The concept of Lean has been around for a long time, but the concept of lean maintenance is not talked about that much. There are a few books written on the topic, but if I’m honest not enough is written about lean maintenance considering how important it actually is in our journey towards higher reliability.
I won’t talk in detail about what ‘lean’ is and isn’t, there are plenty of sources about that elsewhere. In simple terms, just like how being physically lean means removing excess fat and toning our body’s muscles…
In maintenance, being “lean” means 2 things: we look for ways to reduce as much waste and inefficiencies as possible; and continuously improving our work processes.
If your work processes have huge amounts of waste and inefficiencies, it will often cause your team to produce loads of unproductive work (which they often get blamed for).
That’s why if you want to achieve a Reliable Plant, it’s important that you eliminate these wastes from your processes.
The first thing you need to do is to locate and identify where the waste is coming from. Here are 3 major sources of waste in maintenance that you can start looking into:
Waste in Day-to-day Maintenance Execution
This could be in the form of…
- Meetings
- Looking for parts
- Waiting on permits
- Waiting on instructions
- Waiting on other trades
- Waiting on Operations to isolate the equipment
And as you’ve noticed, there’s a lot of time wasted on waiting.
Most organisations achieve a maintenance productivity of about 25% to 30%, simply from being inefficient with how they plan and schedule their tasks .
This means about 70% of the time, you are paying for unproductive work.
To solve this, you must have an effective Maintenance Planning & Scheduling process in place. And, you must effectively implement it in your organisation.
Waste in Preventive Maintenance
In Preventive Maintenance, waste comes from doing preventive maintenance tasks that aren’t actually worth doing.
In fact, experience and research show that even nowadays 40% – 60% of the tasks in a Preventive Maintenance program aren’t actually adding value.
Some of the most common problems here are:
- Tasks are duplicated.
- Tasks are done too frequently or not frequent enough
- Tasks are not effective at addressing the failure mode
- Lack of using existing failure data and experience to set good task frequencies.
Just imagine doing daily maintenance inspection on a piece of equipment that was, in reality, unnecessary.
Or replacing a part every 3 months, when it would have been fine replacing it on the onset of failure (which could be years down the line).
If you want to create an efficient preventive maintenance program, it should be following 9 principles of modern preventive maintenance.
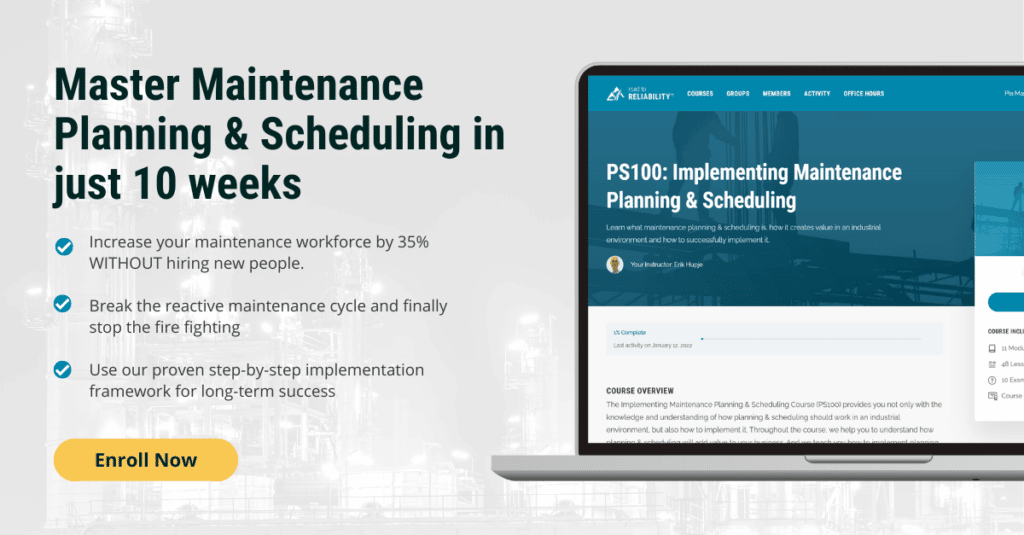
Repeat Failures
Finally, another common form of waste in maintenance environments is the “forever fixing” mindset.
It’s when organizations don’t fix the sources of equipment failures. Instead, they opt to keep fixing those same failures over and over again.
Instead of fixing it forever, they are forever fixing.
See, there are plenty of defects that you cannot eliminate through maintenance.
These defects cause your equipment to fail, no matter how many times you fix the equipment.
Yet many organisations simply plan for the failures, but not the root cause of the problem.
They write job plans.
Hold extra spares.
And when the failure happens again, they fix it.
They hope that with each repair, they are getting faster and more efficient.
But this is where the waste happens.
It’s like fixing your car’s AC every month because it kept breaking down—but you didn’t look for the root cause of the problem.
It’s the same thing in our plants.
And what’s sad about this, is you might not even realize it. Because about 80% of failures that occur in a plant have occurred before.
Meaning, that plenty of the failures you’re experiencing can be avoided by having a defect elimination process in place.
Summary
In summary, lean is about removing as much waste from your work processes.
If your work processes have huge amounts of waste and inefficiencies, it will often cause your team to produce loads of unproductive work.
As such, there are 3 major sources of waste that you can start with:
- Day-to-day maintenance execution
- Preventive Maintenance
- Repeat Failures
By eliminating these waste from your work processes, you are on your way to creating a more productive and reliable plant.