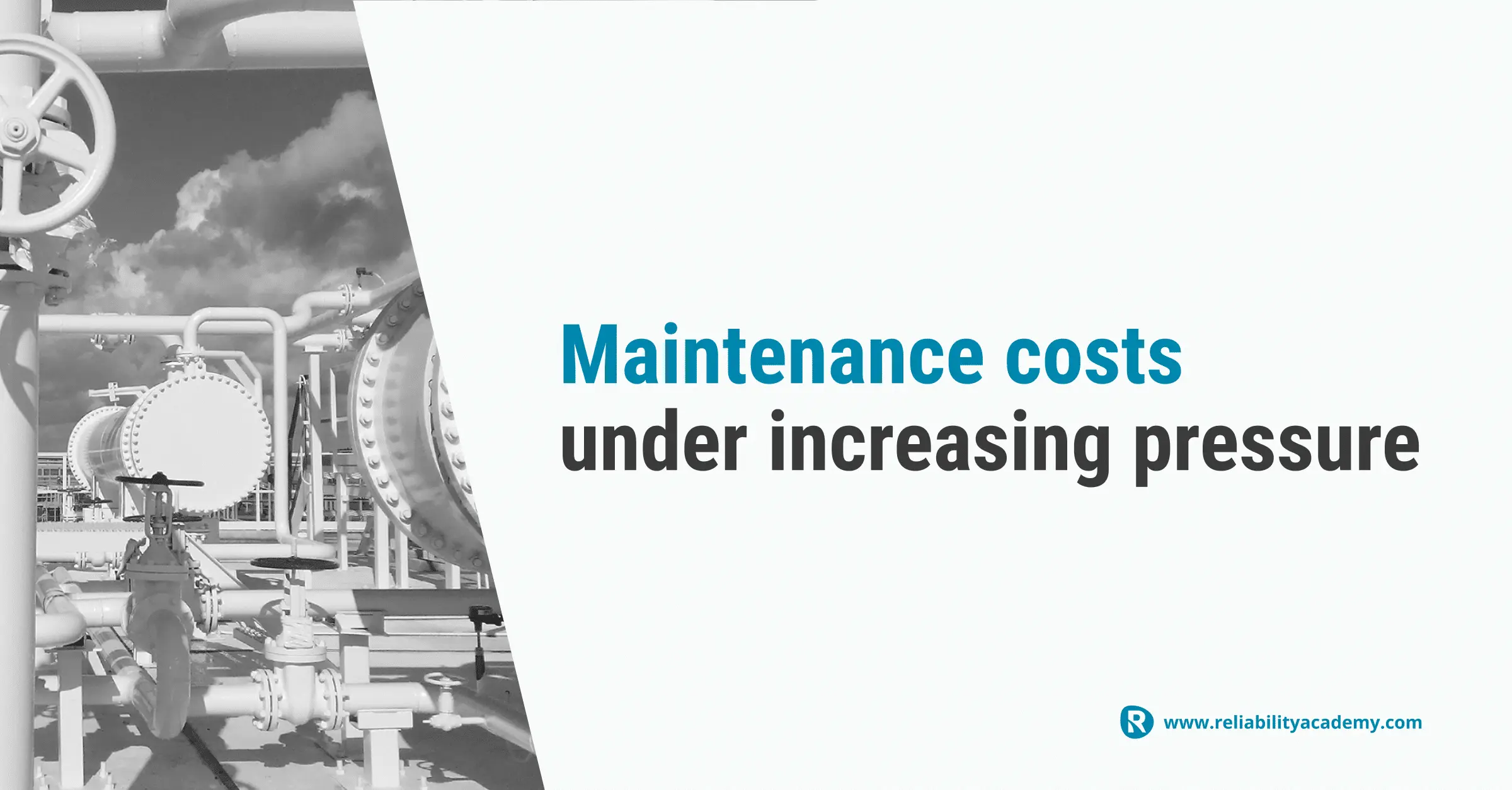
Reducing Maintenance Costs is Easy
In tough times like these, when equipment maintenance costs must be reduced, budgets must be cut. In asset-intensive industries, the maintenance budget is often 20% to 40% of the total annual budget.
Guess whose budget is going to get slashed?
Of course, it’s going to be the maintenance manager’s.
There is very little we can do about the business environment we’re in or the need to cut maintenance costs. What we can do something about, though, is how we cut those equipment maintenance costs.
We’ve all seen the classic approach, and we’ve all probably been victims of it through our careers.
The approach where you just slice 20% or 30% off the budget.
You defer a large amount of work…
You send people home…
You don’t buy spares…
You don’t train your people…
Job done.
And look, most plants can limp along for two, three years, before the lack of maintenance starts to haunt the equipment.
And eventually haunt the organisation itself.
By then, it’s usually the next maintenance manager or plant manager who has to deal with the consequences.
But that is not the sustainable maintenance costs reduction I’m after, and that’s not what I want to talk about either.
What I want to talk about is a more structured, more disciplined and a much more sustainable approach to reduce maintenance costs.
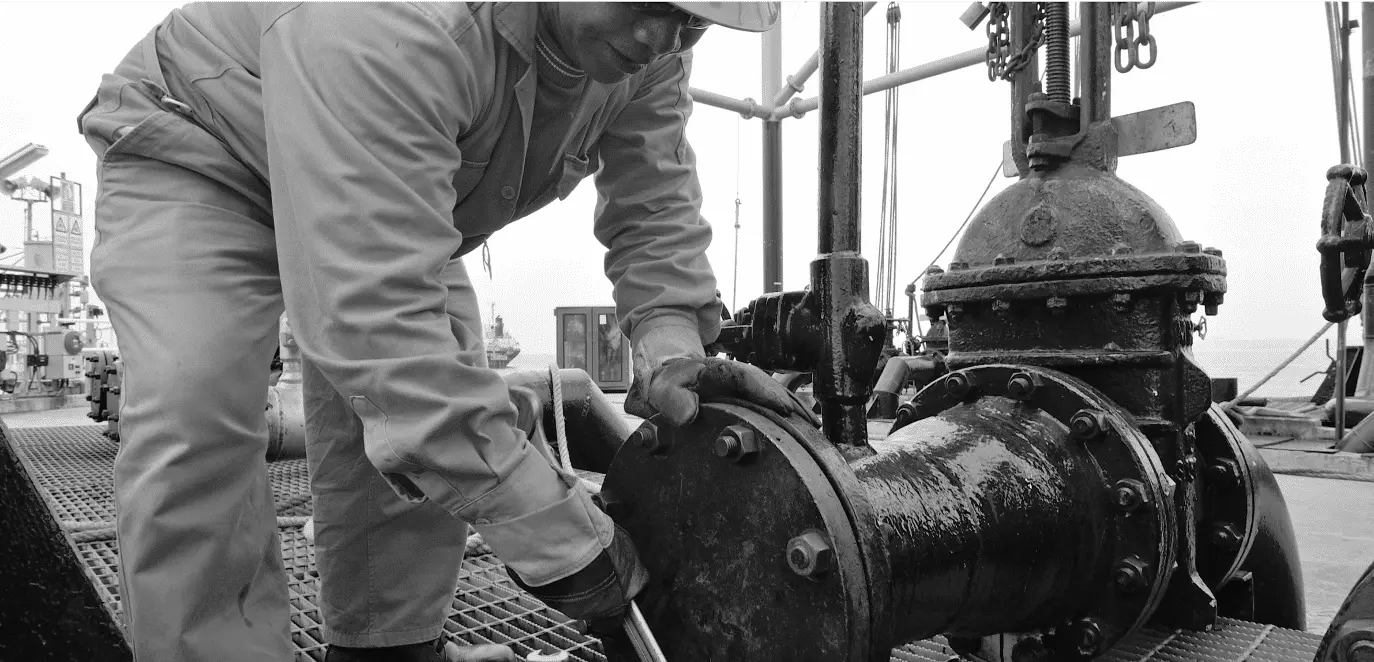
Maintenance costs are a consequence
Before we go further, there’s one thing I really want to make clear, and that is that maintenance costs are a consequence.
They are a consequence of the amount of preventive maintenance we do.
They are consequence of how many equipment failures we experience.
They are consequence of the amount of people we have working for us, whether that be employees or contractors.
They are a consequence of how efficient we are in executing the work we do.
And, they are a consequence of what we pay for the services, parts and materials that we buy as inputs to our maintenance.
So we have to remember, maintenance costs are a consequence of the maintenance we have set up and how well we run our maintenance.
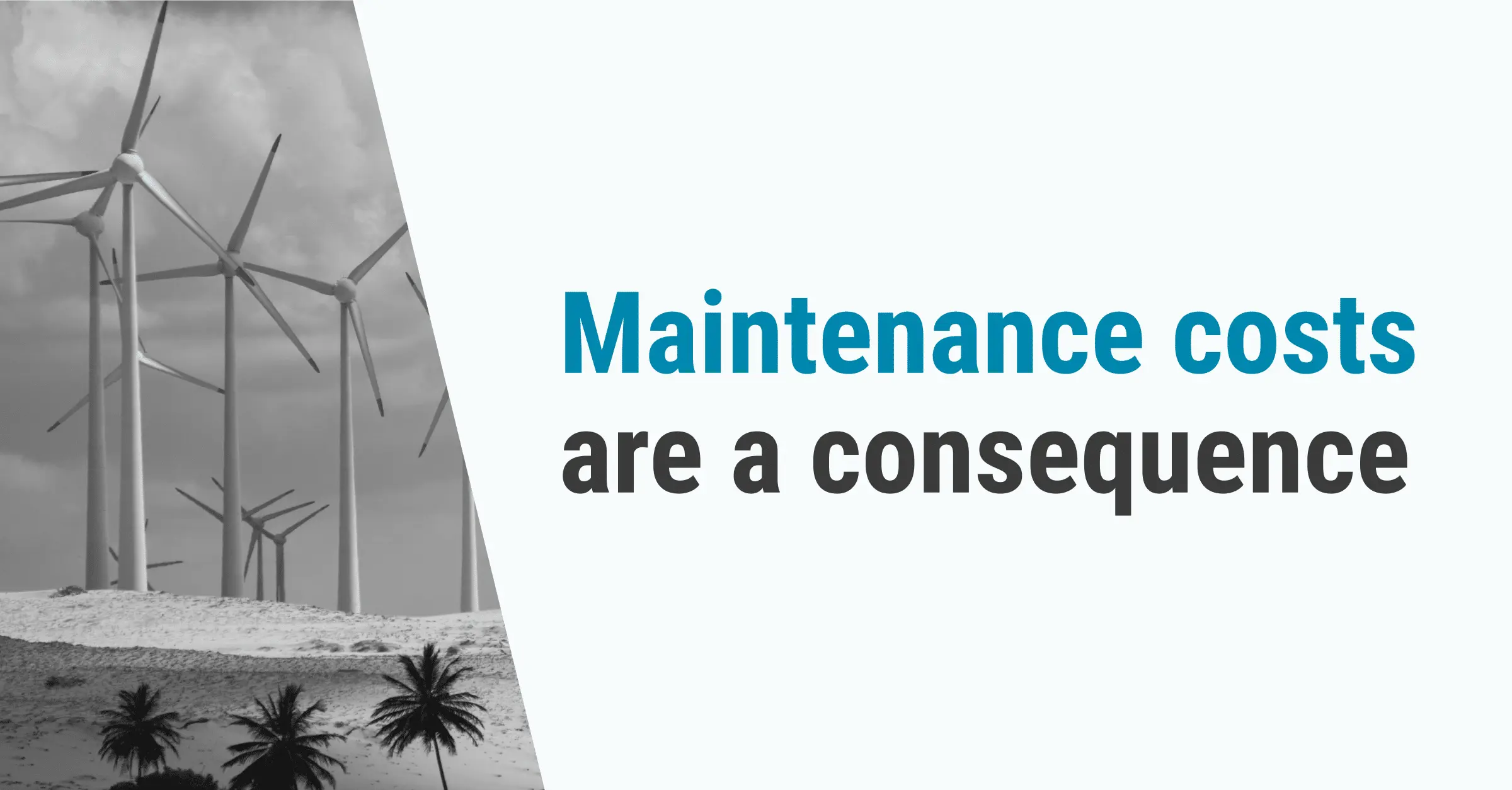
The 3 things you spend your maintenance budget on
When it comes to how you spend your maintenance budget, in basic terms, you spend your money on three things.
First, labour, whether that be your own employees or contractors.
Second, you’re going to spend a sizeable chunk of your budget on parts, materials, consumables and tools.
And third, you’ll likely spend a good amount of money on external services: specialist technicians, OEMs, field engineers, etc.
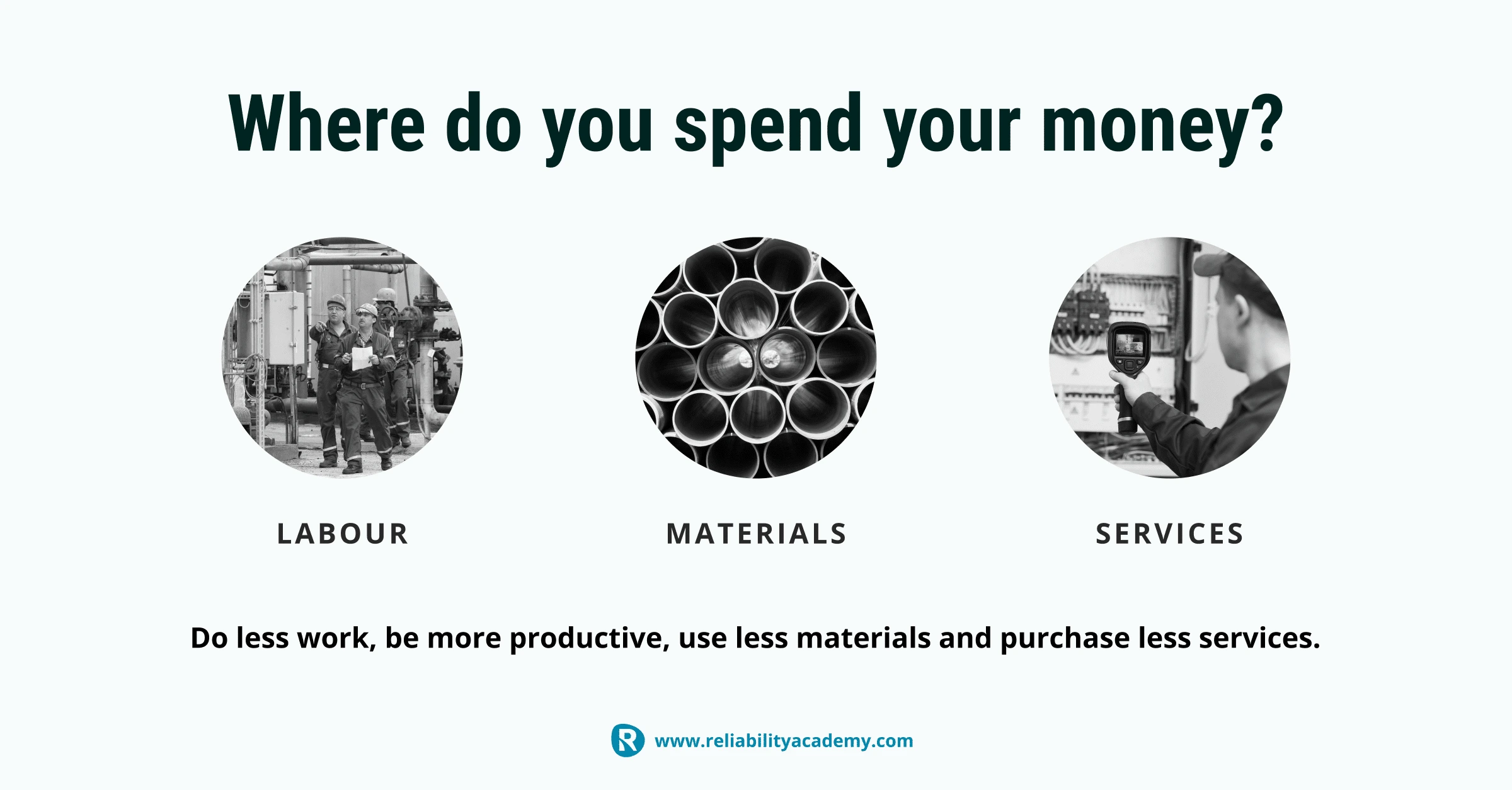
Reducing maintenance costs: the WHAT is easy, the HOW is the problem
So, if you want to reduce maintenance costs, WHAT you need to do is pretty straightforward.
You need to do less work.
You need to be more productive.
You need to use less materials and you need to purchase less services.
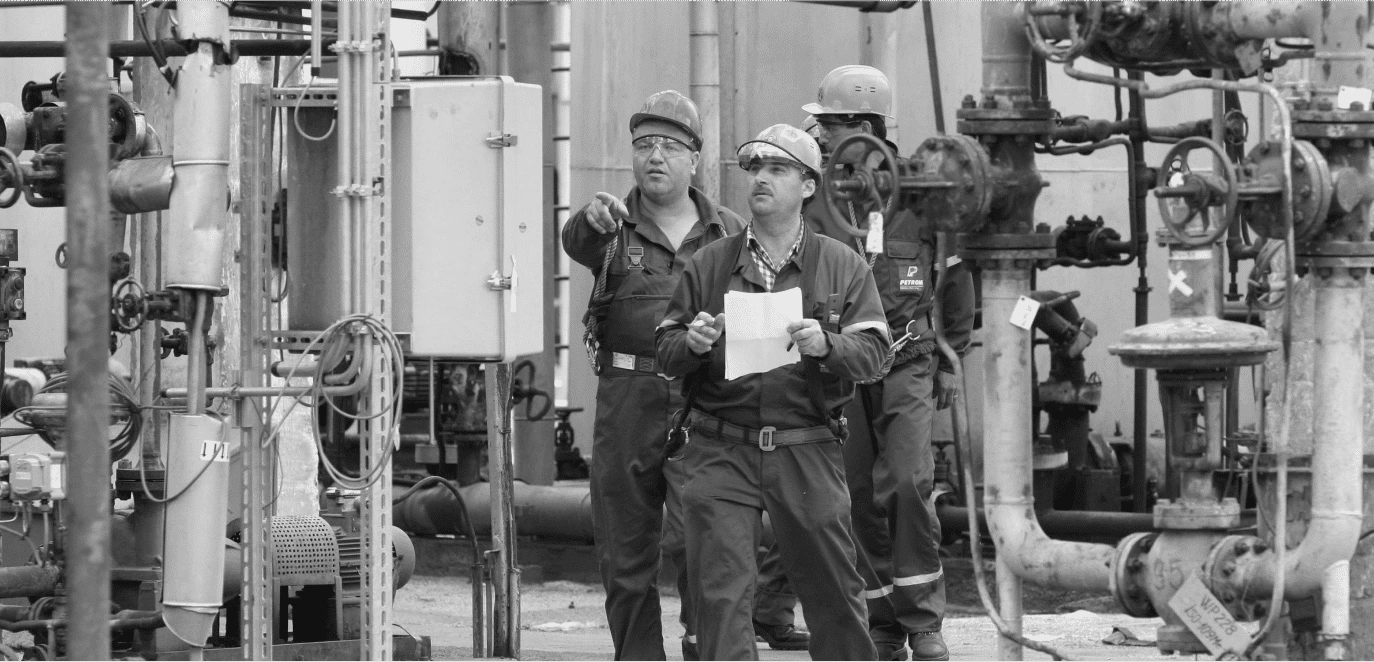
4 Steps to reduce maintenance costs
Even though the WHAT is obvious, the problem is the HOW.
How do we do less work, use less materials, use fewer external services, pay less for what we buy and still achieve a good maintenance performance and high reliability?
Chances are that as you read this, you’re thinking, “Look, this is all very nice, but that’s just impossible.”
And I can understand that you feel that way.
But if you look around any major industrial client and look at what maintenance is done and how that work is done, you’ll quickly see huge amounts of waste.
And interestingly enough, that waste is almost always in the same areas. So when you want to lower maintenance costs, there are typically four things you need to do:
- Tackle low maintenance productivity
- Improve your preventive maintenance program
- Eliminate all those repeat failures
- Improve your maintenance contracts and rates
In the rest of this article, I will discuss each of these in more detail.
Step 1: Tackle low maintenance productivity
The first area to look at is low maintenance productivity. At most industrial sites, the average day of a maintenance technician is really just full of waste.
I mean, if you carefully look at how your technicians spend their day, you’ll see that they spend so much time looking for parts, looking for tools, waiting for permits, waiting for instructions, waiting for equipment to become available.
And in the end, way too little time is left to actually do productive maintenance work.
And that’s all because there is no structured planning and scheduling process in place. Or if it is in place, it’s simply not adhered to.
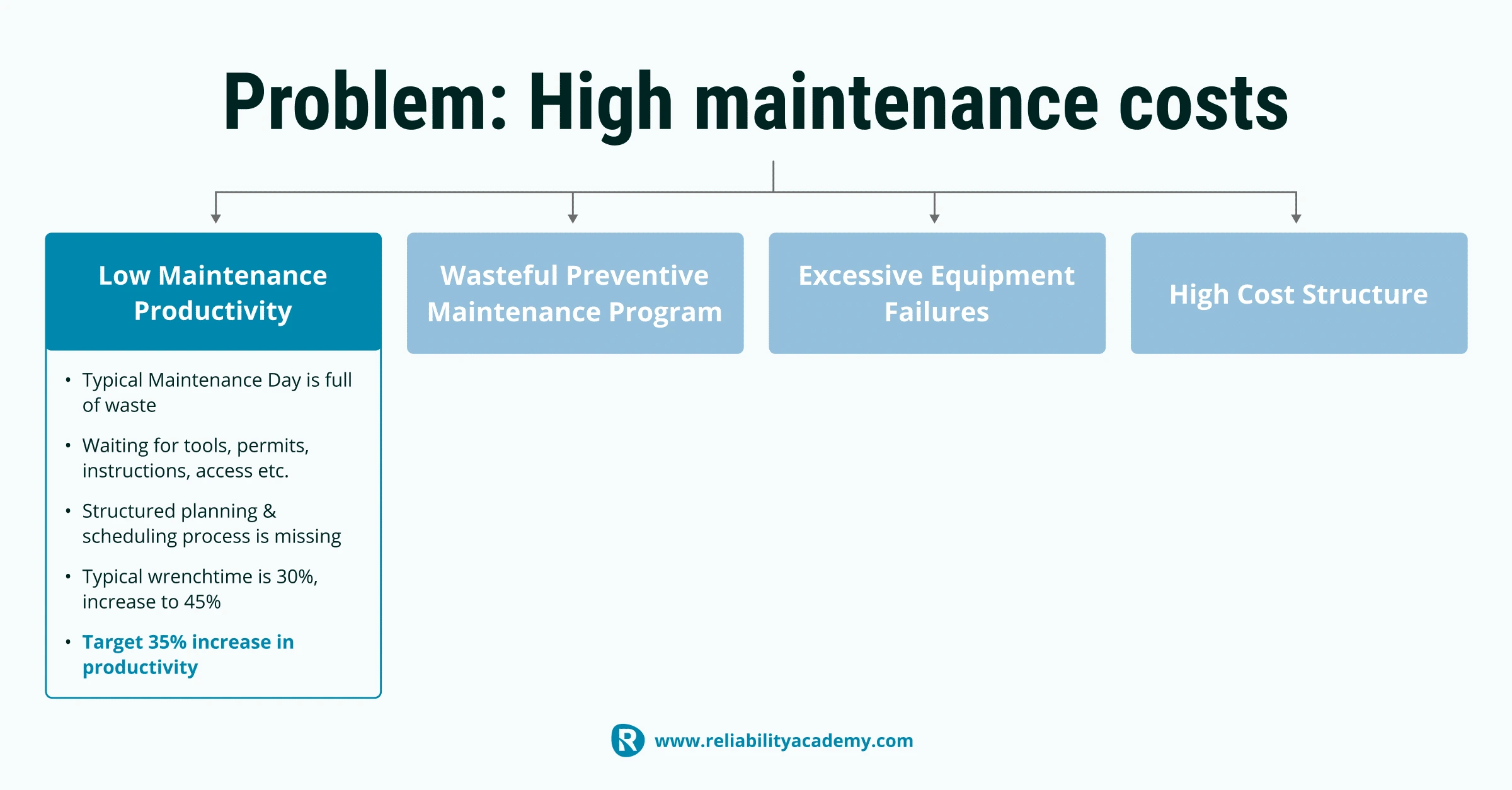
Reduce Maintenance Costs: Step 1 is tackling Low Maintenance Productivity
Typically, you find a maintenance team runs with a wrench time of about 30%, which means out of a 10-hour day, you’re only getting three hours of real maintenance work done.
With an effective planning and scheduling process, you can increase that to 45%, which translates to a productivity increase of 35% without hiring any more people.
So even if you don’t already have planners and schedulers in place, when you move from a wrench time of 30% to 45%, you still create that 35% increase in productivity.
Calculating That Productivity Increase
Assume we have 20 technicians who work five 10-hour shifts per week for 48 weeks per year. These 20 technicians work at an industry average wrench time of 30% for a 10-hour day.
That means over the course of a week they can liquidate 20 x 10 x 5 x 30% = 300 productive hours of maintenance work.
We now introduce planning and scheduling. But we promised the CEO that we would not need more people, so we take two technicians and make one a planner and one a scheduler. That leaves us with 18 technicians, but after a transition period, we will achieve the typical 45% wrench time across their 10-hour days. That means that we now liquidate 18 x 10 x 5 x 45% = 405 productive maintenance hours per week.
Even though we’ve reduced our number of technicians we’ve gained 105 productive hours in a single week. That’s a 35% productivity gain!
This example first appeared in the article How to Sell Planning and Scheduling to Your CEO.
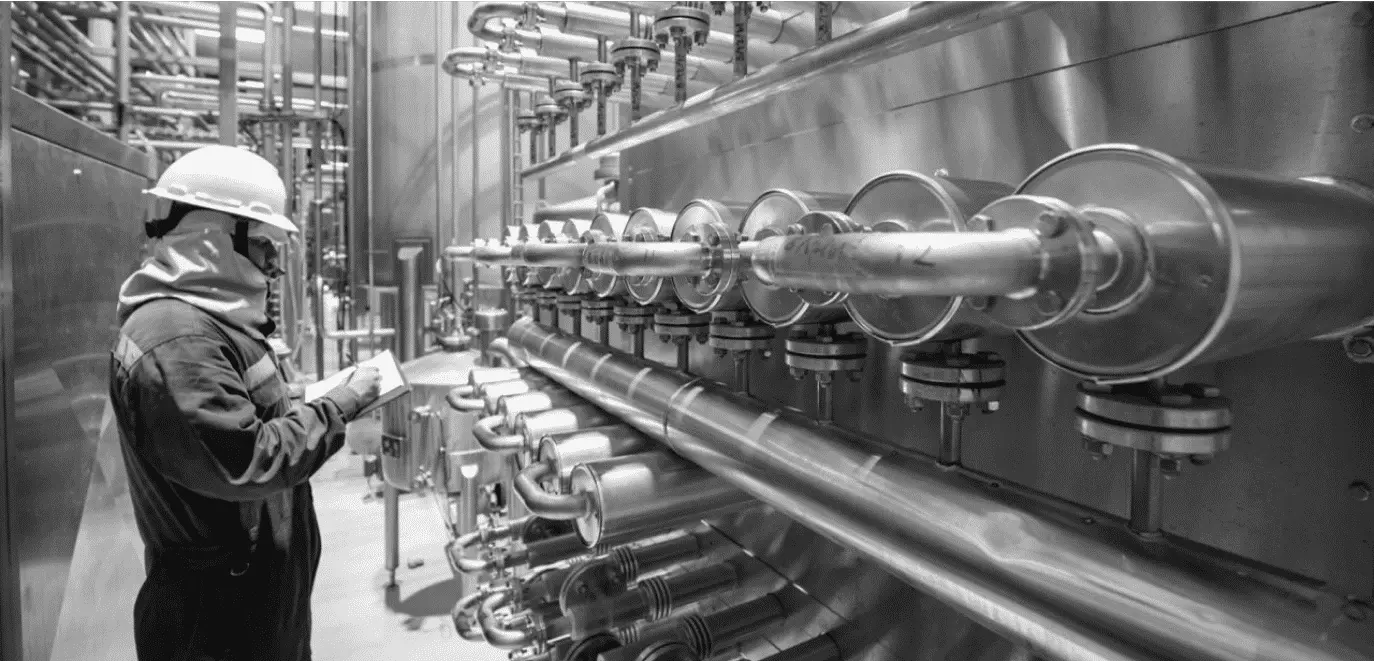
When it comes to implementing maintenance planning and scheduling, there’s actually very limited investment required.
So as a project, it has a really good—pretty much fantastic—return on investment. That excellent ROI is welcome news when you’re trying to sell maintenance planning and scheduling to your leadership.
I developed a great little tool: it’s a very simple wrench time calculator that lets you estimate how much value you can gain from implementing maintenance planning and scheduling in your organisation.
You can download it from the article How to Sell Planning and Scheduling to Your CEO.
Now, I do recommend that you adopt a standard approach to planning and scheduling. There’s really no need to reinvent the wheel. There are good processes out there— use them. And if you want to know more about what an effective maintenance planning and scheduling process looks like, read my article Without Maintenance Planning and Scheduling You Will Fail.
But even more important than all that is that you use a proven framework for implementation.
You see, it’s during the implementation of planning and scheduling where most organisations go wrong.
And in the end, most improvements—even if they are made to begin with—are just not sustained.
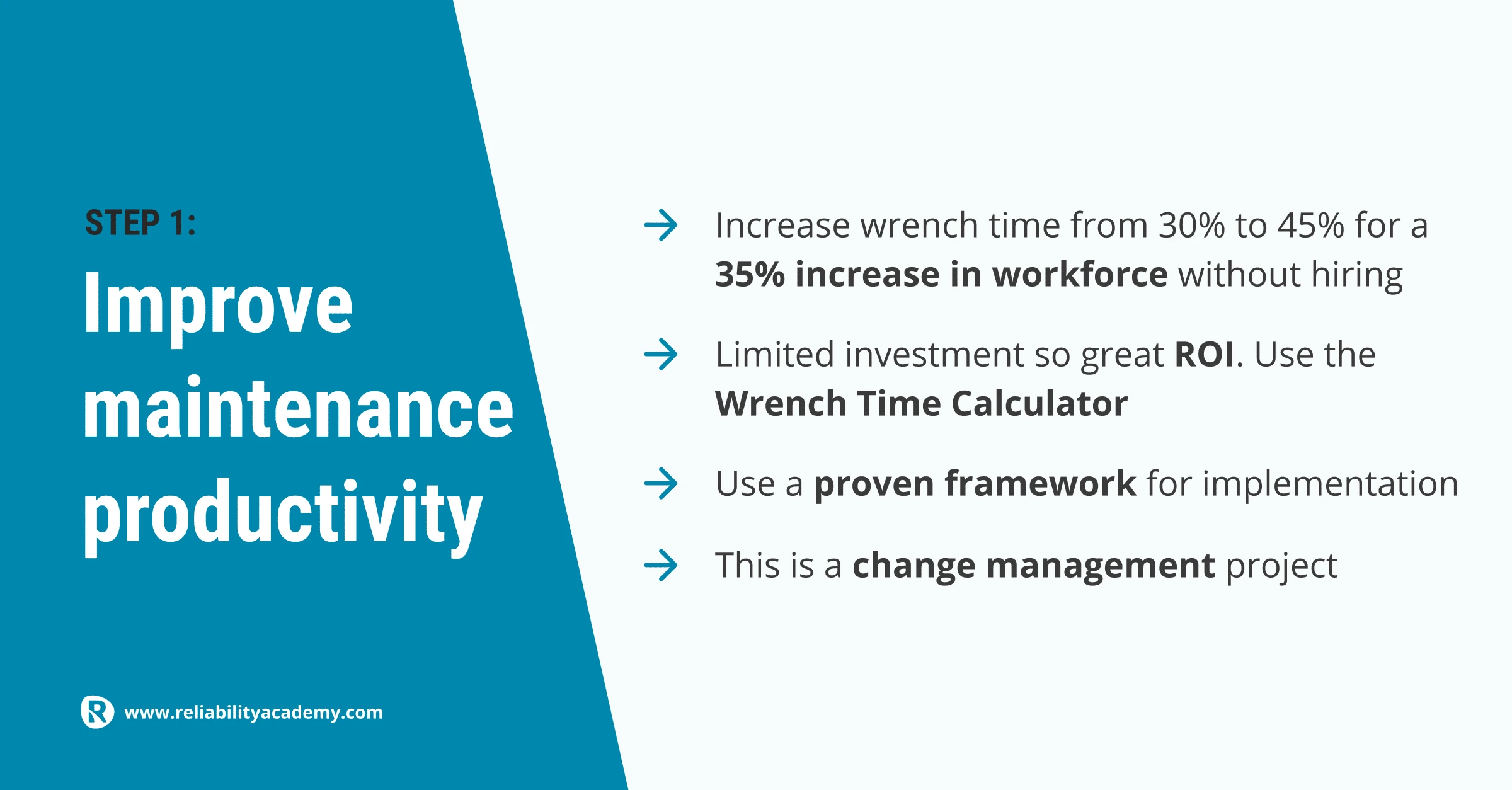
I always like to say that when it comes to implementing maintenance planning and scheduling, you need to treat it as a change management project.
For it to be a successful, you obviously need to understand maintenance planning and scheduling, and that is relatively easy to teach. But you also need to apply good project management principles and even more important, you need to apply sound change management principles.
And that is where most companies go wrong because the change management is something that is typically ignored. And then, as a result, many implementations fail and the improvements are just not sustained.
So don’t make that mistake.
There really is no need to. Read my articles or sign up for my online training course Implementing Maintenance Planning & Scheduling.
Step 2: Improve your Preventive Maintenance program
The second area you need to address is your preventive maintenance (PM) program. In most industrial sites, the PM program has not been optimised.
It hasn’t been reviewed for a very long time, and it often is very wasteful with a lot of tasks that add no value.
A lot of tasks that are done too often.
A lot of tasks that aim to prevent failure modes that actually don’t really matter for the business.
You’ll often find many tasks are poorly defined, so they’re not done properly and they’re not really effective—you’re wasting your money with these.
And often you find that there are tasks missing. Tasks that actually could be preventing some of your main reoccurring breakdowns.
Industry experience, literature and various studies show over and over again, that somewhere between 40% and 60% of your preventive maintenance tasks add little value.
These tasks just waste your scarce resources and inflate your maintenance budget for nothing.
So, if your preventive maintenance program has not really been reviewed in recent years, then from my experience, you should be reducing maintenance work by a good 20%, maybe more.
And when you take that 20% of work away, you are immediately reducing maintenance costs. Not just for this year or next year—you take those maintenance costs out for good.
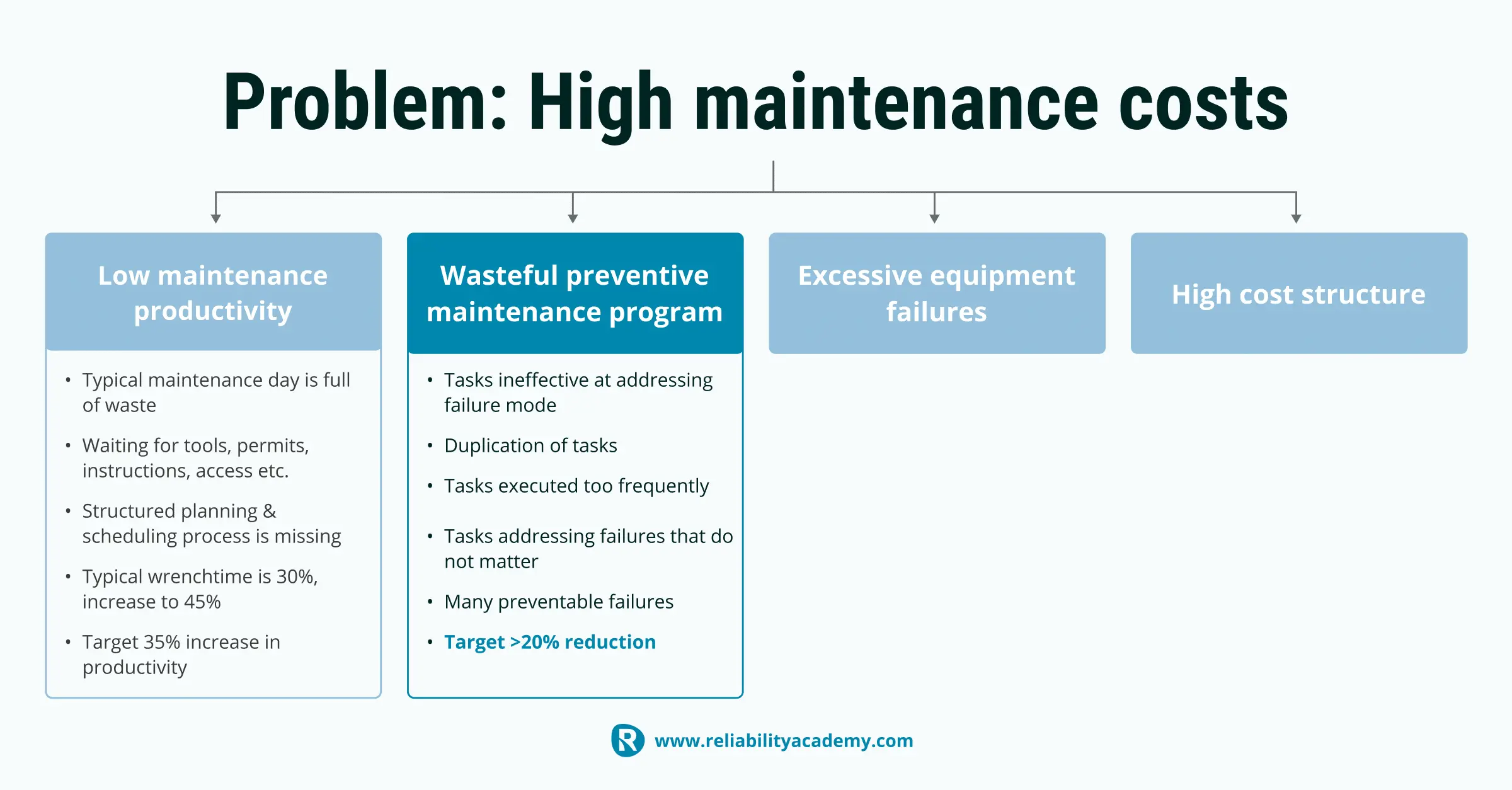
Reduce Maintenance Costs: Step 2 is tackling Non-Valued Added PMs
So how do you improve your preventive maintenance program? Do you go out and hire a consultant to do RCM? Or maybe someone who is specialised in PMO? Ah, they’re trying to sell you an FMEA or FMECA instead?
I don’t want to sound too cynical, but the problem is many buyers do not really understand the difference between RCM and PMO, or between an FMEA and FMECA and how an FMEA forms part of RCM. And unfortunately, there are many service providers out there who will gladly take your money and conduct a long, manpower-intensive RCM, PMO or whatever type of study.
But is that what you need?
Maybe not. Certainly not to begin with.
Instead, what you need to do first is a relatively simple analysis of your preventive maintenance program.
You’re going to dig into your computerized maintenance management system (CMMS) and you’re going to generate some basic Pareto charts that show you the following:
- the equipment with the highest amount of preventive maintenance hours on an annualised basis
- the equipment with the highest preventive maintenance cost on an annualised basis
- the PMs that cost you the most money on an annualised basis
- the PMs that require the most of your labour on an annual basis
And look, this analysis should be really quick, but it will be very insightful.
It’s easy, so you don’t need expensive consultants to do this for you.
And once you have these Pareto charts from your computerized maintenance management system, you then want to get together with some of your key stakeholders and focus on priorities and start tackling these PMs one at a time.
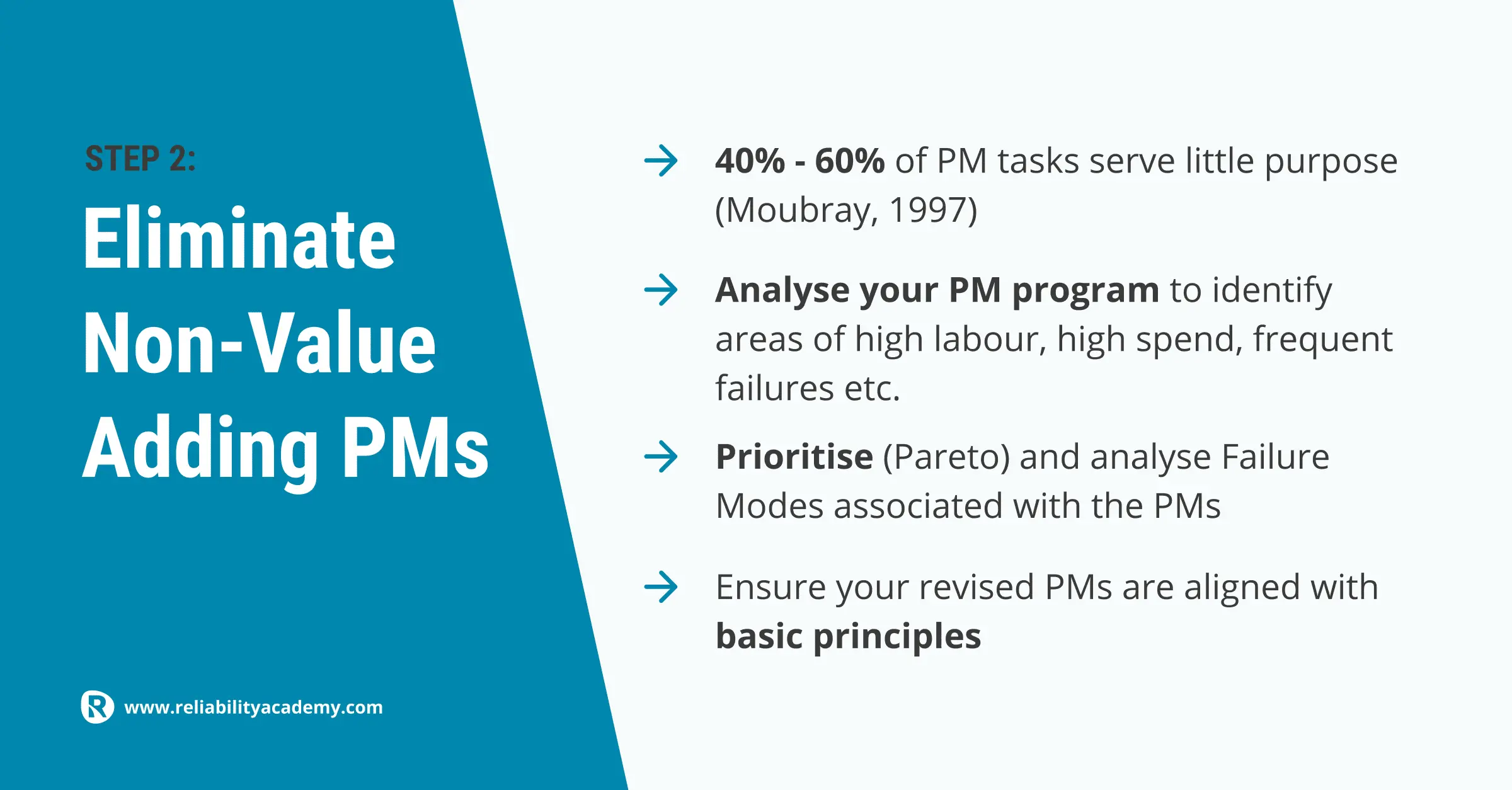
And for each task, for each PM, you want to have a look at the failure mode that the task is supposed to address and ask yourself the following questions:
- Is this failure mode credible?
- Have we experienced it?
- Is the consequence of the failure actually significant enough to justify the work we’re doing?
- Is the task we’re doing effective in dealing with the failure mode (e.g., are we using time-based maintenance where we should be using condition-based maintenance)?
- Does the task frequency/interval make sense?
- Is the task clear and concise so that it can be executed in a repeatable manner?
You’re going to have to work through a series of questions like these, and then you can find and eliminate the tasks that don’t really add value. And because you’re doing it based on your Pareto chart, you’re tackling the ones that are going to give you the biggest benefit.
Now, you need to make sure that when you develop your new PMs or optimise your existing PMs, you’re basing them on basic reliability practices.
And that means you need to know these practices and understand them. If not, you’ll end up making simple mistakes like using time-based replacements for random failure modes.
It doesn’t work and it’s a waste of your resources.
So, make sure you understand the basic reliability principles that should underpin an effective preventive maintenance program.
If you’re not really up to speed, or if you need a refresher, read this article Reliability Centered Maintenance: 9 Principles of a Modern Preventive Maintenance Program, or even better, join my online course Developing & Improving Preventive Maintenance Programs.
Step 3: Eliminate all those repeat failures
The third area that you want to tackle is the repeat equipment failures. It’s really common to find maintenance teams doing the same repairs over and over, and again and again.
Too often, the culture has become focused on what I call forever fixing, rather than fixing forever.
And look, breakdown maintenance is expensive. It’s time-consuming, and it drives an organisation into a reactive maintenance culture.
So this step is really about tackling your bad actors.
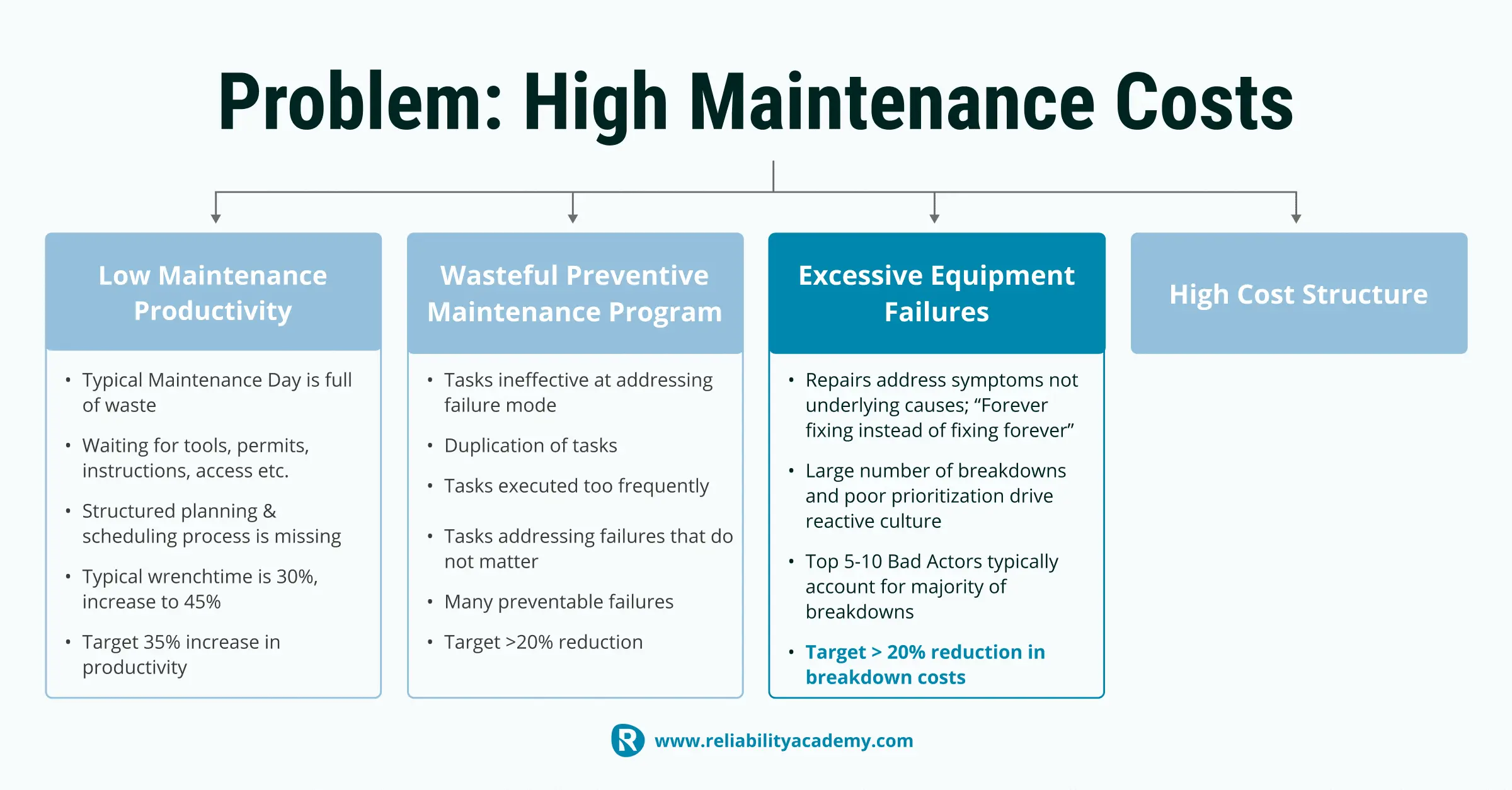
Reduce Maintenance Costs: Step 3 is reducing repeat failures
These are the few pieces of equipment or types of equipment in your plant that are responsible for the majority of your breakdowns, the majority of your corrective maintenance spend and the majority of your corrective workload.
If you eliminate these, you can reduce your corrective maintenance cost by at least 20%, likely more.
The way you do that is, once again, by delving into your computerized maintenance management system (CMMS) and analysing your corrective maintenance history. In the previous step, we were looking at preventive maintenance. Now, we’re looking at corrective maintenance.
And again, you’re going to develop a set of Pareto charts. You’re basically going to pull out the data to generate these charts, which will show you the worst performing equipment in terms of corrective maintenance cost, corrective maintenance effort and failure frequency.
When you do this, you’ll probably find that it’s a handful of equipment behind most of your corrective maintenance pain.
Together with stakeholders like operations and engineering, you’re going to prioritise these bad actors, and you’re going to do some basic, sound root cause analysis.
And what you want to make sure you do now is identify all the underlying and contributing causes.
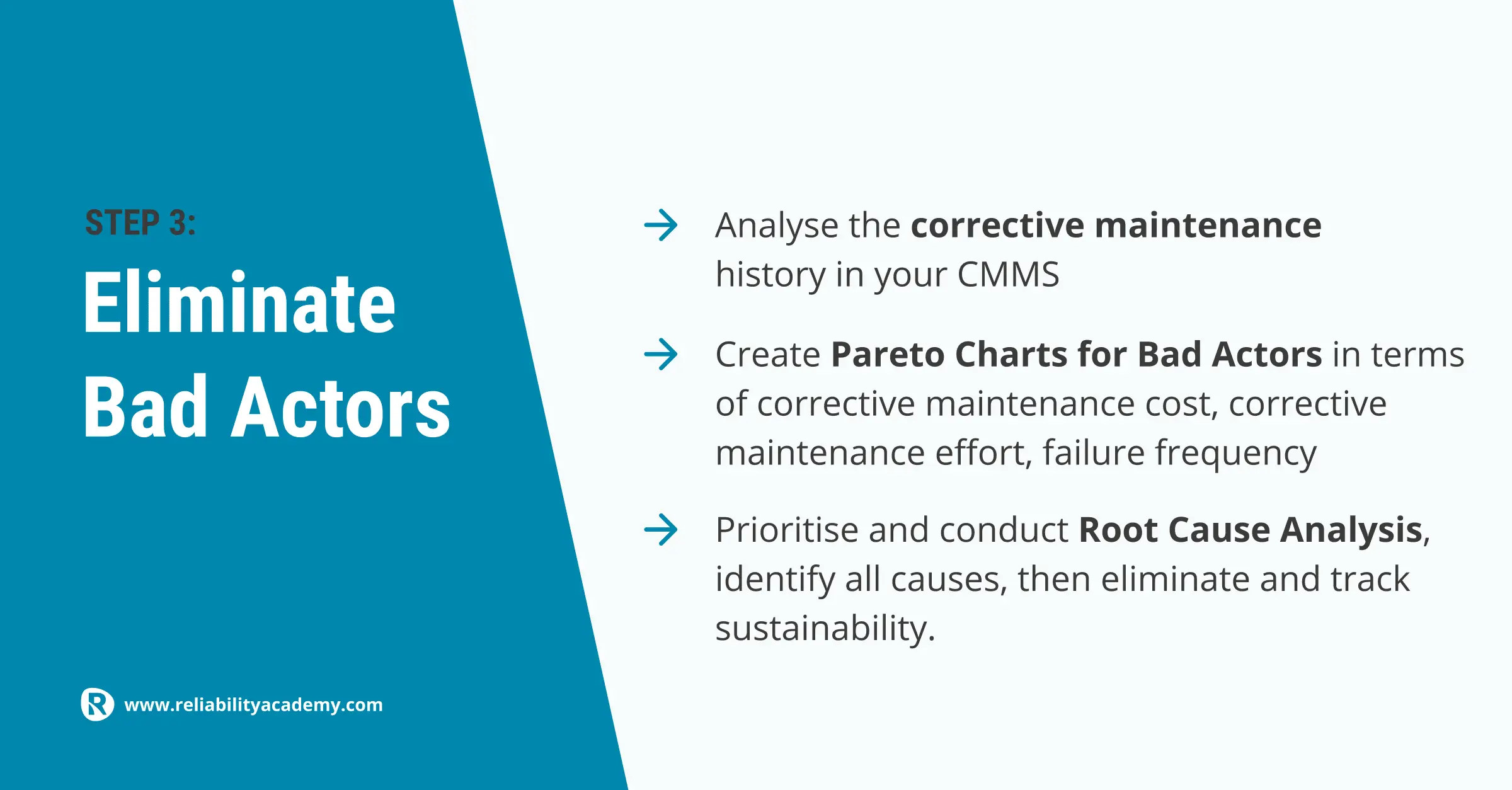
Don’t fall into a trap of staying at the superficial cause level where you end up blaming the operators and the maintenance technician. That happens a lot, but it doesn’t help you solve your issues.
What you want to do is really get down to the process issues, the systems issues and the management issues that are calling for these failures to not be eliminated. And those are the issues you want to fix.
Then you’re going to see significant improvements in your corrective maintenance workload, and you’re going to see significant improvements in your corrective maintenance budget.
Step 4: Improve your maintenance contracts and rates
Now, the fourth step is improving your maintenance contracts and your rates. In this area you should be targeting at least a 5% cost reduction.
Many organisations specify contract requirements that they don’t really need, and guess what—these requirements actually drive up prices.
So what you want to do is review your specifications and requirements, initially internally, but then also together with your suppliers and your service providers.
This is so that you really understand which of your requirements are driving up their maintenance costs.
Then you can see which requirements you can reduce or maybe even eliminate.
There are almost always win-wins possible in this space. Win-wins where you reduce your cost and your supplier actually increases profitability.
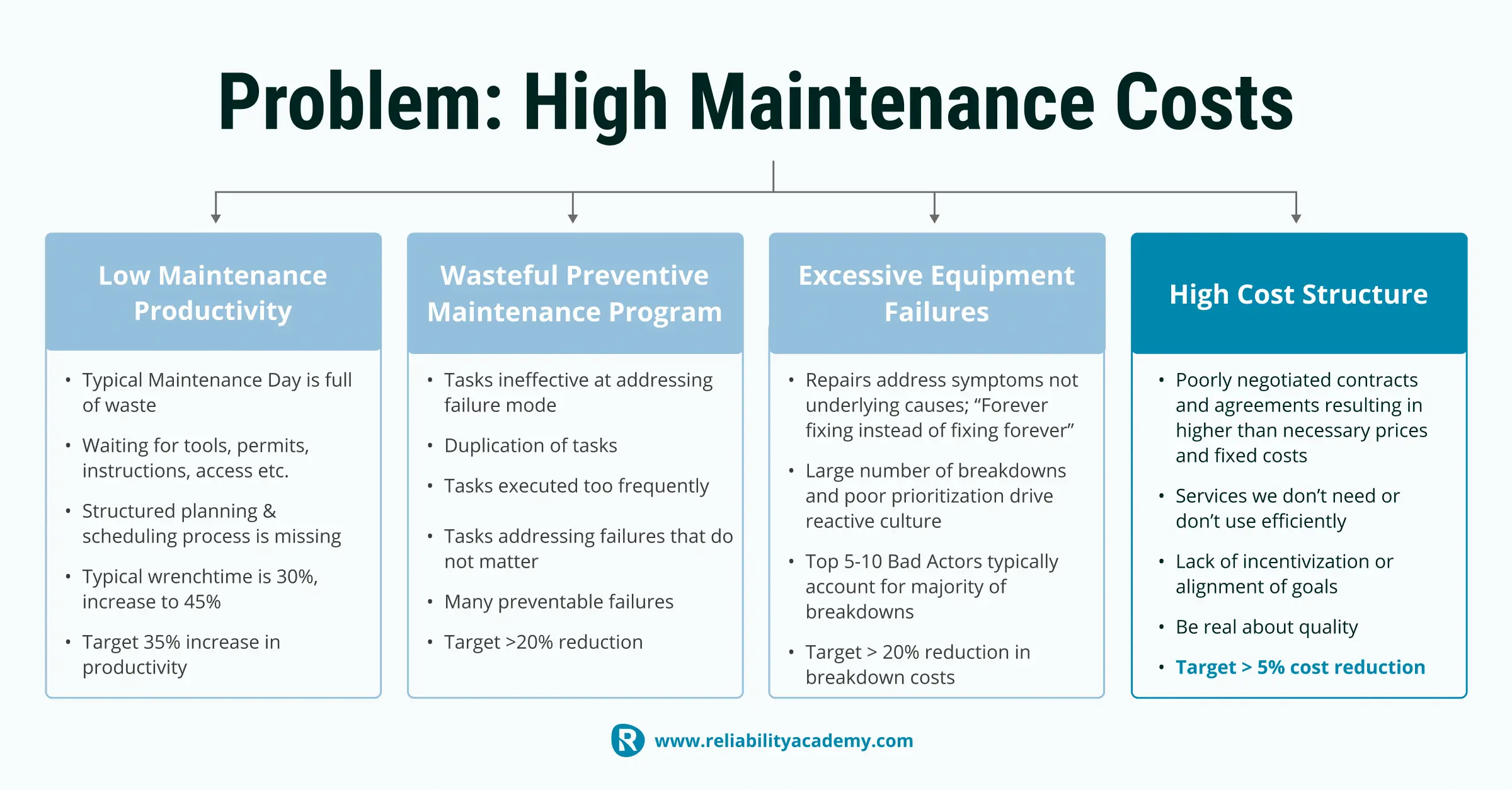
Reduce Maintenance Costs: Step 4 is tackling a high-cost structure by improving your contracts
The next step is to ensure that you structured your contracts in such a way that you incentivise your contractors and service providers to eliminate waste, become more efficient and help you reduce your maintenance costs.
And when you approach your key service providers and contractors, the ones that really matter to your organisation, and you ask them for their help and input, you’ll likely be surprised by their willingness to support your journey.
Good suppliers understand the value of a long partnership.
And if you have key suppliers or key contractors that don’t want to play ball or don’t really want to help you reduce your maintenance costs, well, that’s a telling message.
It’s a telling message that you’re going to have to take some action.
Now, this is an area where you really can, and should, leverage your procurement and contracts team.
Take some pressure off your maintenance team and your reliability team. Reach out to your colleagues in procurement and contracts and get them to help you with this.
It’s important to remember that with all these things, you always need to keep an eye on quality.
You need to stay real about the impact on quality, because you can quickly lose everything you gained when you start getting quality issues.
The bottom line, really, is that you need to work with your contractors and your service providers to eliminate waste across their processes, and then rates and maintenance costs will come down.
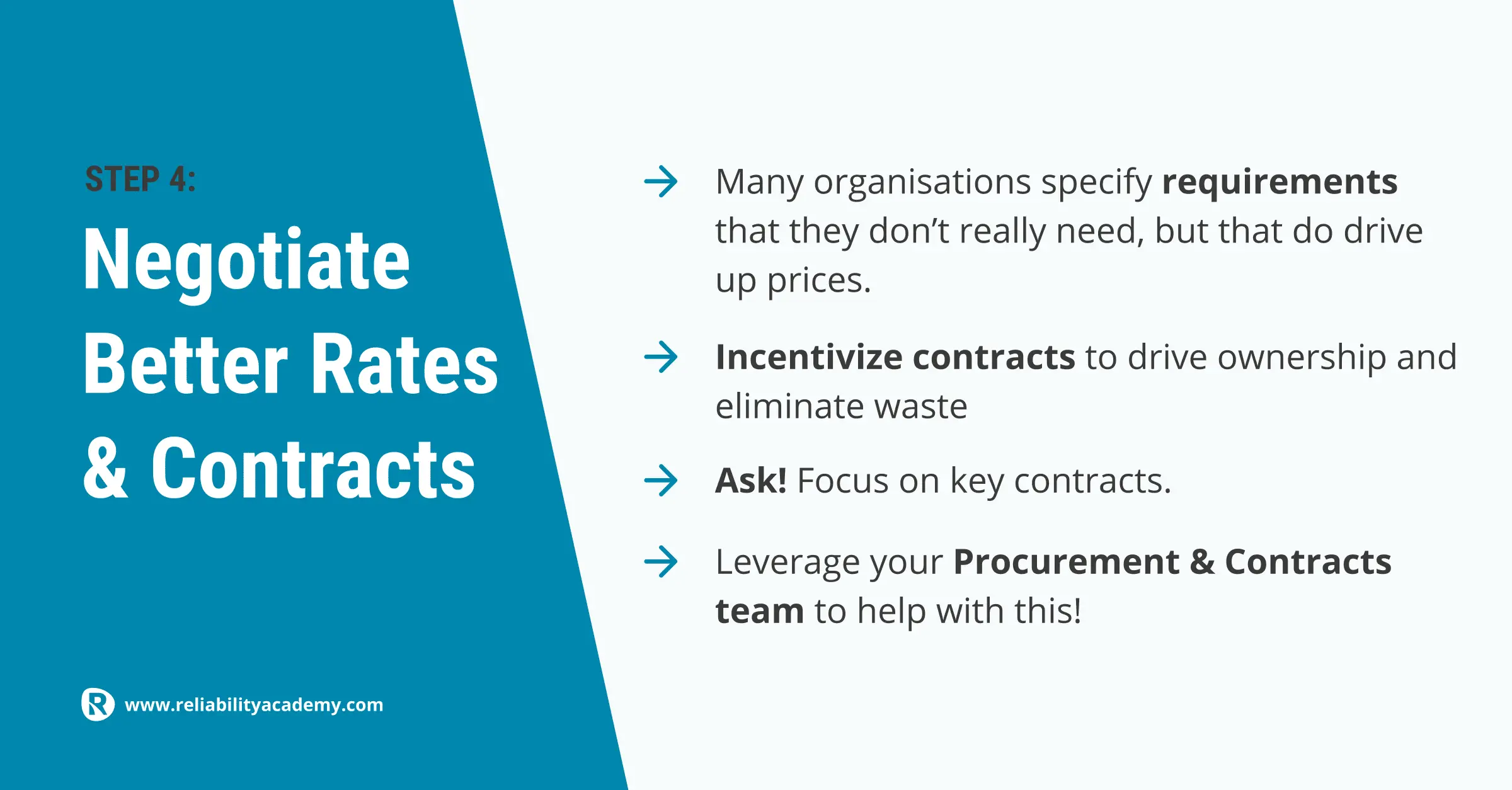
Implementing the 4 steps
Now you have a framework of four steps that will help you reduce maintenance costs in a sustainable manner.
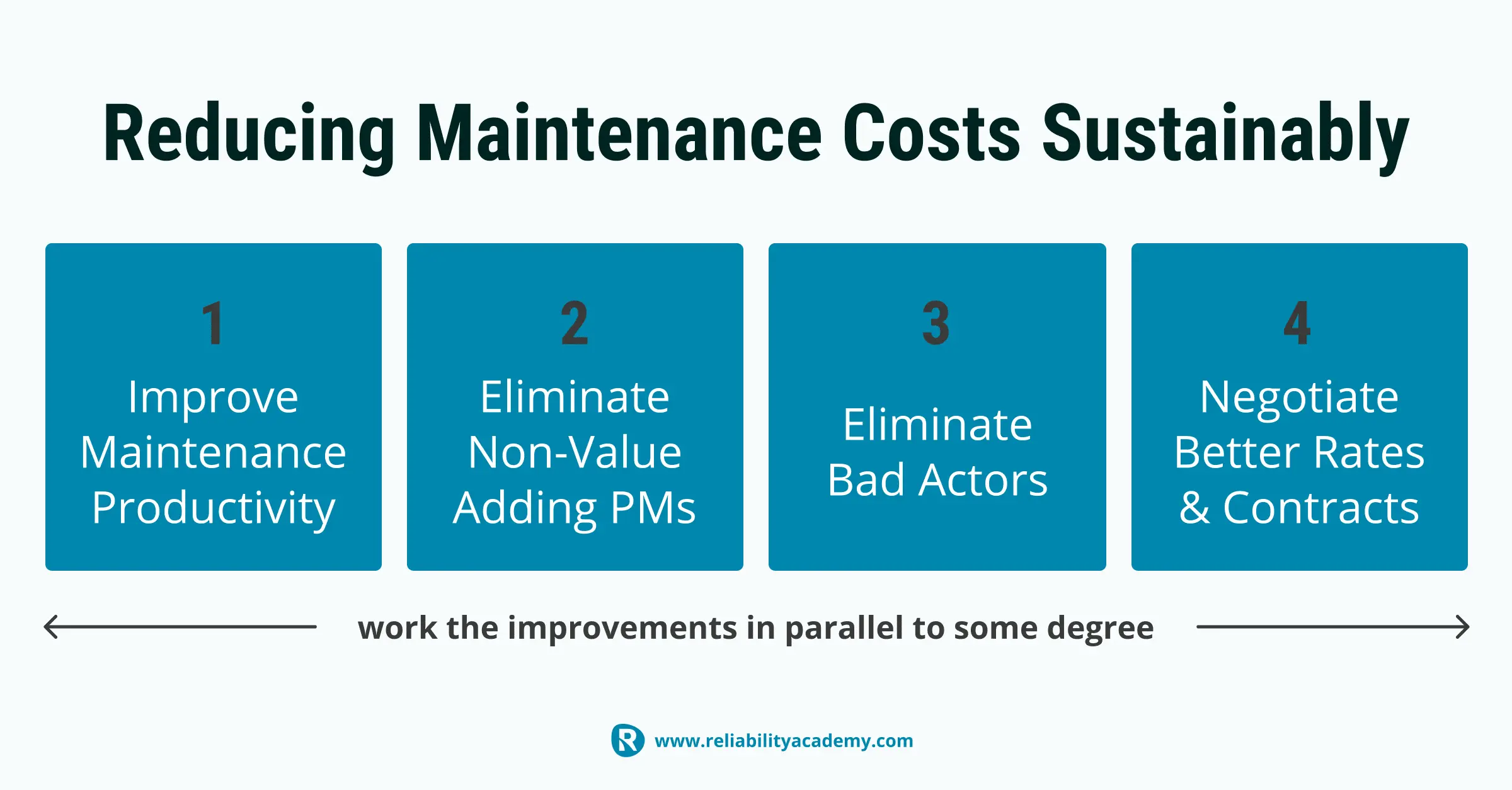
And when you work through this framework, you’ll find that what you once considered impossible, now actually becomes very possible to lower maintenance costs.
And again, the secret here is to understand where your waste is and to tackle that waste. Then your maintenance costs will come down and they’re going to stay down.
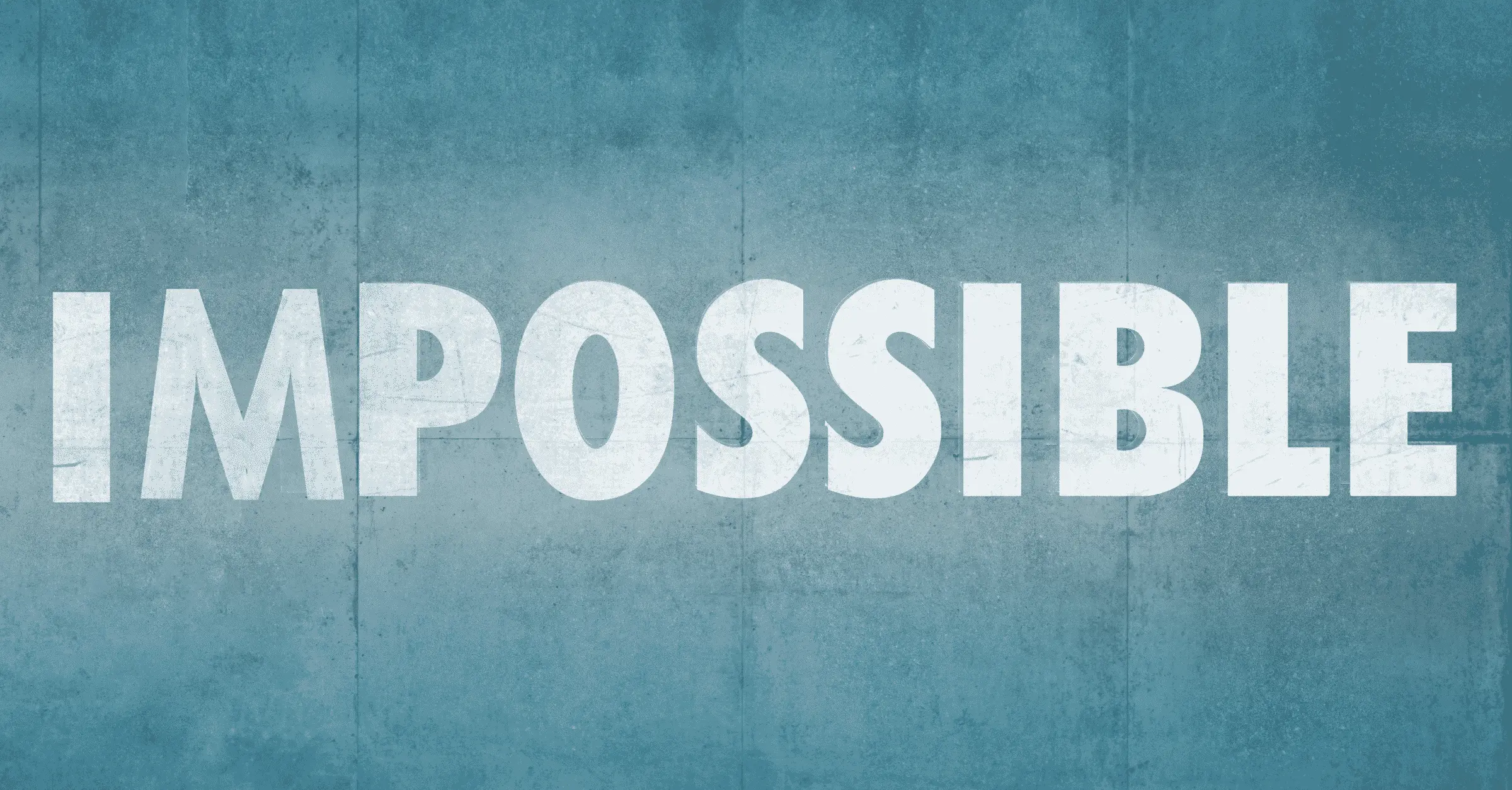
Now, in my last corporate role, I was a maintenance reliability manager for an LNG plant. The annual budget varied between $60 million and $90 million per year, depending on the number of turbine overhauls we had to do.
In that role, I developed a cost-reduction program based on these very principles of improving maintenance productivity, eliminating non-value-adding PMs, eliminating bad actors and negotiating better rates and contracts.
You see, no matter whether you have a big budget or a small budget, the principles really remain the same.
You need to eliminate the waste.
You need to focus on doing the right things and doing them well.
And above all, you need to remember that maintenance costs are a consequence.
They are a consequence of the maintenance you do, and how well you do it.
I normally recommend that you execute these four steps in the sequence that you see here on the screen, starting with improving productivity, because once that’s done, it gives you more capacity to get other improvements done.
Reduce maintenance costs fast
At the beginning of this, I talked about the fact that the pressure on maintenance costs has been increasing.
So what do you do if you’re in a real hurry to reduce maintenance costs?
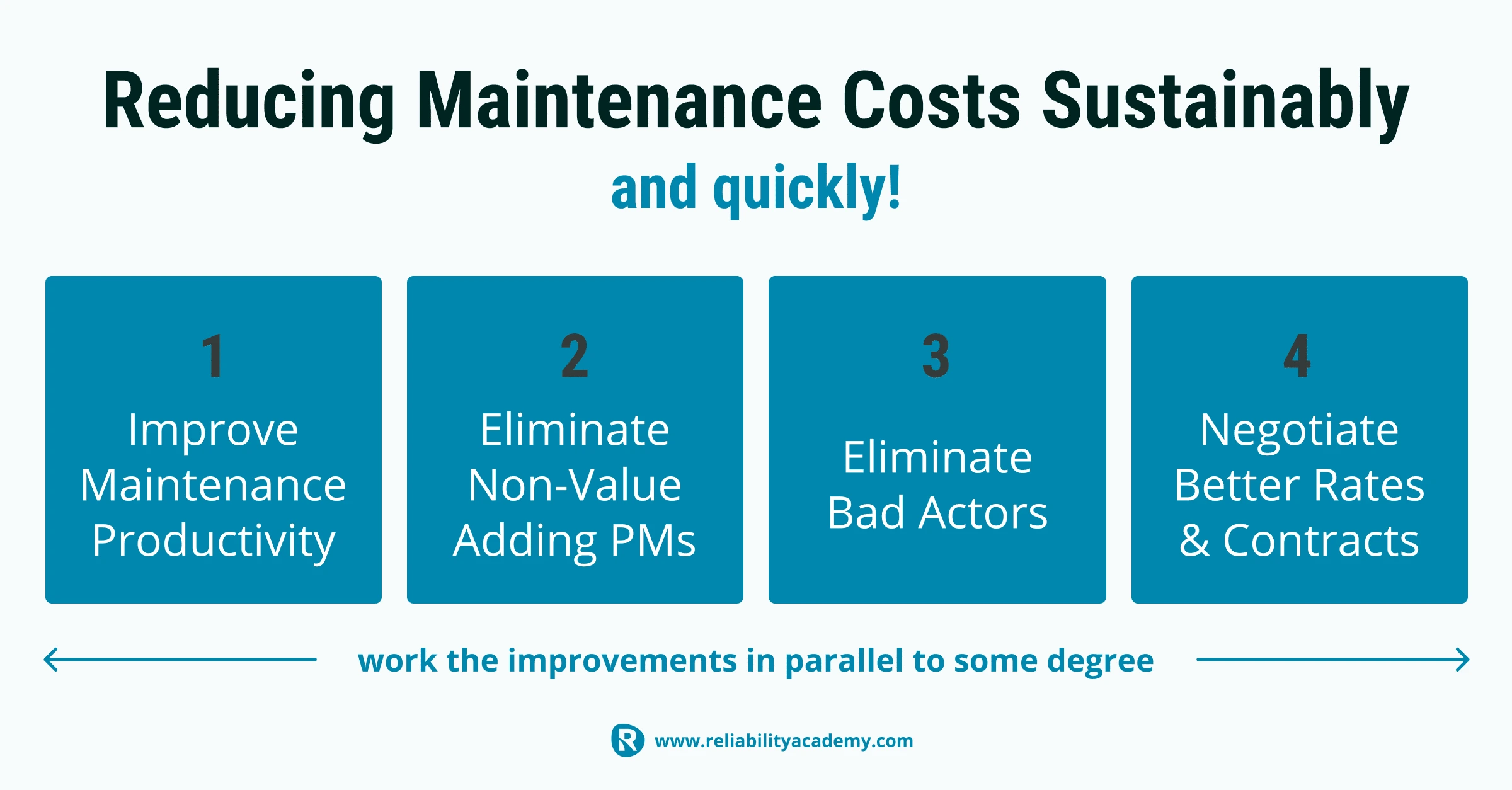
Well, unfortunately, you’re still going to have to do the same work, but you may want to change the sequence a bit if you’re really under pressure. If you’re really in a hurry.
In that case, I would start off with a very focused effort on your PMs and then eliminate all the work that really does not need doing. In the space of one or two months you can probably eliminate 10%, 15%, maybe 20% of your workload.
Next, I would look at engaging a few of your biggest contractors and see if you can renegotiate rates. And in some cases, you may have to give in on some of your standards and specifications. Now be careful when you do this, because as we discussed, you need to watch your quality. But this can often be a quick win.
Because like we said, many organisations routinely specify requirements that don’t really drive value for them, but they do add to the cost of the supplies. So approach the suppliers and ask them. Sometimes these conversations can be really eye-opening.
Now, once you’ve initiated that work—and I say initiate, because you don’t want to wait until it’s finished—you want to start tackling your bad actors.
And once you’ve kicked that off, you want to start looking at your maintenance productivity. I put this last because this typically takes the most amount of time.
Normally I would say it takes a good 12, maybe 18 months to really get a sustainable change in the way you manage your maintenance planning and scheduling because you’re actually changing the way you work.
But…
If the pressure is on, and if you have the leadership support, a strong case for change and motivated, capable personnel, then you can probably break the back of implementing planning and scheduling within six months. You can make significant improvements.
Now, the last point I want to make is that if you’re really under pressure, you want to work these improvements like I kind of hinted at in parallel, but just keep in mind that any organisation can only work on so many things at the same time. And that will also go for your team.
There’s only so much work that they can do. So be selective, and be strategic.
Be amazed by what you can achieve
With all that said, I want to leave you with a quote from Bill Gates, and it is really relevant to everything we’ve just been talking about:
“We tend to overestimate what we can do in one year and underestimate what we can do in ten.”
And that applies especially when it comes to reducing maintenance costs.
You’ll be amazed by how far you can cut maintenance costs down and still maintain, or even improve your performance.
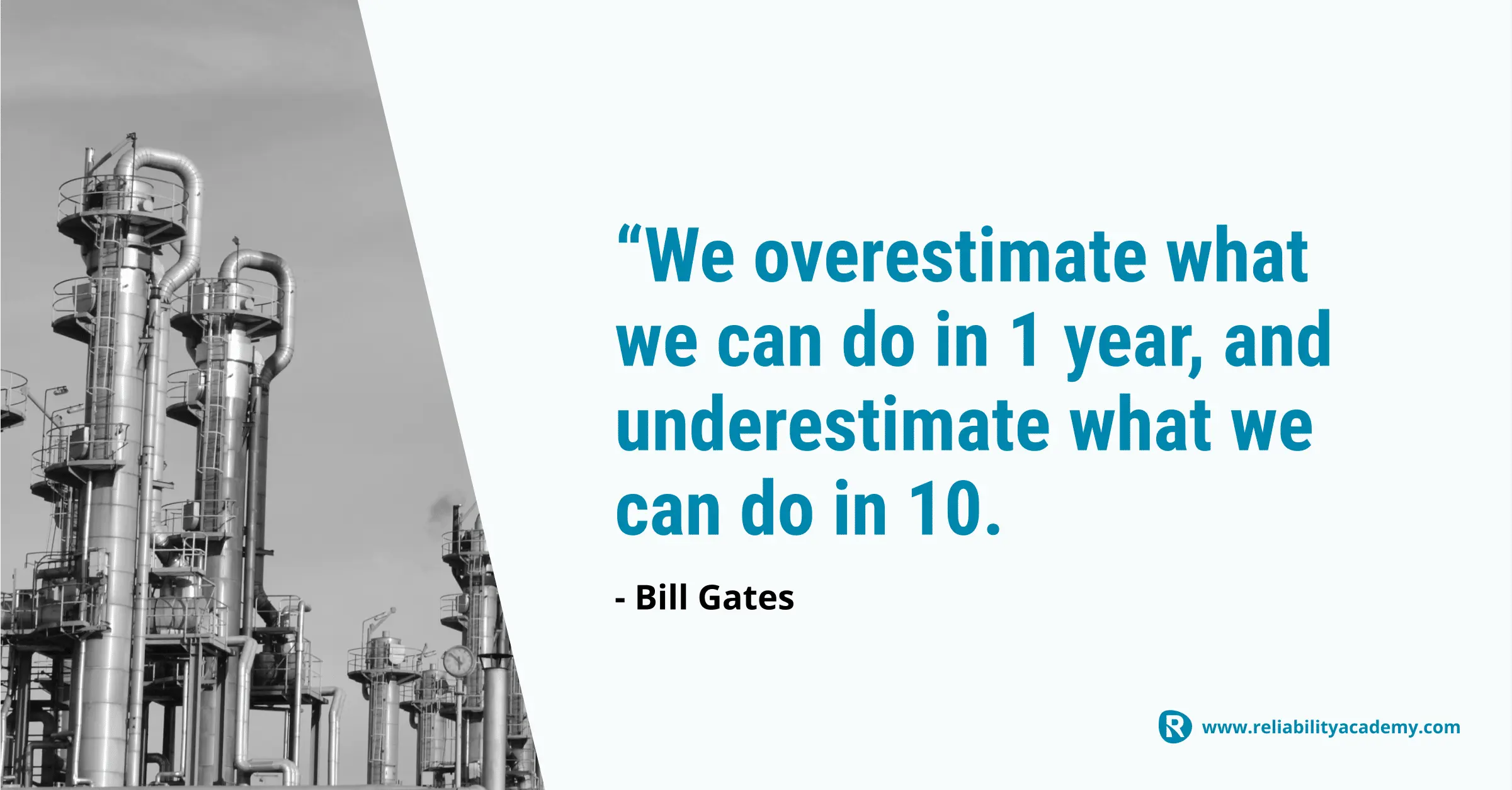
Actually, it turns out that I got this wrong: the full quote from Bill Gates’ 1996 book The Road Ahead says, “We always overestimate the change that will occur in the next two years and underestimate the change that will occur in the next ten. Don’t let yourself be lulled into inaction.”