There’s a big difference between busy and productive.
A lot of times, maintenance technicians are busy juggling hundreds of tasks in a day. They’re busy running around looking for spare parts, sitting down in meetings, taking breaks, or waiting on operations to give them access to equipment. They’re busy. But they’re not getting any productive work done.
Maintenance productivity isn’t just about doing a lot of work—it’s about maximising the time spent on activities that directly improve your plant’s reliability. That’s where “Wrench Time” comes into play.
By understanding and optimising your Wrench Time, organisations can not only streamline their maintenance processes, but also significantly improve their reliability and efficiency. In this article, we’ll discuss what Wrench Time is in more detail, why it matters, and how you can optimise it to enhance your maintenance operations.
Key Takeaways:
- Wrench Time is the time technicians spend working on equipment, as opposed to performing other non-tool-related tasks such as admin work, retrieving parts, or attending meetings.
- Poor Wrench Time and productivity is often caused by the large amount of waste in your maintenance execution. Low productivity doesn’t come from your technicians being lazy. It is the result of an inefficient way of working.
- An effective maintenance planning & scheduling process can increase your wrench time from a typical 30% to somewhere around 45%. This improvement in wrench time is equivalent to increasing your work force by 35%.
- There are generally 4 ways you can measure you wrench time: estimate, indirect, direct, or self-reported.
What is Wrench Time?
When you hire your technicians, you hire them to do maintenance. But in most organisations, maintenance technicians spend maybe a third of their time doing actual maintenance.
Wrench time is simply a measure that shows how much of your technician’s time is being spent doing the actual productive maintenance, the hands-on tool time, as opposed to performing other non-tool-related tasks such as admin work, retrieving parts, or attending meetings. We typically express wrench time as a percentage.
This metric is important because it measures your overall maintenance productivity, and it helps you assess the efficiency of your maintenance teams. Wrench Time impacts everything from operational uptime to maintenance costs. Higher Wrench Time means your maintenance crews are spending more of their shifts on the tools rather than being bogged down by non-value-adding activities. By increasing the actual time technicians spend on maintenance, your organisation can drastically reduce downtime, lower maintenance costs, and improve the reliability and longevity of your equipment. Essentially, better Wrench Time means getting more value out of your maintenance efforts with less waste.
What is a Good Wrench Time?
In the 1980s, DuPont commissioned the largest benchmarking study of maintenance and reliability. It covered 3,500 sites across North America, Europe, and Japan. It was so extensive that it’s still referred to today.
The DuPont study – and many studies since then – have shown that maintenance productivity levels of 20% – 30% are typical across industries. That means you get 2-3 hours actual maintenance time out of a technician working a 10-hour shift. Which is pretty bad.
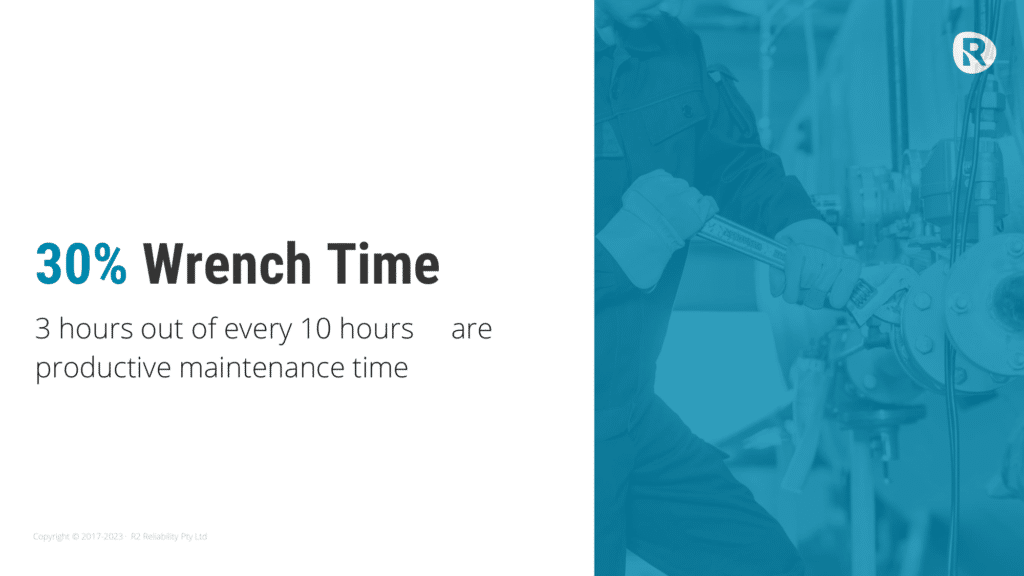
The study also showed that the top 5% of these companies – the “Best of the Best” – do the basics very well. And those basics included Planning and Scheduling.
By implementing an effective planning and scheduling process, you can improve your maintenance productivity to 45%. And this is equivalent of increasing your workforce by 35% without hiring more people.
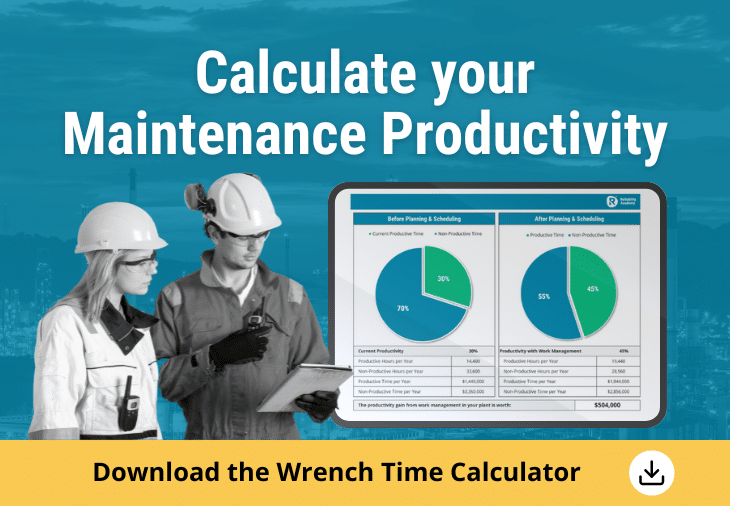
How Waste Occurs in Maintenance Execution
Your wrench time is typically impacted by the amount of waste in your maintenance execution. Let me discuss that visually using this simple timeline of what a typical day of a maintenance technician looks like.
Let’s assume we have a maintenance crew that works a 12-hour shift from 6:00 AM in the morning to 6:00 PM in the evening.
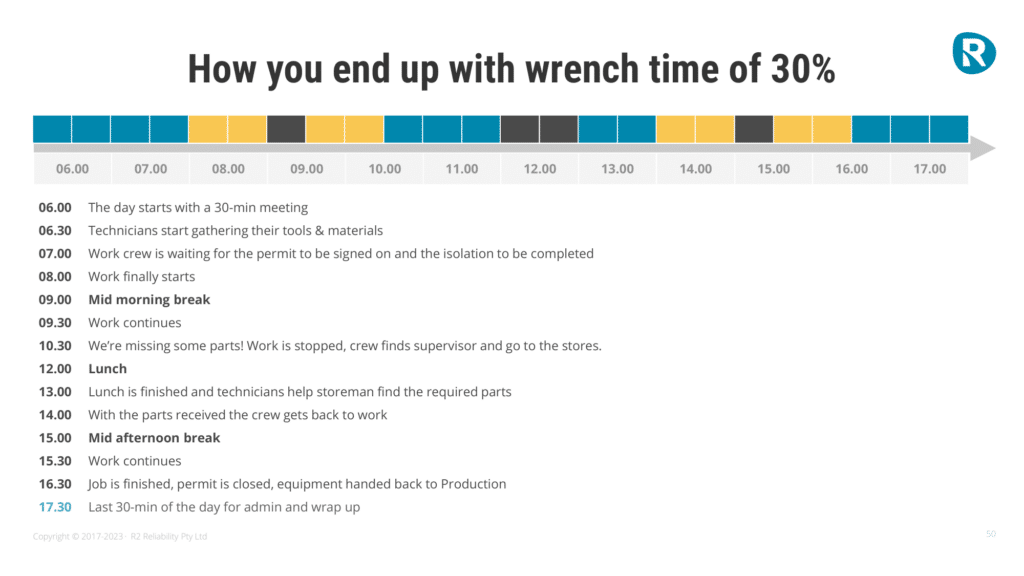
In this timeline, we list down all the activities that typically happens in the day of your technician, and we’re going to apply a simple color code.
- Yellow for productive maintenance, when our technicians, are actually doing maintenance work on the equipment
- Blue is for non-productive time when our crew is in meetings, waiting for something, looking for parts, etc.
- Black, we’ll use for breaktime. Mid-morning breaks, lunch time, and mid-afternoon breaks.
Now, when you look at this timeline, it’s absolutely full of non-productive time. And when I only show the productive time, it becomes even more clear.
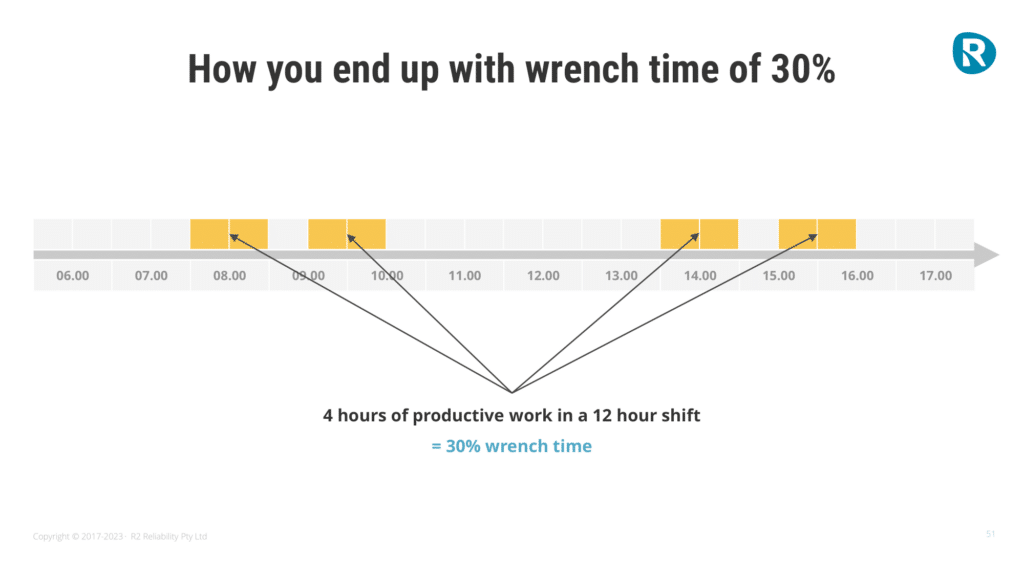
Our crew was very busy, but they weren’t very productive.
Now, to be clear, they weren’t slacking, they only took breaks when they were allowed to. They never had longer breaks. They were always working hard, trying to do the right things. But they only got about four hours of actual maintenance done in their 12-hour shift. And four productive hours out of a 12-hour shift, would give them a wrench time of just about 30%, which as we discussed, is pretty much average across the industry.
This low productivity is not because your crew is lazy. The low productivity is the result of an inefficient way of working. All those delays came about because this was a reactive maintenance organisation that did not run an effective planning and scheduling process.
Common Causes of Waste in Maintenance Execution
Now, what I showed in that timeline were just a few types of waste. But there’s many types of waste that can occur in a maintenance organisation. And when you look at that list, you’ll probably recognise many of them.
- Waiting on permits
- Waiting on isolation or de-isolation
- Finding tools
- Getting spares and materials
- Locating additional spares / materials
- Having to organize access e.g. scaffolding
- Having to organize lifting / rigging
- Having to find another trade to support
- Travel to / from site
- Excessive break time
With an effective maintenance planning and scheduling process, you can minimise these delays and increase your productivity to around 45%. And if you get to world class levels, you’re going to probably look at wrench times of 50 to 60%.
Measuring Wrench Time
If you want to improve your wrench time, your first must know your current wrench time. By setting this as your benchmark, you can see whether your improvement efforts are working. Now, before we discuss measuring your wrench time, I want to warn you about two important things:
- The first is that wrench time is very important. But wrench time says nothing about doing the right work or doing the work right. So keep that in mind. Doing the right work and doing it right, but with lower productivity is going to be much more valuable to your organisation than being very efficient in doing the wrong work or doing the right work wrong. So remember that.
- The second health warning is to compare wrench times carefully. People quote all kinds of wrench times and productivity numbers. However, if you’re not using very similar definitions and similar wrench time assessment methods, you are likely comparing different things and that can lead to all kinds of incorrect conclusions. It is much better, therefore, to assess yourself quarterly or annually and analyse your own improvement trends instead of comparing with peers, unless, you really use the exact same methodology.
With all that said, let’s look at how you can assess your productivity.
Now, there are 4 main ways to assess your maintenance productivity.
1 – Estimate Your Wrench Time
The first method to assessing your wrench time is by estimating your productivity using a simple tool like our wrench time calculator. This is a crude tool for estimating wrench time. It’s inaccurate, but it’s fast and easy.
And you can strengthen your assessment by involving your maintenance supervisor, your operations supervisor, a couple of technicians, your planner, and scheduler, and do it in a team environment. That way you can get a shared view of where your current productivity sits.
This method works well to build a case for change to start implementing or significantly improving planning and scheduling, but it’s not robust and detailed enough to do repeat measurements for continuous improvement or for benchmark.
2 – Indirect Measurement of Wrench Time
The second method is indirect measurement using other metrics like the number of work orders completed, the number of hours liquidated, backlog growth, and time writing non-productive hours.
These metrics can give you an idea of your productivity, but they don’t really give you a productivity number. But by analysing the trends, you can draw important conclusions about what’s happening to your productivity and wrench time. However, you must adjust those metrics for crew size because it can change over time.
3 – Direct Measurement of Wrench Time
Now, although the most accurate, this method is not always your best option. Direct measurement can be very invasive and can be experienced as quite threatening by your crew. So don’t do it unless you have a mature culture.
There are 2 ways to do a direct measurement of your wrench time:
Continuous Time Observation Method. Also, sometimes called “day in the life of”. With this approach, you have an observer monitoring a worker for their full shift and everything they do is recorded, whether he or she’s working, having lunch, taking a break, looking for parts, talking to the supervisor, or needing to go to the bathroom.
Multi-Moment Observation (MMO) Method. In some ways you could consider this a less intrusive way to measure wrench times. In this approach, observers now follow multiple workers from a distance at predetermined time intervals and then note down what they’re doing. Are they working productively? Are they waiting? Are they traveling to or from site? Are they getting job instructions or are they on a break? And before you start the study, you need to create a randomly generated list of people to observe. This way, every technician has an equal chance of being observed and you’re not distorting the study.
4 – Self-reported
The last approach to measuring your wrench time will be what we would call self-reported. This requires your technicians to track their time. There are many tools and apps out there that can help with this. Unfortunately, this approach has many drawbacks and is not very reliable in terms of the data it provides. With this approach, the wrench time data that is being reported is usually much higher than it really is. Now, you can do this, but you probably need to be a very mature organisation with years of wrench time studies and reporting before you go down the self-reporting route.
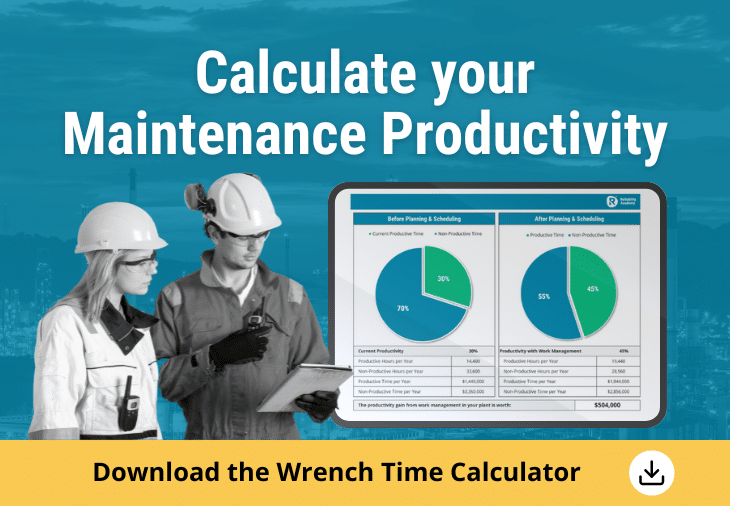
Improving Wrench Time through Maintenance Planning & Scheduling
Maintenance Planning & Scheduling is one of the 4 Essential Elements on the Road to Reliability™. Planning & scheduling, or work management as it’s often called, ensures the right work gets done, at the right time, with the right tools, materials, and people.
Without an effective maintenance planning & scheduling process, you’ll never achieve high reliability or high wrench time. That’s because an effective maintenance planning and scheduling process can drastically reduce the amount of waste in your maintenance execution—waste that typically occurs during and between jobs.
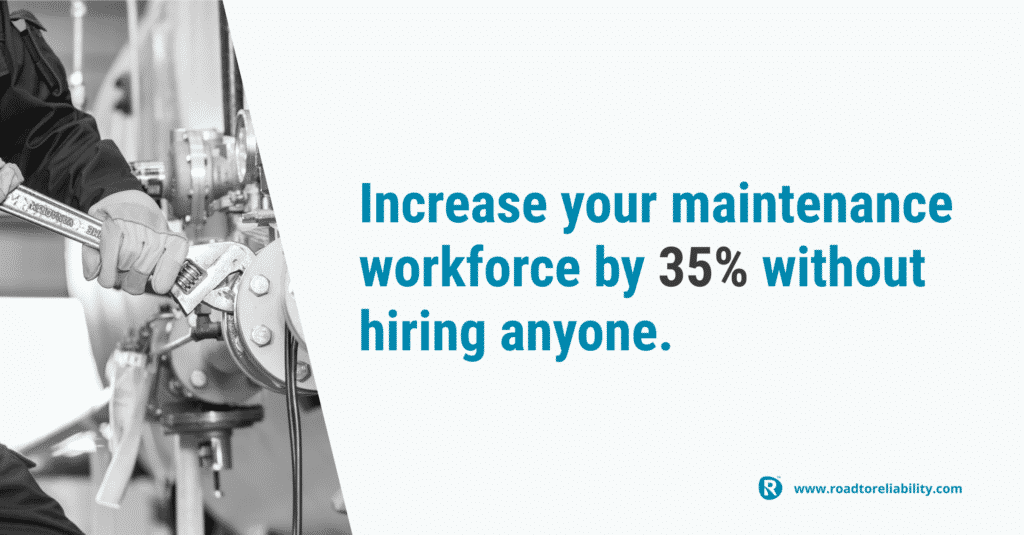
Maintenance Planning & Scheduling is pretty easy to understand. But a lot of organisations still suffer from poor wrench times. That’s because plenty of organisations still commit the same mistakes.
By training and educating your team on how to effectively implement maintenance planning & scheduling in your organisation, you can increase your workforce by up to 35% without hiring more people. And to some organisations, that translates to millions of dollars in savings per year.
Conclusion
Wrench time is the amount of time your technicians spend doing actual productive maintenance. The average wrench time across industries is around 30%, which is pretty bad.
Improving Wrench Time is important for achieving higher maintenance efficiency. Understanding the factors that influence this key metric and implementing strategies to improve it, you can significantly improve your organisation’s reliability while reducing costs.
By implementing an effective maintenance planning & scheduling process, you can increase your wrench time to around 45%. Which is the equivalent of increasing your workforce by 35% without hiring more people.
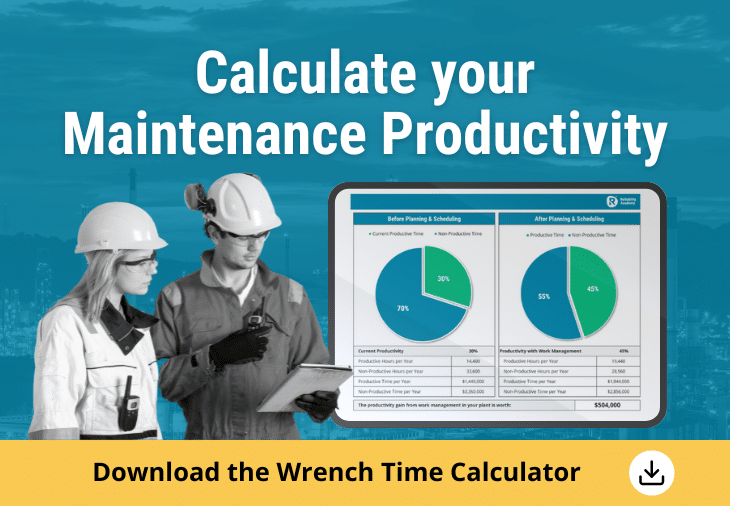