The 5 Types of Preventive Maintenance
At a high level, all maintenance is either preventive maintenance or corrective maintenance. As a maintenance practitioner, you need to match the right type of maintenance with the characteristics of the failure mode you're dealing with. And you need to pick the type of maintenance that suits your objectives. In this article, we will discuss the 5 different types of preventive maintenance.
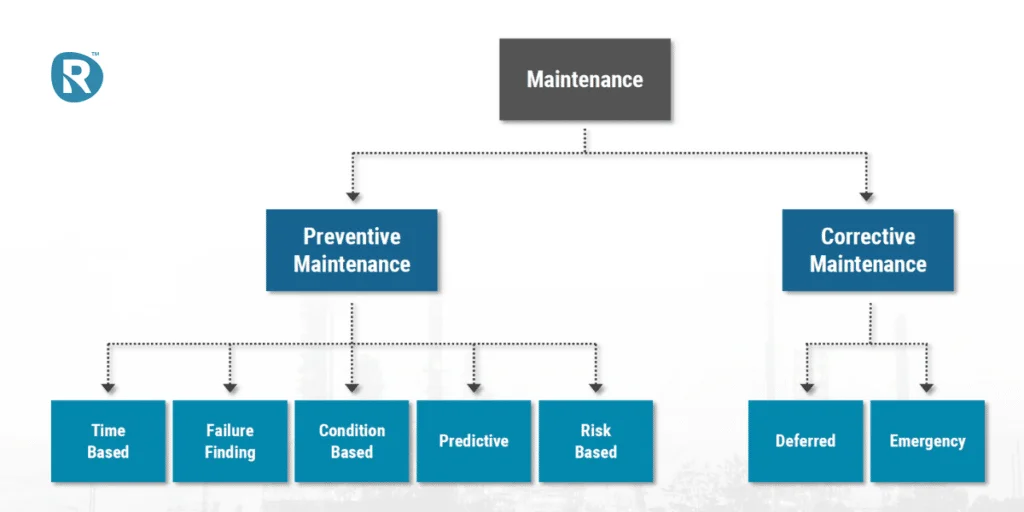
Keep in mind that there is no ‘best’ one-size-fits-all type of maintenance. An effective and efficient preventative maintenance program will always consist of a mixture of the different maintenance types.
What is Preventive Maintenance?
Preventive Maintenance are maintenance tasks done before a failure has occurred. And they are aimed at preventing a failure, minimising the consequences of failure, or assessing the risk of the failure occurring. It doesn't have to be more complicated than that.
What are the 5 types of Preventive Maintenance?
There are 5 different types of preventive maintenance:
- Time-based maintenance
- Failure-finding maintenance
- Condition-based maintenance
- Predictive maintenance
- Risk-based maintenance
Let's discuss each one in greater detail.
Time-based Maintenance
When people talk about preventive maintenance as a whole, they're actually often referring to time-based maintenance.
This refers to replacing or renewing an item at a fixed time, interval or usage, regardless of its condition.
Example: Every month, every 100 hours or every 10,000 kilometers, you replace a part or you service it with the expectation that you significantly increase its reliability.
It is only effective when you're dealing with failure modes that are clearly age related or for dealing with compliance or regulatory requirements where you have a time commitment.
Failure-finding Maintenance
This type of preventive maintenance is aimed at detecting hidden failures. These are typically associated with protective functions. Think about pressure safety valves, trip transmitters and the like. This type of equipment won't be required to function until something else has failed.
That means under normal operating conditions, you'll not know whether this equipment is still functional, i.e, the failure mode is hidden. And as these failures are hidden, you'll need to find them before you can rely on that equipment to protect you.
It's important to realize that failure finding maintenance tasks do not prevent failure. They're aimed at detecting. And once you detect it, you will then have to repair the failure you find. Failure finding maintenance is conducted at fixed time intervals, typically derived from legislation or risk based approaches.
Condition-based Maintenance
Most failure modes are not age-related. However, most failure modes do give some sort of warning that they are in a process of occurring or about to occur. So if we can find evidence that something is in the early stages of failure, it may be possible to take action or prevent it from failing completely, or minimise, avoid the consequence of it.
So condition-based maintenance looks for physical evidence that a failure is occurring or is about to occur. Thinking of condition-based maintenance in this way, shows that it has broader applications outside of the condition monitoring techniques that are often only associated with rotating equipment. Condition-based maintenance is much more than the typical vibration monitoring that a lot of organisations do. Now, it's important to realise that condition-based maintenance does not reduce the likelihood of a failure occurring.
Instead, condition-based maintenance is aimed at intervening before the failure occurs on the premise that it's more economical and should have less of an impact on availability. In other words, condition monitoring does not directly fix machines nor does condition monitoring directly stop failures. Condition monitoring lets you find problems before they become a failure. You then need a follow-up task to make an intervention.
Predictive Maintenance
When people spoke about predictive maintenance, this was essentially a synonym for condition-based maintenance, especially in North America. But things have changed. In my view with the advent of artificial intelligence, much lower cost of equipment sensors and machine learning…
…there's really a difference appearing between predictive maintenance and what some people might call "prescriptive maintenance", and the more conventional condition-based maintenance. At least in my view. See, I see predictive maintenance or prescriptive maintenance, as some call it, as an extension, a more advanced approach to condition-based maintenance.
Predictive maintenance is a type of maintenance where we use potentially many process parameters gained from online sensors to determine if our equipment is moving away from stable operating conditions and heading towards failure. And sometimes it may not even be a direct condition measurement.
So, this does mean that predictive maintenance is only effective when you really understand the failure mode you're dealing with and you have various direct or indirect measurements that you can use to determine if a failure is becoming imminent.
It is also something that is typically only applied to more complex failure modes or failure modes with fairly significant consequences because of the costs and the complexity involved with predictive maintenance.
Risk Based Maintenance
Risk based maintenance is when you use a risk assessment methodology to assign your scarce maintenance resources to those assets that carry the most risk in case of a failure. That risk is the product of likelihood and consequence.
So as a result, equipment that has a higher risk and a very high consequence of failure will be subject to more frequent maintenance inspection. On the other hand, low-risk equipment may be maintained at a much lower frequency and possibly with a smaller scope of work. When you implement a risk-based maintenance process, effectively you have reduced the total risk of failure across your plant in the most economical way.
Risk based maintenance is essentially preventive maintenance where the frequency and the scope of the maintenance activity is continuously optimised based on the findings from testing or inspection; and a thorough risk assessment. So some examples of risk-based maintenance that you're probably familiar with would be risk-based inspection as applied to static equipment like vessels, piping, tanks, pressure relief valves.
So, those were the 5 types of Preventive Maintenance.
Remember that you need to match the right types of preventive maintenance with the characteristics of the failure mode you're dealing with. And you need to pick the types of preventive maintenance that suits your objectives.
An effective and efficient preventative maintenance program will always consist of a mixture of the different maintenance types. If you want to read more about Preventive maintenance, then you can read this article about the 9 Principles of a modern preventive maintenance program.