As maintenance practitioners, we have a responsibility to maximise our scarce maintenance resources. Especially since maintenance is often subject to tough budget cuts. We need to be as efficient as we can when it comes to our preventive maintenance. That’s why good preventive maintenance programs and maintenance strategies don’t try to fix everything. They are risk-based.
In this article, I want to discuss what Risk-based Maintenance (RBM) is all about. I’ll share with you how I worked with teams of experts to use Risk-based Inspection (RBI) in our maintenance plan to reduce inspection workloads by up to 40% in different plants around the world. And how we did so with already limited resources.
What is risk-based maintenance? Simply put, it is a type of preventive maintenance where you assign your scarce maintenance resources to your most critical assets that carry the most risk of asset failure or high risk assets.
A risk based maintenance plan maximises your limited resources. Assets that carry high risk of equipment failure should be subject to more frequent maintenance tasks and inspections. And lower risk equipment may be maintained at a much lower frequency and scope of work. Risk based maintenance systems are unique because both the frequency and the scope of maintenance are continuously optimised. And this optimisation is based on the findings from your actual maintenance and your risk assessment.
Let me explain this visually.
Risk-based Inspections
Let’s assume we have six pieces of equipment shown below, where we have the results of their initial maintenance inspections.
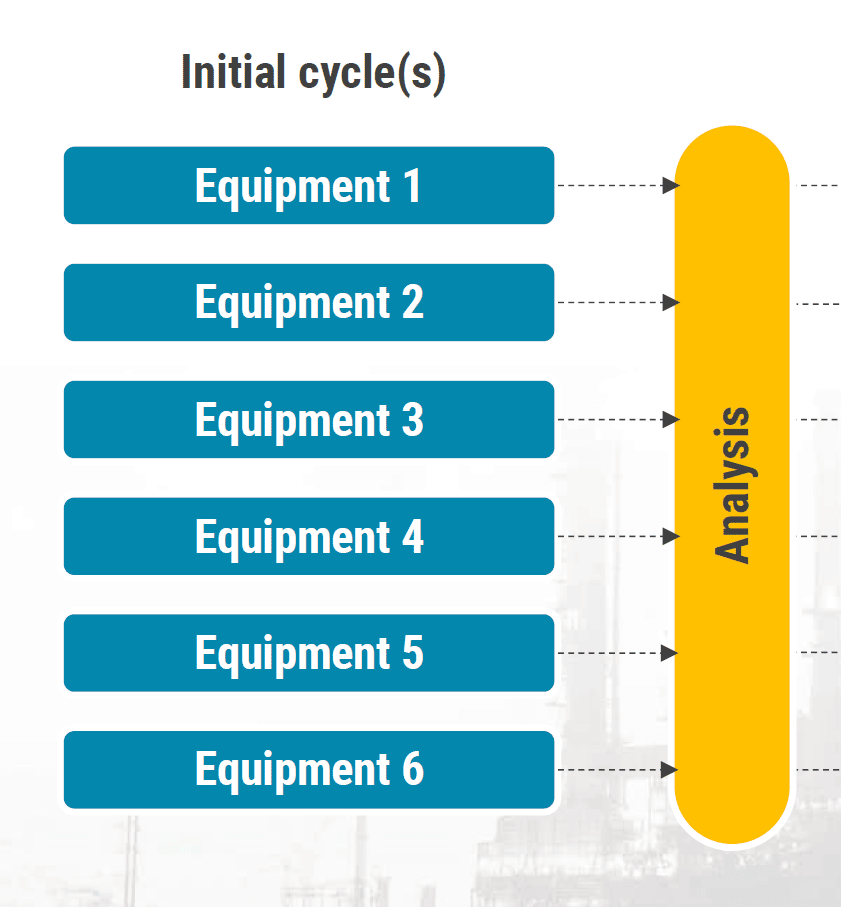
Through a risk-based assessment, we then evaluate whether we need to…
- keep doing inspections at the same frequency and the same scope of work,
- or whether we can extend the frequency
- or reduce the scope of work,
- or potentially reduce the frequency and increase the scope of work orders.
Based on our initial maintenance inspections and risk assessment, let’s say we found a couple of things that should be changed for the next cycle—
Equipment 1 – We’re quite concerned about a certain asset failure mode, and we want to inspect it much sooner than we had intended. Not only that, but we’re also no longer concerned with some failure modes. So the scope is actually somewhat reduced.
Equipment 2 – We’re actually not so concerned anymore. And we decide to extend the interval and reduce the scope of work orders.
Equipment 3 – We need to collect data to make a reliable assessment, but we’re not that concerned that we decide to accelerate the next inspection. So we keep both the frequency and the scope of the inspection the same.
Equipment 4 – When we analyzed the equipment, we realised that the asset failure modes we’re inspecting for simply are NOT applicable in our operating context. So we removed this inspection from our program completely.
Equipment 5 – This is similar to equipment two, in that we’ve decided to extend the inspection interval, and we are going to reduce the scope of the inspection somewhat.
Equipment 6 – Based on the maintenance data, we discover that the rate of deterioration is actually less than we thought. So, we extend the inspection interval. But this time, we are actually concerned that it could apply to more components of the equipment. So the scope is expanded.
From these findings, our next cycle would then look like this.
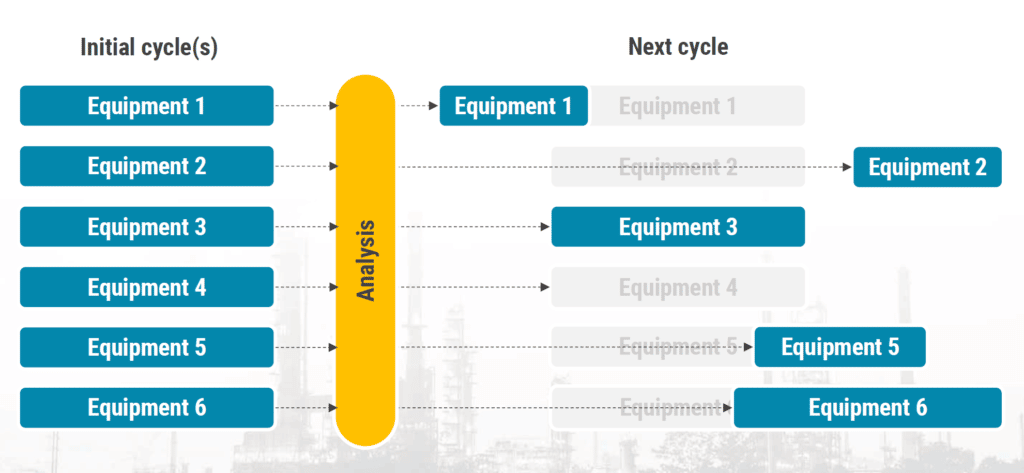
All this simply means is that the scope and frequency of your maintenance plan for the next cycle changes according to the findings from your previous cycle and risk assessment. By doing this type of maintenance, you make the most of your maintenance resources. And you give enough focus to your high risk assets.
The Problem with Risk-based Maintenance Strategies
Now, a common problem you might encounter is that, after a while, all your maintenance and inspection tasks can end up all over the place (like the one above). So instead of having all your inspections neatly every three years, you have them all spread around.
And when these inspections require equipment shutdowns and potentially plant shutdowns, that can become a really complex issue. This is when you hear people say, “All right. Well, let’s stop this RBI nonsense. We have shutdowns every four years. So let’s just inspect everything every four years.”
Sure. That’s easy, very easy. But it’s not wise from a business perspective. Because that way, you will never move beyond your yearly, two yearly or four yearly outages. So you really do want to apply the risk-based maintenance principles in your maintenance plan.
How do you solve this problem?
Now looking at our overall equipment condition and the target date for the outage. We really want to defer our outage to align with the required dates for equipment five and six represented by the red line here.
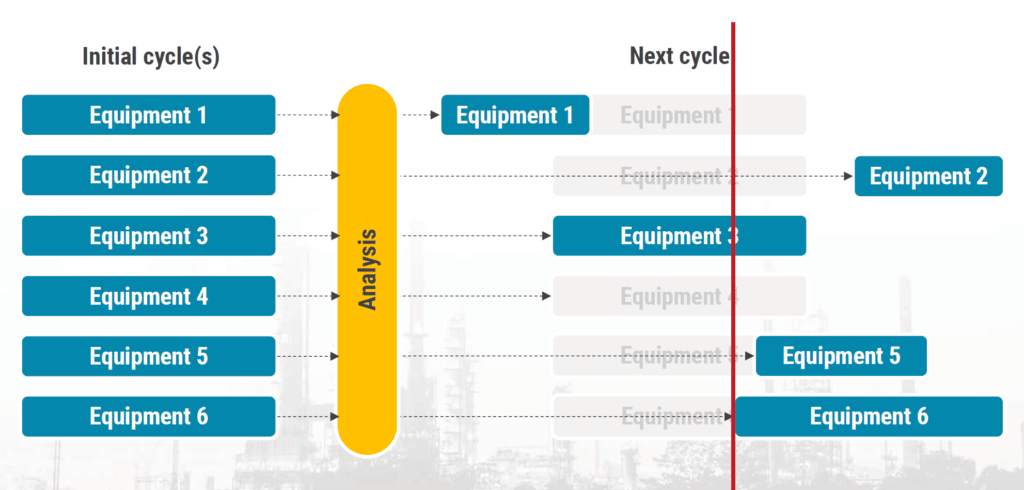
But the concerns around equipment one and three won’t let us do that without doing more work in our maintenance plan. So now it’s time to see if there’s any additional inspections or mitigations we can come up with that might allow us to move equipment one and three further to the right. On careful review, we may conclude that we really need to collect data for equipment one to be able to assess its condition. So, we can’t really do much.
We had planned to get a visual inspection during our next cycle, but since we’ve moved that target date to the right represented by the red line, that will be too late. We’re not comfortable moving it that far to the right. So we come to the conclusion that we will need to do something different.
Non-intrusive inspection techniques
On review, we find that actually we could use a much more advanced, non-intrusive inspection technique in our maintenance plan. This technique doesn’t involve entering the vessel, or equipment/plant shutdowns. But this non-intrusive inspection technique would be a lot more expensive (which is why it was never done before).
But if we spend the extra money on this more advanced technique, we collect data we need. And if we get positive results, we may actually defer the internal visual inspection until the new date shown by the red line. So this is all about risk management and an economic trade-off in a sense.
Is the value of deferring the outage to the new target date (represented by the red line) sufficient to justify doing this expensive non-intrusive inspection early?
What does this all mean?
This might all seem complicated and theoretical. But this is exactly how we used Risk-Based Inspection (RBI) to reduce inspection workloads by 30% – 40%. We used a combination of extension of inspection frequencies, as well as reducing the inspection scopes. So doing less work, less frequent.
By using maintenance strategies like RBI, with advanced non-intrusive inspection techniques, we were able to extend outage intervals in the past. And it was a win on all fronts.
It was good for the companies I worked with because we kept producing for longer.
- We deferred the shutdown.
- It was good for personal safety because we eliminated several man entries into certain vessels.
- And it was good for process safety as we got a much better understanding of the integrity of the equipment that we inspected by these more advanced inspection techniques.
There are different approaches for RBI both quantitative and semi-quantitative and there are various external industry standards that describe RBI including API through API580 and API581.
The Biggest Benefit
In complex continuously operating plants, often the biggest benefit of implementing risk based maintenance plan for the business is not so much the reduction of the work and maintenance costs… but the reduction in downtime and asset failures. For example…
Inspecting pressure vessels is often done during shutdowns, often full plant shutdowns. And very often the pressure vessel inspections are on the critical path of the shutdown. So when you reduce the inspection scope of work, you can typically reduce the length of your shutdown. And that is often worth a lot of money.
And although many of us are familiar with a risk-based approach for inspecting pressure equipment, you can apply the same principles to other categories of equipment too e.g. pressure relief valves or certified electrical equipment. We discuss this in much more detail in our new online training course, Developing & Improving Preventive Maintenance Programs.
Summary
We have scarce maintenance resources. That’s why we need maintenance strategies that allow us to assign them to critical assets that carry the most risk of failure. This is what risk based maintenance strategy is all about. Risk based maintenance systems are unique because both the frequency and the scope of maintenance are continuously optimised based on the findings from your actual maintenance and your risk assessment.
A common problem when you implement risk based maintenance is that all your maintenance tasks and inspection tasks can end up all over the place, instead of being neatly organised every few years. That can become a really complex issue when inspections require equipment shutdowns and potentially plant shutdowns.
To solve this problem, see if there are any additional inspections or mitigations you can come up with that might allow you to move equipment further to the right of the schedule. It might be worth spending extra money on more advanced inspection techniques so you can actually defer the internal visual inspection to a more convenient date.
This is all about risk management and an economic trade-off in a sense. In complex continuously operating plants, often the biggest benefit of risk based maintenance strategy is not so much the reduction of the work… but the reduction in downtime.
When you reduce the inspection scope of work, and focus on equipment that have the most risk, you can typically reduce the length of your shutdown and reduce maintenance costs. And that is often worth a lot of money.