Maintenance Planning & Scheduling (MPS) is one of the key elements of a reliable plant. When done right, it increases your workforce productivity by at least 35%, reduces downtime, and eliminates the chaos of reactive maintenance. Yet somehow, so many organisations fail to successfully implement this process. Even when organisations train their teams, bring in consultants, or adopt new software, they often struggle to make this process stick.
In this article, we’ll break down why most planning & scheduling efforts fail, the common mistakes organisations make, and what you can do differently to make sure your implementation succeeds.
Why Do Implementation Efforts Fail?
First, let’s look at the overall implementation.
Even if you implement a proven and tested maintenance planning & scheduling process, there are 2 key reasons why you would still fail during implementation.
Reason #1: Underestimating the Challenge of Changing the Way People Work
Implementing a new planning & scheduling process isn’t just about improving your team’s efficiency—it’s also about changing the way your entire organisation works.
You’re not just changing the roles of planners and schedulers—you’re impacting everyone involved: managers, supervisors, technicians, operators, and more. It’s a ripple effect that requires buy-in at every level.
Yet many organisations fail to approach MPS as a change management project. Instead, they treat it like a process update and expect people to adapt automatically.
They don’t.
If you don’t actively manage resistance to change, communicate the “why” behind the new process, and provide the right support—your efforts will simply fall flat.
Reason #2: Lack of Discipline and Maturity to Stick to the Process
Many organisations know what they should do—but they don’t actually do it.
A plant manager in the US once told me, “I wish we did what you taught us to do in your course.”
They had invested in our online training program. They knew the right process. But they didn’t stick with it.
This happens all the time. Companies start strong, but as soon as resistance builds or daily operations get in the way, they fall back into old habits.
If leadership doesn’t hold the team accountable, and if your team doesn’t own the process, you will often default to reactive firefighting—no matter how good the training or the process.
The reality is, MPS isn’t just about knowledge or process. It’s also about discipline and commitment over time. That’s why it is so important to have the right coaching and accountability in place, which I’ll talk more about later in this article.
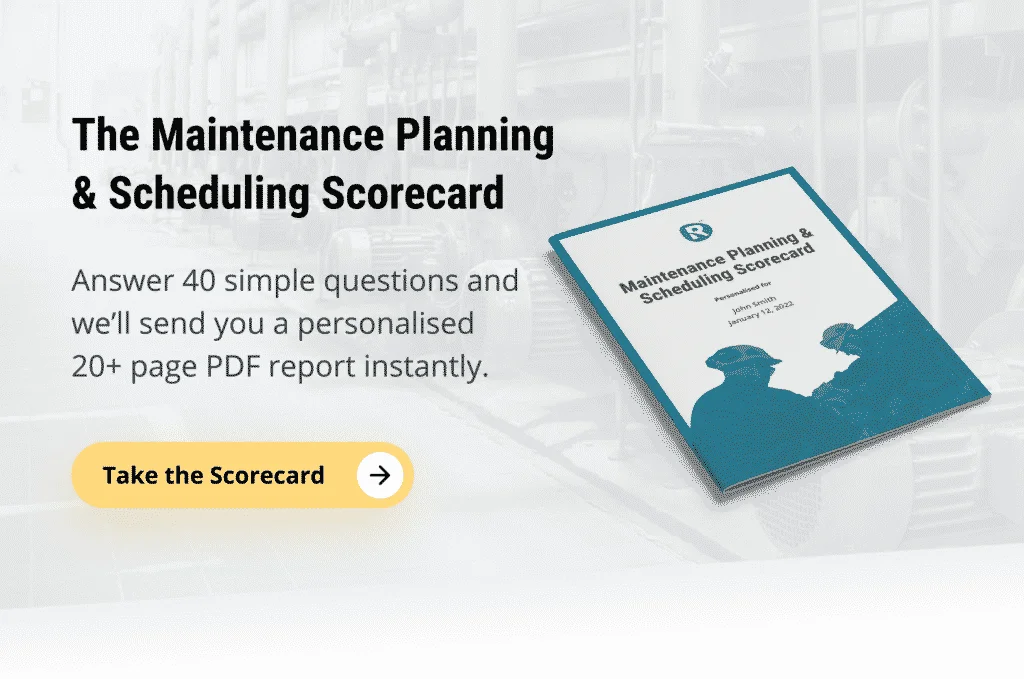
The 13 Maintenance Planning Mistakes
Beyond poor implementation, many organisations make critical mistakes in the maintenance planning & scheduling process itself. Here are 13 common mistakes you need to avoid during maintenance planning:
Mistake 1: Picking the Wrong Person as Your Planner
Many organisations fail before they even start by choosing the wrong person for the planner role.
The maintenance planner is one of the most critical roles in a maintenance organisation. A good planner increases workforce productivity, makes sure jobs are properly prepared, and reduces waste. A bad planner leads to poor job plans, inefficiencies, and frustration.
Among other things, planners must have:
- The right attitude – They must be proactive, detail-oriented, and committed to improvement.
- Strong technical knowledge – While they don’t need to be the best technician, they must understand maintenance processes.
- Organisational skills – Planners must coordinate materials, tools, and resources efficiently.
Get this wrong and you’ll end up with poorly prepared work and an ineffective maintenance planning process. As a result, the productivity of your crew won’t go up or not by much. In fact, it could even go down.
Mistake 2: Not Training Your Planners Properly
Even if you hire the right person, they won’t be effective if you don’t train them properly.
Planners need to understand:
- How to use the CMMS
- How to develop detailed job plans and work packs
- How to source materials and parts
- How to collaborate with schedulers and supervisors
Without proper training, planners will lack consistency and create low-quality job plans. This will negatively impact the work of your technicians and ultimately affect your team’s productivity.
Mistake 3: Using Your Planner as a Relief Supervisor, Expeditor, or Troubleshooter
One of the biggest, and most common mistakes when it comes to maintenance planning is that, in many plants around the world, maintenance planners aren’t actually planning.
Instead, planners often end up being a combination of a planner, a relief supervisor, an expediter, an administrator, and an all-around troubleshooter. And guess what? When you ask a planner to do all that, he or she won’t be spending much time planning.
That means you’re not going to get the productivity gains that you’re looking for.
So remember, a maintenance planner must never work for the current week. A maintenance planner must always be working for future weeks.
Mistake 4: Using Planners for Emergency Work
Planners should never be involved in emergency work. That’s the supervisor’s responsibility.
Because planners know where everything is, it’s tempting to ask them to jump in during a crisis. But every time they do, they’re pulled away from planning future work, which keeps the team stuck in reactive maintenance.
Make your maintenance supervisor accountable for emergency work. And just to repeat myself because it’s that important: remember that your planner should always be working for future weeks, never for the current week.
Mistake 5: Planning from Behind a Desk
Once your maintenance planner has been in the role for quite some time, a sense of “knowing-it-all” can slip in. It’s common for a planner to think:
“I know this job. I used to work on that machine myself. I know exactly what it will take to get this repair done. I can plan this job right here from my desk.”
Let me tell you right now: Always visit the job site.
There will always be things going on in the plant that might have changed the situation. And consequently, planner might miss some things that need to go into plan. That could be a safety issue or an access issue. Things change, and people sometimes forget. When you plan from behind a desk and you miss these things, you lose efficiency, you introduce waste.
So remember, planning is not a desk job.
Mistake 6: Poor Sequencing of Resources and Materials
Planners need to make sure that all the resources and materials in the work order and work pack are properly sequenced.
If not, you will find your mechanics hanging around while the electricians are still putting the electrical isolation in place. Or worse, you’ll find your mechanics all around the plant looking for electricians to put that electrical isolation in place.
That’s not efficient. So, make sure your planner breaks down all the steps of a job plan and puts those into the CMMS.
Mistake 7: Incomplete and Poor-Quality Job Instructions
A bad job plan forces technicians to stop work, track down missing information, and figure things out on their own.
Clear, complete job plans should include:
- Step-by-step instructions
- Required materials and tools
- Safety precautions and permits
- Equipment diagrams, manuals, and specifications
A well-planned job lets your technicians execute the work without delays or confusion.
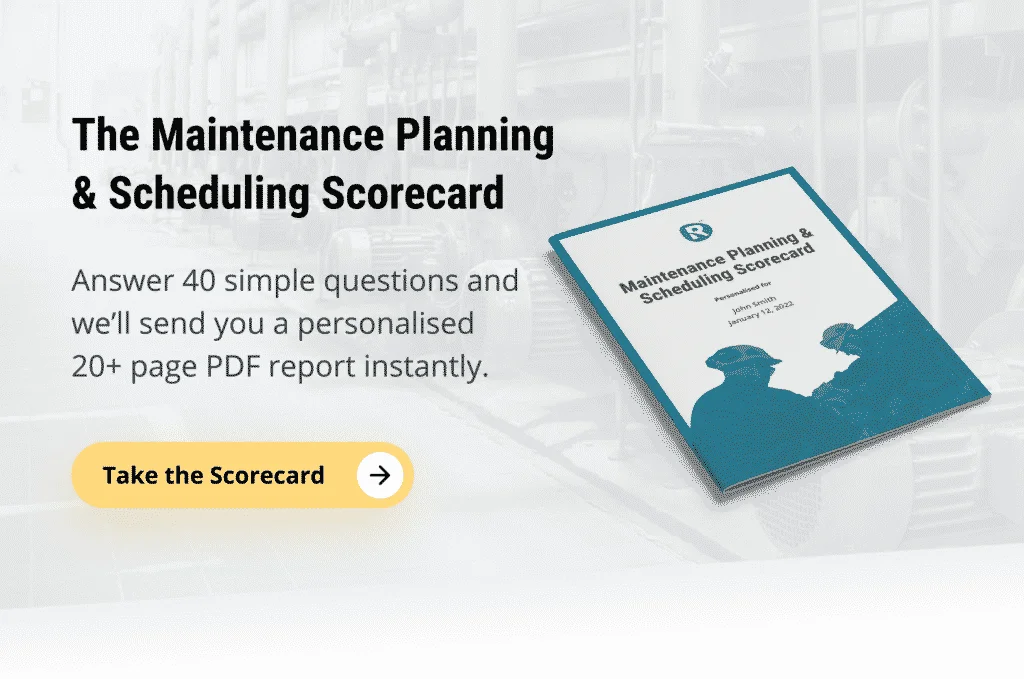
Mistake 8: Not Providing Feedback to Planners
Once your technicians finish a job, you need to make sure they capture good quality history in your CMMS and provide accurate feedback to your planner.
If planners never receive feedback on job plans:
- Mistakes will be repeated.
- Inefficiencies will persist.
- Technicians will disengage from the process.
I recommend that your planner adds a feedback form to specific job plans and work packs. The technicians then complete those forms and the planner can review them together with the supervisor before improving the job plans.
Mistake 9: Not Kitting and Staging Work
A fully planned job is useless if technicians don’t have the right materials, tools, and equipment ready to go.
Without kitting and staging:
- Technicians waste time searching for parts.
- Jobs get delayed due to missing materials.
- Execution efficiency drops significantly.
Planners should work with warehouse staff to verify that all materials are available and properly staged before a job is scheduled.
Mistake 10: Not Acting on Feedback
Asking for feedback is pointless if planners don’t act on it.
If technicians take time to provide feedback but nothing changes, they will stop bothering—and the feedback process will stagnate.
Your planners must:
- Review feedback regularly.
- Update job plans accordingly.
- Communicate changes to technicians so they see that their input matters.
Mistake 11: Not Properly Managing the Backlog
Managing backlog is not easy especially if you have a lot of backlog and you’re in a reactive maintenance environment.
A poorly managed backlog creates:
- Overdue work that never gets scheduled.
- Missed opportunities to group jobs efficiently.
- Shutdown inefficiencies where critical work is forgotten.
The secret is to keep your backlog clean:
- Make sure that work that has been done is actually closed out completely and doesn’t show up in your backlog.
- Make sure that work orders that are fully planned are marked accordingly in your CMMS.
- Don’t set work to ready to execute if the job is not fully planned or if the materials have not yet been confirmed to be on site.
Mistake 12: Using the Wrong Metrics
Many organisations track the wrong KPIs or overload their teams with too many metrics.
You really want to put most of your focus on analysing and getting feedback from your maintenance crew. The feedback you get from your technicians on the quality of the job plans is the best indicator you have for planning quality and planning performance.
However, that typically is a qualitative measure. If you want to get a quantitative measure in place, then I strongly recommend you focus on estimating accuracy as a performance metric.
Only when you have these 2 key metrics understood and under control should you consider adding additional metrics.
Mistake 13: Undervaluing Your Planner
A planner is just as critical as a maintenance supervisor. Yet, many organisations fail to respect or properly support their planners.
If a planner feels undervalued:
- They will disengage from the role.
- They will leave, bringing with them the organisational expertise they honed over time, which may lead to instability in the team that they will leave behind.
- The organisation will struggle to find a replacement.
Investing in planners, training them properly, and giving them the authority to drive the process is essential for long-term MPS success.
‘Shortcuts’ That Hinder Progress
The truth is, implementing MPS in a reactive organisation without the right mindset and skills can be extremely challenging. So, what do organisations do when they struggle with MPS? They look for shortcuts.
Instead of fixing process discipline and leadership accountability, they invest in expensive software or bring in high-priced consultants hoping for a quick fix.
But software alone won’t fix a broken process.
If planners aren’t actually planning and schedulers aren’t enforcing discipline, even the best technology won’t help. Moreover, hiring consultants to do the work for you means your team never learns to own the process themselves. What happens then when those consultants leave? The process unravels!
Instead of shortcuts, your organisation need to focus on:
- Training and coaching your own team
- Building discipline and accountability
- Developing a sustainable internal process
The Importance of Training & Coaching
If you want to avoid implementation setbacks, process mistakes, and you don’t want to resort to ‘shortcuts’ that don’t work, then you need to properly train and coach your team.
Training is important to shift mindsets and build skills in your team to avoid those costly mistakes. Coaching, on the other hand, builds accountability to make sure your team owns the process and implements what they learned during training.
Now, there are two levels of coaching required for a successful MPS implementation:
- Coaching the Team During Implementation – Helping planners, schedulers, and supervisors execute the process in real time.
- Coaching the Implementation Leaders – Training those responsible for rolling out MPS so they stay on track, remove obstacles, and enforce discipline.
This is where our Tool Time Sprint™ comes in.
How the Tool Time Sprint™ Helps You Implement MPS the Right Way
The Tool Time Sprint™ is a 12-month live training and coaching program designed to help maintenance teams successfully implement and sustain Planning & Scheduling.
This program doesn’t just teach theory—it guides your team through the process step by step, making sure they develop the discipline and accountability to make it work.
Through live coaching, hands-on training, and structured implementation support, your team will:
- Learn how to plan & schedule effectively
- Develop the habits and discipline needed to sustain it
- Increase tool time and maintenance productivity
- Build a culture of proactive maintenance
If you’re serious about getting MPS right and avoiding the common mistakes that lead to failure, let’s talk.
Schedule a call to learn more about the Tool Time Sprint.
Final Thoughts
Most Maintenance Planning & Scheduling efforts fail not because the process doesn’t work, but because organisations struggle to implement it properly.
By understanding why MPS implementations fail, avoiding common mistakes, and investing in the right training and coaching, you can build a sustainable, high-performing planning and scheduling process.
If you’re ready to take your MPS implementation seriously, the Tool Time Sprint™ can help. Schedule a call today to learn how to make Planning & Scheduling work for your team.
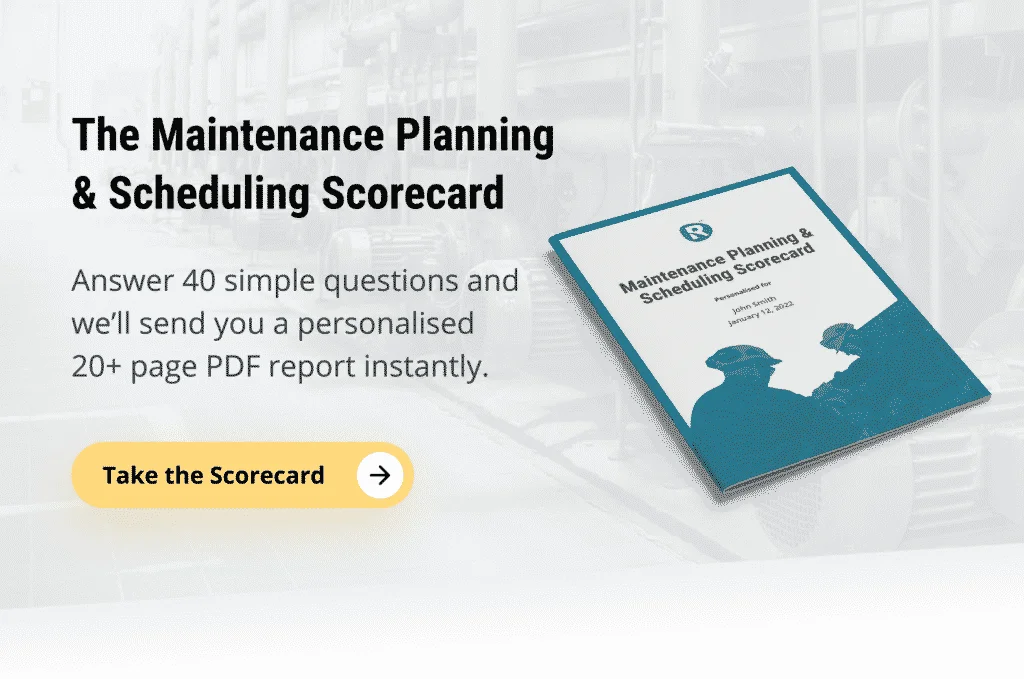
TAG: PLANNING & SCHEDULING