Most industrial plants around the world are trapped in the vicious cycle of reactive maintenance. These plants and their teams silently suffer from low reliability, high maintenance costs, low morale, and too much stress. Unfortunately, the journey to create a Reliable Plant has been made unnecessarily complex. In this article, I will show you how to escape the reactive maintenance environment in 4 simple steps.
The Reactive Maintenance Trap
But first, let’s set the scene. Imagine it’s a typical Tuesday afternoon when suddenly, a critical piece of equipment fails. Production grinds to a halt, stress levels soar, and you’re at the epicenter, tirelessly battling one breakdown after another. This isn’t an isolated bad day; it’s a recurring nightmare that drains profits, exhausts your team, and invades your personal life.
But why does this cycle persist across plants worldwide?
The truth is, reactive maintenance is a silent profit thief – unpredictable, costly, and stressful.
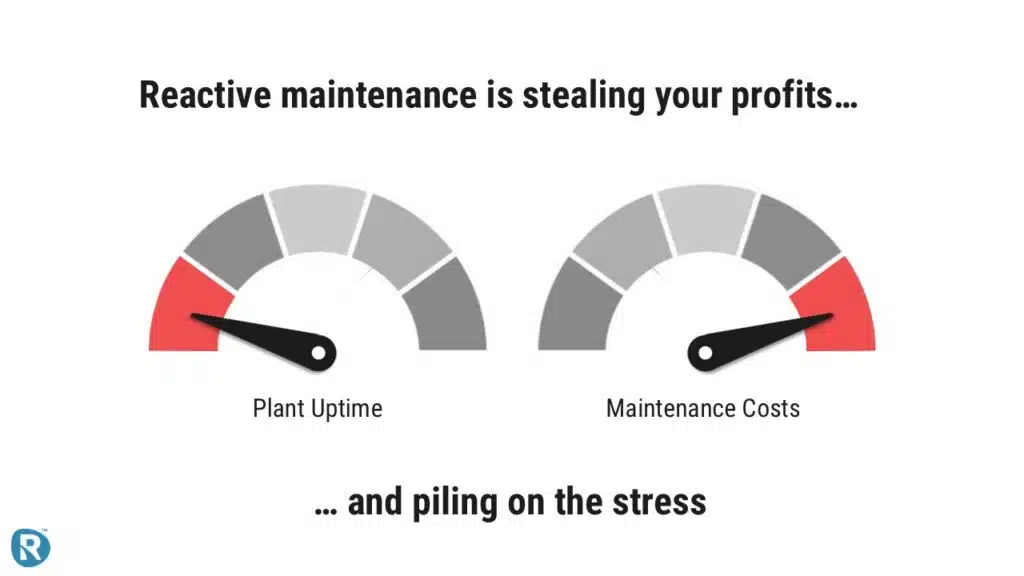
And the wort part is that it creates a negative cycle that becomes really hard to escape. But while you might feel stuck in this reactive cycle, I want you to know there IS a way out and that’s exactly what we’ll be covering in this article.
The Power of Proactive Maintenance
Now, picture a week free from firefighting, where your focus shifts from urgent repairs to proactive improvements. Envision a workplace renowned for its reliability rather than its quick fixes. This isn’t a pipe dream but a tangible reality achievable through proactive maintenance. Today, we’ll lay out a practical roadmap for building a culture of reliability, enhancing your leadership, and sparking change within your organization.
After reading this article you will not only walk away with a clear roadmap, you will
- understand that the journey to a reliable plant does not have to be complicated
- understand that there is a very logical and clear sequence to the steps we need to take
- see that you can and SHOULD do this with your own people, instead of relying on an army of external consultants!
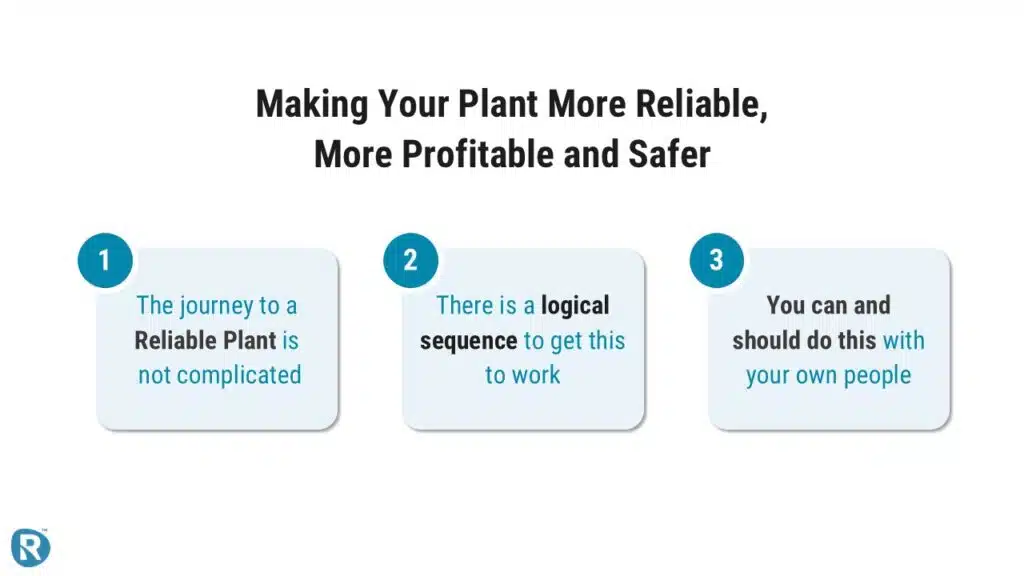
A bit of background
But before we jump in let me share a bit about myself. My name is Erik Hupje, I’m the founder of the Reliability Academy and for 23 years or so I worked for Shell and ConocoPhillips across the world. Initially in Netherlands, the United Kingdom, the Philippines, the Sultanate of Oman and since 2013 I am based in Australia. During my career I worked on old assets, new assets, billion-dollar greenfield projects, onshore and offshore, oil, gas, unconventionals and a large scale LNG plant. I’ve managed small maintenance teams with small budgets and relatively large teams with very substantial maintenance budgets (close to $100 million per year).
Everywhere I worked, I encountered the same problems: relatively low productivity, repeat failures, unoptimized PM programs and highly reactive maintenance environments. You see even though I worked for big name companies, companies with strong reputations, I found myself in some of the most reactive maintenance environments you could imagine.

Although I worked in quite a few locations around the world, I obviously did not work everywhere. Or in every industry. But since launching the Reliability Academy I have worked with clients around the world. In fact, 90% – 95% of our revenue comes from overseas clients. And when I work with our clients, I observe the same issues: organisations are reactive, the basics are often lacking, there is a strong need to get productivity improved, the PM programs are wasteful and they’re dealing with too many repeat failures.
And when you then factor in the feedback we get from individual students from all over the world It just really reinforces the message that most plants around the world, no matter where they are, no matter the industry they are in, they are struggling with a reactive maintenance environment.
And to be honest, that was the situation I found myself in, back in 2005 when I worked in the Philippines and had just been promoted to Head of Maintenance Execution. Of course, I was happy with the promotion. But, I had no time to celebrate. Every single system we had was plagued with issues. Every week we had a new ‘emergency’ that would throw everything up in the air. And we had a big backlog of overdue maintenance including a lot overdue safety-critical maintenance.
Work was never-ending. The pressure was immense. And so was the stress. I knew we needed to make some serious changes if we ever wanted to get out of this vicious cycle we were in… Now at this point in my career I had limited experience in maintenance and reliability so I turned to the market for advice, but all I ever got, were complex, expensive, often software-centric solutions. But what my team and I needed was a simple easy-to-understand solution. A practical solution that we could actually implement, not something with 10 or 20 different elements that would take us 5 or 10 years to get in place.
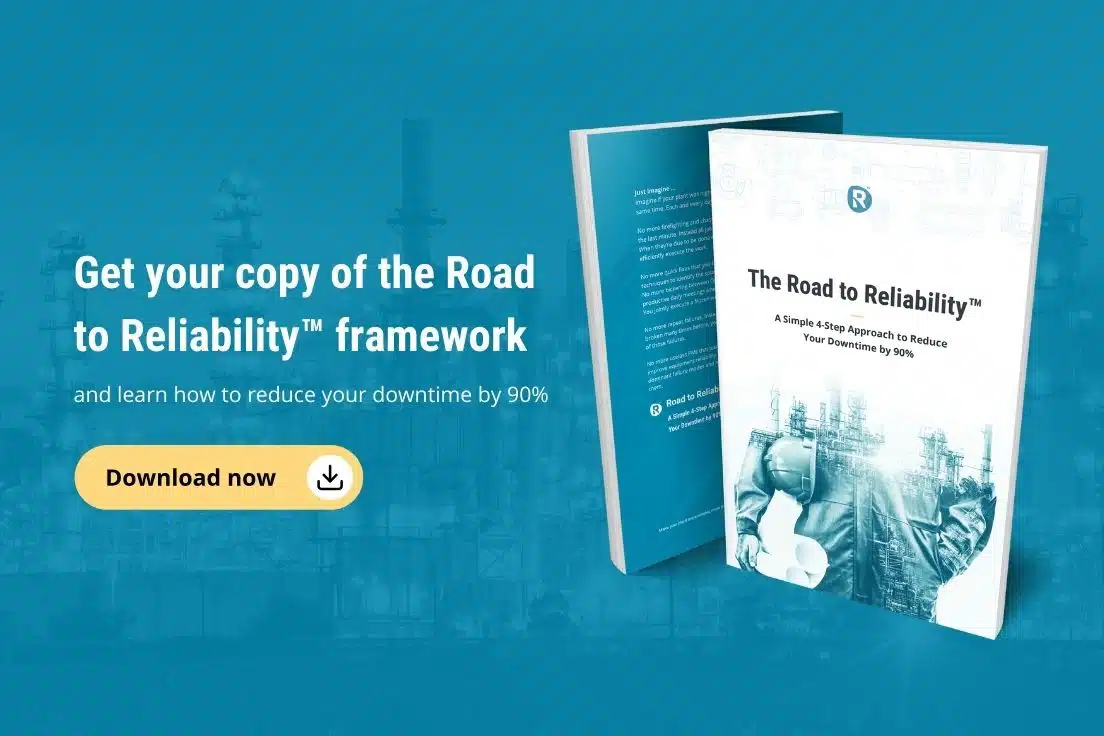
Now the situation kind of forced our hand. On an offshore platform you are limited to the number of people you can have onboard and we were maxed out on headcount but not getting enough work done. Productivity was low, way too low. So we improved our planning & scheduling process with the intent to boost our productivity. We implemented a frozen weekly schedule, we ran backlog reviews, work orders were identified, prioritized, planned, scheduled and executed.
We also noticed that we were doing a lot of PMs that weren’t adding value, so to help reduce our workload, we prioritized our critical PMs and improved them and removed the PM tasks that weren’t adding value.
And we struggled with a lot of high-impact, repeat failures, which we tackled by analysing the root causes and eliminating them where possible.
We implemented these improvements one at a time. And slowly, but surely, our efforts bore fruit. There was less waste. Our workload got lighter. We got more things done in a day.
Morale improved. Work standards improved.
My team, our management and I myself were all amazed at how effective those 3 simple improvements were. Years later, I would come across research that actually quantified the importance of these elements. More on that later.
Now, I’m sharing this story with you—because if you’re in a similar situation right now, if you’re experiencing big backlogs, low reliability, low productivity, high maintenance costs and you need to guide your team through this phase, with little to no leadership support then you are in the right place, because that is exactly what I will talk about in this article.
The rest of this article will breakdown in 3 sections:
- In the 1st part I will explain the Framework and the 4 elements you need to implement
- Then I will explain how that framework converts to a simple roadmap and the logical sequence of the steps
- In the 3rd part we’ll talk about what you need to do make the change, and how we can help you on your journey
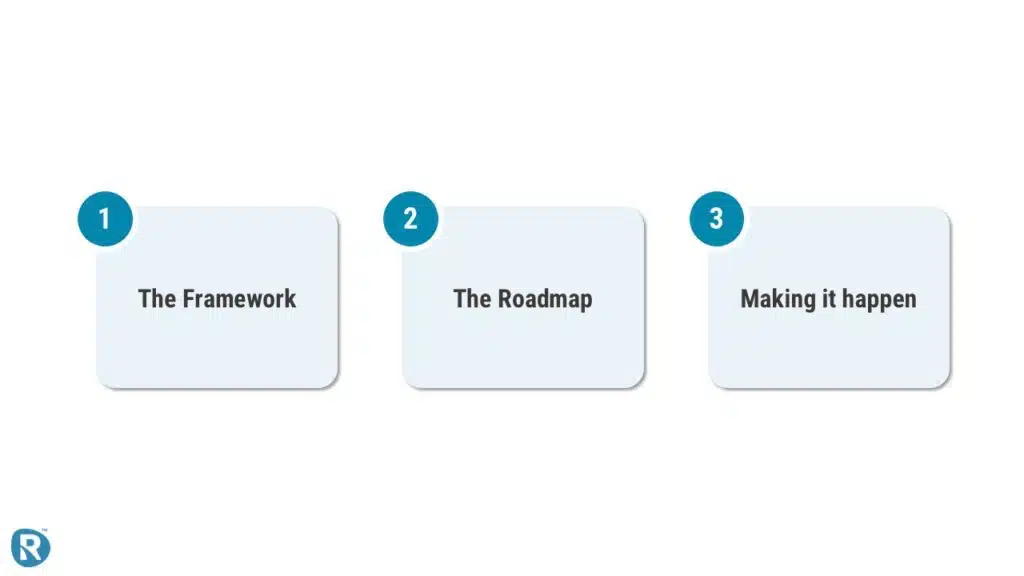
The Problem
As we discussed many organisations around the world struggle with low reliability & high maintenance costs and that leads to lost production and lower-than-possible revenue and profit. But … that is just the tip of the iceberg. That is what you can observe quite easily in these organisations.
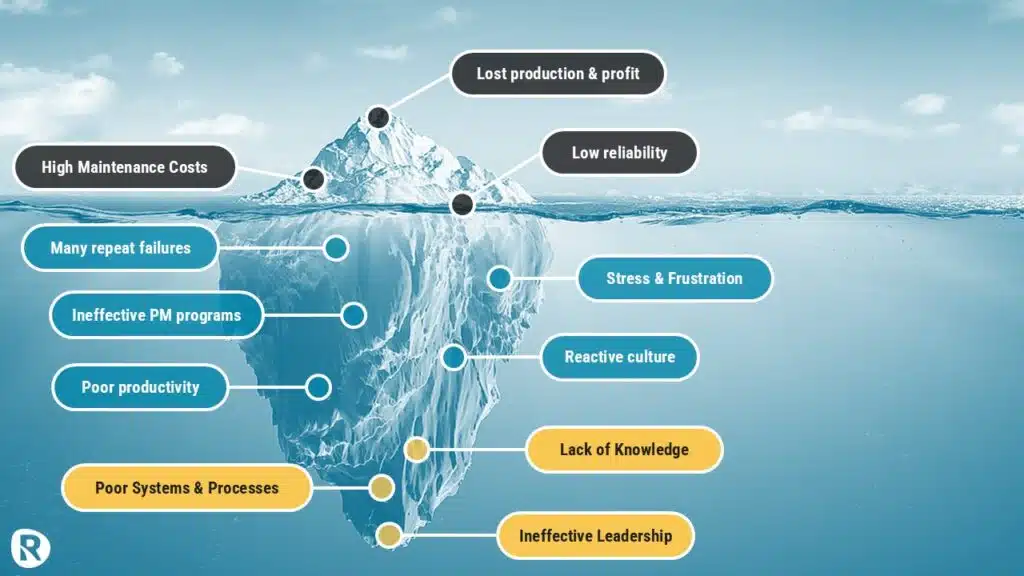
When you look deeper, you typically find a lot of repeat failures, and an organisation that tries to be really good at fixing failures, rather than preventing them. The result is a lot of fire fighting, high levels of stress, and a lot of frustration. At the same time, we typically see poor preventive maintenance programs with a lot of tasks that add little to no value, and critical tasks missing. All this leads to a reactive culture, where we’re continuously fire fighting and fixing repeat failures. And as a result, we end up with low productivity. In many organisations we’d be lucky to get 25% to 35% productive time out of a typical maintenance technician
And that low productivity only makes it harder to escape the reactive environment.
In simple terms, this happens because these organisations lack effective systems and processes. They don’t have the knowledge of how to manage maintenance effectively and how to drive reliability. Not enough attention is paid to the basic processes that really drive effective maintenance and high reliability. And in the end, this is the result of ineffective leadership.
The Perceived Solution
So how do we fix this? How do we reduce maintenance costs and improve reliability? We all know how to get to high reliability, right? It is a complicated long journey. We’ve heard it many times: “it’s a marathon, not a sprint.” It takes years and years of hard work, relying on many specialist consultants and advisors. You likely will need to invest millions of dollars and buy new software. Why do we know this? We know this – because that is what the market has told us for decades. That is what I was told when I reached out for help in the past. And we know this, because the frameworks out there in the market to achieve reliability are complicated. They consist of 20 or 30 different elements that we need to implement.
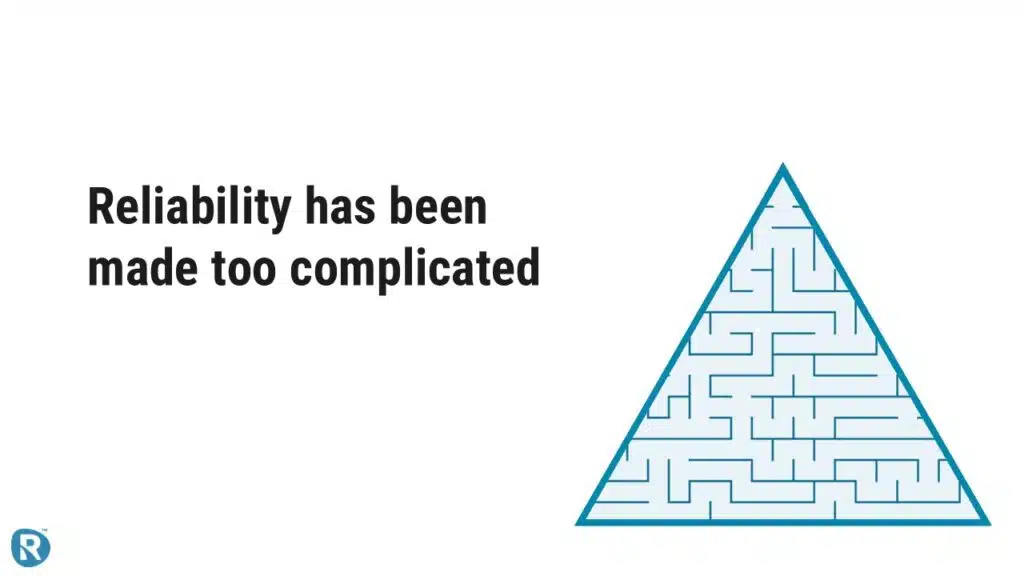
And when you are working in a reactive maintenance environment the last thing you want, the last thing you need, is an overly complicated improvement framework with 20 different steps. You need, you want a simple, practical approach, that you can start with tomorrow… and actually have a chance of implementing.
Now don’t get me wrong – a lot of the models out there are theoretically correct. They contain a lot of aspects organisations need to get right, to achieve world-class performance. But the problem is not that thousands of organisations around the globe are struggling to become world-class. The problem is that thousands of organisations around the globe are struggling to escape the vicious cycle of reactive maintenance. They are struggling to really make progress early in the journey to a reliable plant. And the easier we make those first steps the better our chances of making real, sustainable progress.
The Vicious Cycle of Reactive Maintenance
But once you really understand what is happen in all these plants around the world. And once you’ve been through the process of making plants like these much more reliable You start to see that the journey to a reliable plant is quite predictable. And when the problem is predictable, the solution becomes predictable too.
You see, what is happening in these plants that keeps them stuck in that vicious cycle of reactive maintenance is the following.
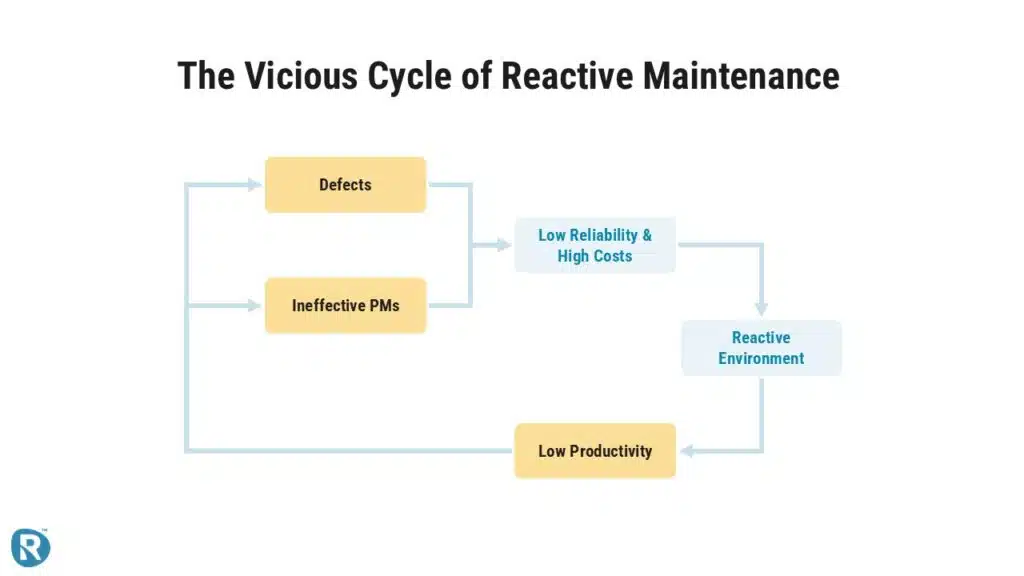
Their plant is typically plagued by two things. First, a lot of defects that cause repeat failures. And secondly ineffective PMs that waste scarce resources and do not prevent further failures. The result is a plant struggling with low reliability and high maintenance costs, because fixing failures is a lot more expensive than preventing them.
The low reliability and high maintenance costs over time lead to a reactive environment with not enough resources to do the work and chasing the latest equipment failure. Fire fighting is the norm. And fire fighting becomes glorified in the culture. Instead of preventing failure, organisations try to get really good at fixing failures.
But the reality is, that in these reactive maintenance environments productivity is low. When you are rushing from one breakdown to the next you don’t plan the work, you barely schedule the work. And as a result is that your crews continuously experience delays. And on average productivity in an environment like that is somewhere between 25% to 35%. Typically on the lower end of that range. And that low productivity means your crew is stretched to do the work that the organisation thinks needs to be done, and there simply is no time to remove those defects or improve those PMs. And that is how organisations get stuck in the vicious cycle of reactive maintenance.
And what you can see is that there are 3 key areas that need to be tackled to break that vicious cycle:
- You need to eliminate your defects
- You need to create an effective PM program
- And you need to create a productive working environment
The Road to Reliability Framework™
And that is exactly what you find in our Road to Reliability Framework™. With the core processes of Planning & Scheduling, Preventive Maintenance and Defect Elimination.
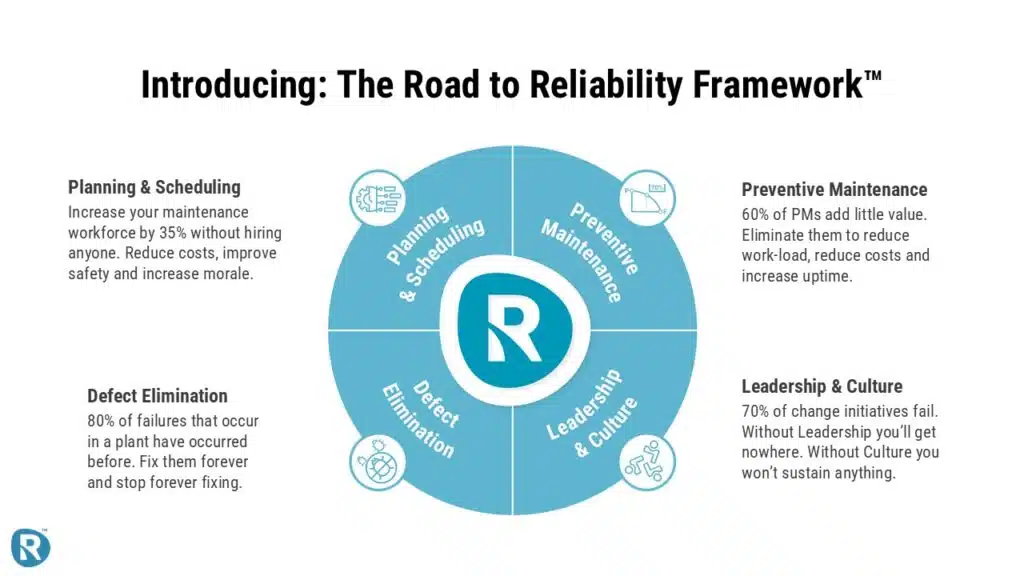
Planning & Scheduling
You need to implement an effective and efficient planning & scheduling process so that you can increase your maintenance productivity and create a stable working environment where the fire fighting is largely eliminated, where stress levels are much lower and where your team has the time and motivation to make further improvements. Now the great thing about improving planning & scheduling is that it pays for itself very quickly. In most organisations you effectively increase the size of your maintenance by 35% without hiring anyone.
Preventive Maintenance
Once you have made substantial improvement with your planning & scheduling, and have created a more stable working environment, you need to review your PM program and make sure you are doing work that adds value. Over and over again we see PM programs that are wasteful. Tasks that are done too often, tasks that really add no value. Experience shows that in a typical PM program 60% of the tasks add little value. Eliminate them to reduce work-load, reduce costs and increase uptime. And you do that by making sure your PM program is based on the basic principles of reliability and effective maintenance.
Defect Elimination
The purpose of defect elimination is simple: get rid of the many repeat failures that most plants around the world keep dealing with. Experience shows that 80% of failures that occur in a plant have occurred before. And what do we normally do in response to recurring failures? We get good at fixing them. We increase inventory. We create special procedures to deal with them. Some organisations even have dedicated reactive maintenance teams whose whole purpose in life is to chase after breakdowns. But what we want to do, what we need to do, is to eliminate the problems that cause these repeat failures. We need to fix them forever, and stop forever fixing.
Leadership & Culture
You need Leadership to drive change. Without leadership you will get nowhere. But without culture you won’t sustain the change you have created. And unfortunately, this is what a lot of organisations get wrong.
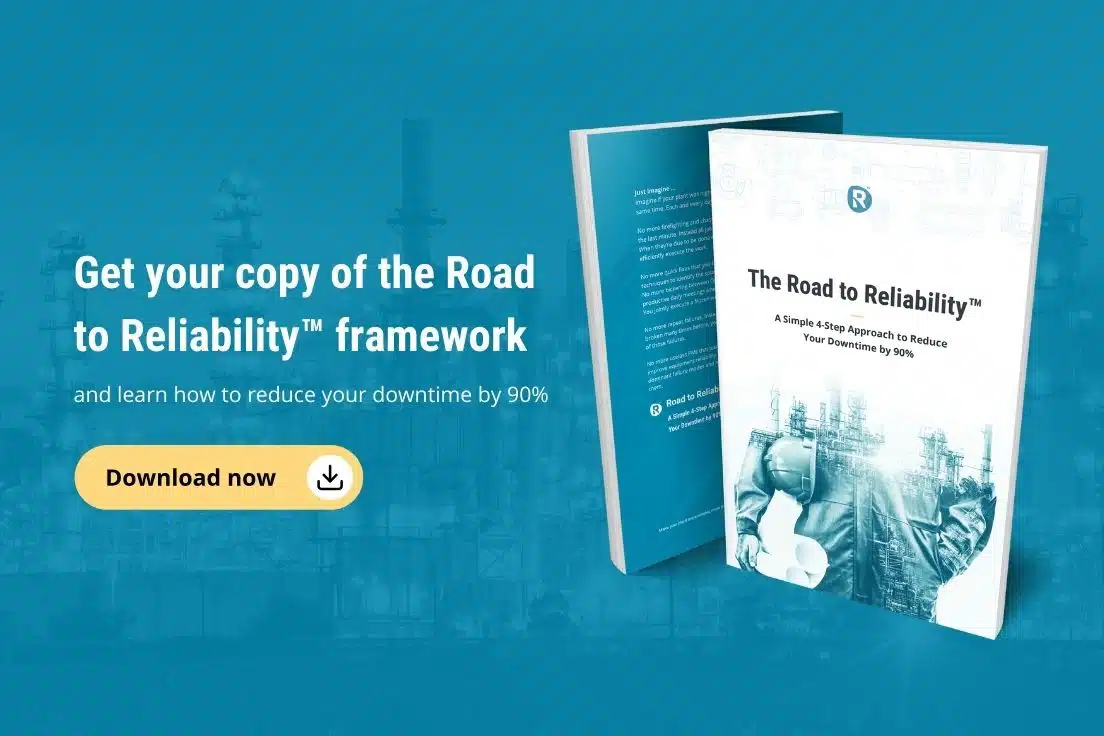
The Value
Now you might be wondering: so what is all this worth? What would I gain if I implemented those 3 practices? Well, there is actually research that can answer that question. So not our personal industry experience, not our client success stories, but real, objective research.
This research was done in the 1990’s by Dupont across 3500 manufacturing sites around the world including the US, Europe and Japan. No unfortunately the full details of that research is not in the public domain, but over the years Winston Ledet and others have shared enough of it to be able to tell an important story.
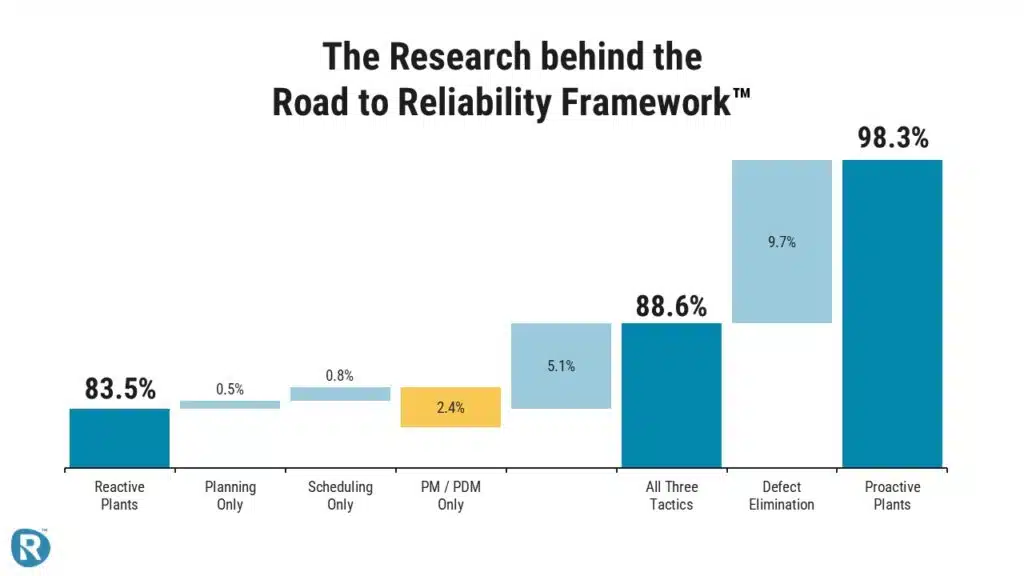
You see, that research found that reactive plants typically achieved an uptime of around 83.5%. That same research found that the best performing manufacturing sites achieved uptimes in excess of 98% by focusing on planning & scheduling, preventive and predictive maintenance and defect elimination.
So, lets have a look at what that study showed in a bit more detail. Starting with a reactive plant on the left with an uptime of around 83%.
- When industrial plants with a reactive maintenance culture implemented only Planning their uptime improved on average by +0.5%
- When they implemented only Scheduling their uptime improved on average by +0.8%
- When they implemented Preventive Maintenance only, their uptime decreased on average by 2.4% due to the additional downtime to conduct preventive maintenance work.
- But industrial plants with a reactive maintenance culture that implemented all three tactics of Planning, Scheduling and Preventive Maintenance increased their uptime on average by 5.1%. Not bad, in most industries that is worth a lot, potentiall millions of dolars per year.
- But when these plants added Defect Elimination to their suite of practices, their total increase in uptime went up by almost 15%! Meaning they increased from a low 83% to a world-class level of over 98%. And these plants experienced almost 90% less downtime compared to reactive plants.
Imagine what that would do to your business.
The Danger of Marathon Thinking
I mentioned earlier that common belief that this journey is a marathon. A journey that takes time, a huge amount of effort over a long period of time, and substantial investment. In itself that is not wrong, but when we accept this view that improving reliability is a marathon that creates two big problems.
The first problem is that most of us can’t run a marathon.

You could train for it, and with a lot of hard work, you would succeed. Now try getting your whole team to run a marathon. Very unlikely that you will succeed. The result is that a lot of improvement programs that have been approached as long-term marathons lose steam along the way and fail. The result is that a lot people and a lot of organisations start to belief that improving reliability is just too hard, too complicated, and not something they can do themselves without a lot of external help.
The 2nd problem that this view creates, is that it very often leads to a lack of leadership support.
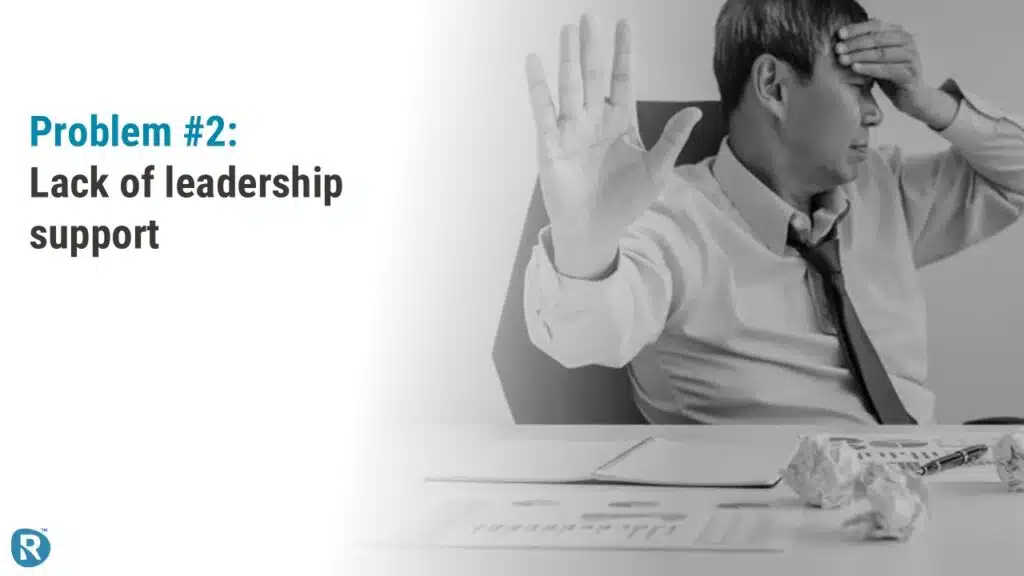
You see, when you are stuck in a reactive maintenance environment, where maintenance costs are high, reliability is too low and equipment failures are often impacting production, it can be very hard for leaders to support a substantial investment in improving maintenance & reliability performance.
A lot of senior leaders don’t have a strong understanding of the field of maintenance & reliability. And they are typically judged on achieving relatively short-term, quarterly goals.
So when you come with a multi-year improvement plan that is based on the classic Reliability Marathon approach, you are essentially promising a payback some time far in the future with significant upfront costs right now. You’re just not going to get that YES that you want. That you think you NEED – especially when you are stuck in that reactive environment, when maintenance & reliability are seen as troublesome, as issues and not as profit centers that justify more investment.
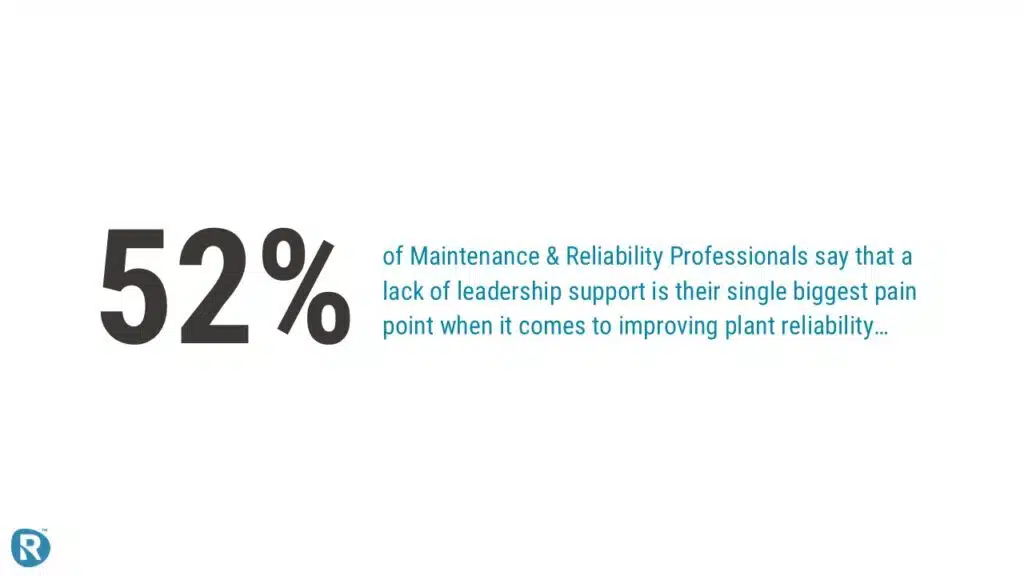
In a recent poll I ran on LinkedIn, 52% of respondents said that a lack of leadership support was their single biggest pain point when it comes to improving reliability. What I am saying here is that we’re making it too hard for ourselves to get leadership support by trying to get them to run a marathon with us. Leadership is simply not interested at this point to run the marathon. They don’t see the long-term benefits outweighing the short term pains. Or worse, they don’t buy the story.
But it doesn’t stop there. It gets worse.
‘Shortcuts’ don’t work
You see, just as a marathon runner, these organisations hit a brick wall and can’t get through. Their maintenance costs remain high, productivity low, reliability not where it should be.
The result is that people start to look for shortcuts, Ways to go around that brick wall. They look for silver bullets that make the journey easy. That’s when people think that investing in new or more advanced software will solve their problems. Or that doing RCM on their whole plant will solve their reliability problem. Unfortunately, neither is true. Silver bullets don’t exist. And the journey to reliability is not easy.
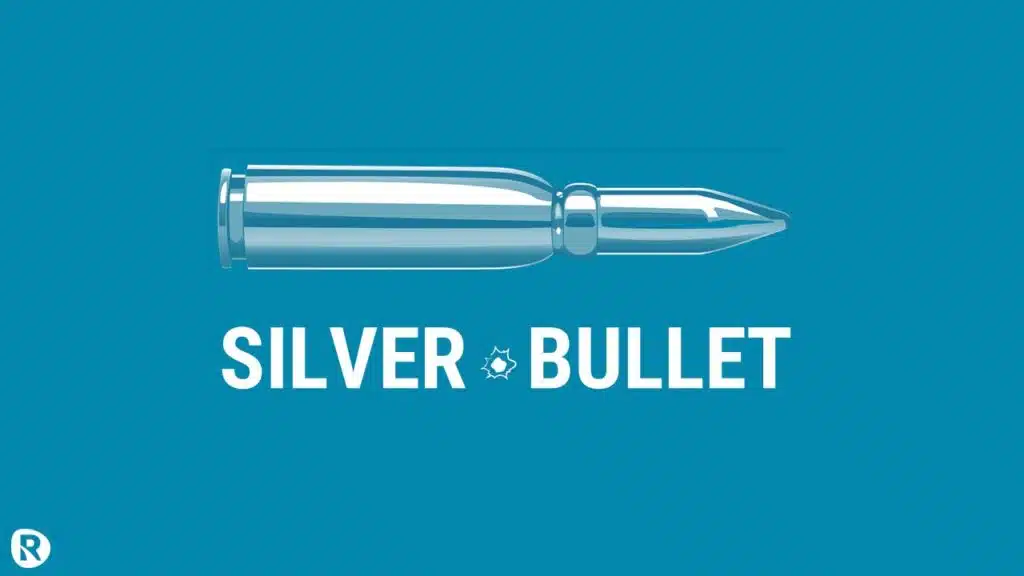
But it does not have to be as complicated as we make it out to be. I’ve already shown you a simple framework that shows you how to escape the vicious cycle or reactive maintenance and create a reliable plant. So that you don’t need to rely on silver bullets that don’t exist.
Now what I will do next is convert that framework into a simple roadmap. And convert that marathon journey into a series of shorter sprints. These shorter sprints are easier to understand, easier to manage, easier to sell in your organisation and give you a much better chance of making an improvement that will be sustained over time.
Reliability Sprints
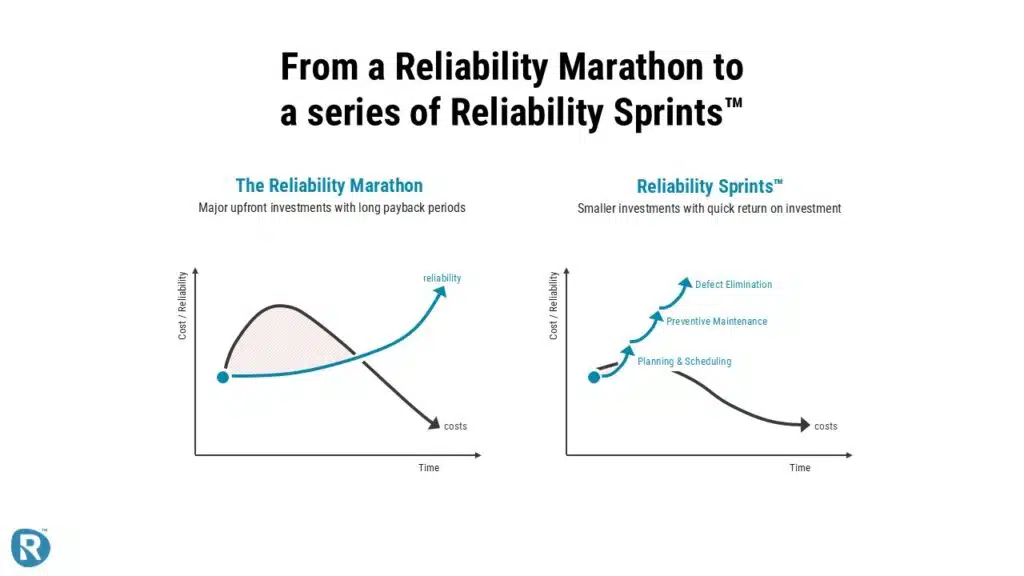
I call them “Reliability Sprints”. Just like the IT industry has moved away from massive, complex, time-consuming projects to implement software and nowadays uses a more agile approach based on a series of sprints. We are encouraging our clients to move away from large, complex, and multi-year reliability improvement projects. And instead, tackle reliability improvement through a series of shorter, focussed sprints. These sprints are less complex to manage, easier to understand, cost less and are typically something you can implement with your own team without having to hire an army of external consultants.
And by adopting a sprint methodology we’re moving away from the classic Reliability Marathon approach to a series of Reliability Sprints. With the Reliability Sprints methodology we aim for smaller improvements, which are delivered much quicker. We focus on just a few items that really deliver value and we eliminate certain elements and practices, that are historically included in these large reliability marathons but that actually have a very low or slow payback. And because we’re aiming for smaller improvements, with less upfront investment the resistance to change and the need for major leadership support also reduces. Which makes it easier for us to make this journey.
A word on Reliability Culture
Now before I share a roadmap that is based around Reliability Sprints I need to talk a bit more about the 4th element: Leadership & Culture. You see 3 of the elements in our framework are actual work processes, processes that our teams will execute on a continuous basis. Those processes were planning & scheduling, preventive maintenance and defect elimination. But the 4th element of our framework is leadership and culture. And this is not a process.
When it comes to leadership I think most of us will have a clear view on what that is. There are many definitions out there, but I like this simple one from mindtools.com which states that “in its simplest form, leadership is influencing other people to follow.” And so when it comes to our reliability journey we need to motivate others to follow us on that journey.
But in our journey to creating a reliable plant, we do not just need leadership, we also need to create a culture focussed on reliability. You see you need leadership to drive change. And you need culture to sustain it.
Imagine that you and your team are pushing a big heavy rock up a sloping hill.
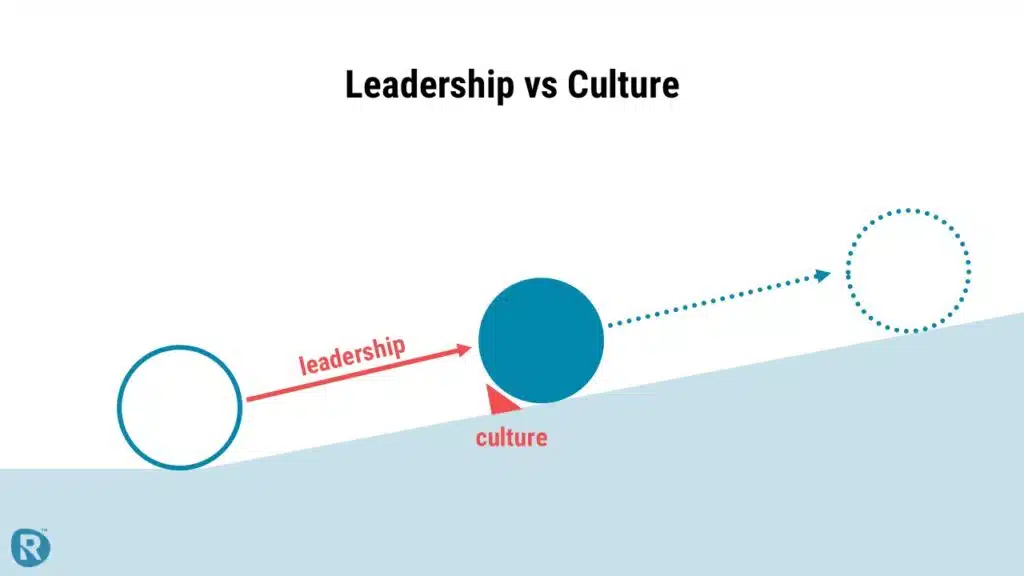
To be honest that is what the journey to creating a reliable plant can sometimes feel like.
You need leadership to motivate your team to push that rock up the hill. But this is a long hill. It is a never ending hill. So if you don’t find a way to stop that rock from rolling down the hill when you’re not pushing you will never make much progress. And this is often what happens in organisations. They push hard to make some progress, but that progress erodes over time because they didn’t create a culture to sustain that improvement. You see that is exactly what culture is and does it sustains your progress, your ways of working, your values, your beliefs and embeds them in your team, in your organisation. So that when you are busy with something else for a minute that big heavy rock is not going to roll down the hill. Now that is a nice way to explain the difference between leadership and culture.
But what is culture?
And what does culture mean when it comes to reliability? Now there are many academic sources and books on organisational culture. And even a few books on reliability culture. Unfortunately, the concepts and models proposed in those sources are not simple, not very practical. So, a while back I developed a simple model that defines what reliability culture is using just 4 elements.
This model is based on the book “Improving Maintenance & Reliability Through Culture Change” by Stephen J Thomas, who built his model on some of the academic research on corporate culture, specifically the culture model developed by Terrence Deal and Allan Kennedy in the 1980’s.
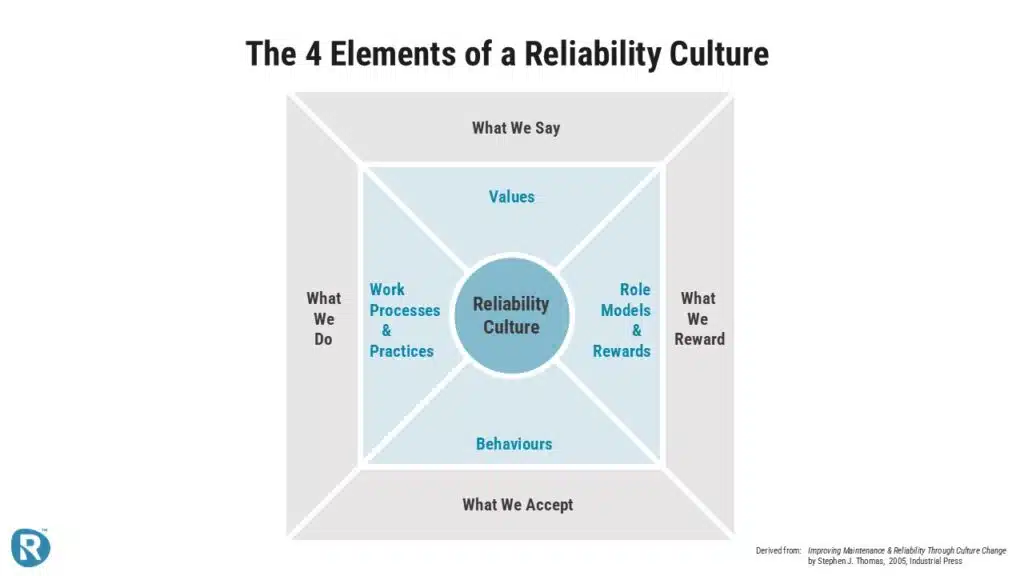
What you see here is a similar model, but simplified and one major addition: Work Process & Practices. You see most of the work on culture is on organisational culture, corporate culture. When it comes to reliability culture, I strongly believe your work processes and practices are key. Work processes formalise how work is done, and as such strongly influence reliability culture. Poorly defined, loose, inconsistent, or simply missing work processes will drive you to a much more reactive reliability culture. On the other hand, well-defined, well-executed processes can reinforce a proactive culture even to new members of the organisation.
Now I don’t really have the time to go into this model in more depth, But I do want to share this view which really simplifies culture to 4 practical elements:
- What we say
- What we do
- What we reward
- And what we accept
And if you get those things right, and get a focus of reliability built around these 4 things you will be on the right track.
Developing a Roadmap
So let’s look at how we convert this framework of 4 elements into a simple, and practical roadmap that you can follow. We need to get to a state where we have our 3 core work processes of planning & scheduling, Preventive Maintenance and Defect Elimination implemented in our organisation and supported by a culture that is focussed on reliability.
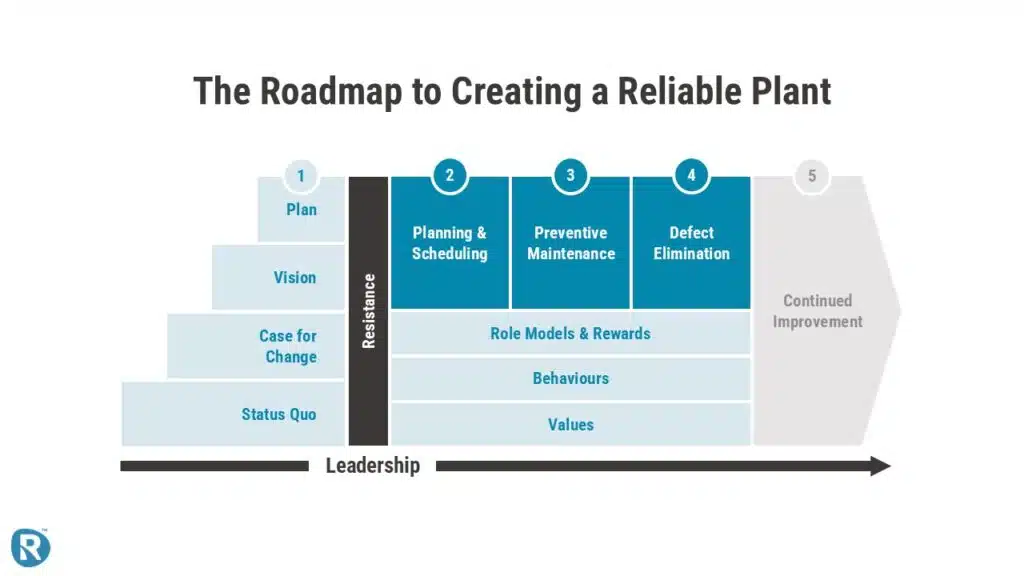
And as we discussed, that moving forward, that push for change requires leadership, Which is shown by the long black arrow. But by breaking your journey into smaller steps you reduce the amount of resistance you face.
Now, there is a very logical sequence on which processes need to be implemented first.
Step 1: Get your Reliability Strategy Defined
For most organisations where they are today Is a very different place. A place that is characterised by a lot of reactive maintenance, a lot of firefighting. So when you look at that desired future state you’re likely going to face a lot of resistance, A lot of push back from a variety of people in your organisation. Whether that is leadership, operations of your own maintenance team. Plus you may not yet have a clear picture of what good would look like for your plant.
And to overcome that resistance, you need to have a Reliability Strategy that consists of 4 key things.
- First of all you need to understand the status quo: where you are today, how is your performance, what are the big issues.
- You then need to build a clear case for change that you use to engage your organisation nd share with them why staying where you are today is not good enough.
- With that case for change you need to have a clear vision of what the future will look like for your plant and for the different groups in your organisation. You need to show them how improving reliability is going to make their work life better. You need to show them what’s in it for them to follow you on that journey to a more reliable plant.
- And then finally you need to take those three elements and develop a simple, but clear plan on how to move forward.
Combine those 4 things and you have the core elements of a simple, but highly effective Reliability Strategy that will show your organisation how to move from the current reactive environment to a much more proactive place.
Step 2: Implement or Improve Planning & Scheduling
Step 2 is to start with implementing or improving your maintenance planning & scheduling process so you can better levels of productivity and get more work done with your existing crew. With better planning & scheduling you create a more stable working environment with less fire fighting which then gives you the time and headspace to focus on the next step.
As I said earlier, the great thing about improving planning & scheduling is that it pays for itself very quickly. In most organisations you can effectively increase the size of your maintenance crew by 35% without hiring anyone. Depending on the complexity of your organisation, you can make a massive improvement in your productivity in 6 to 12 months.
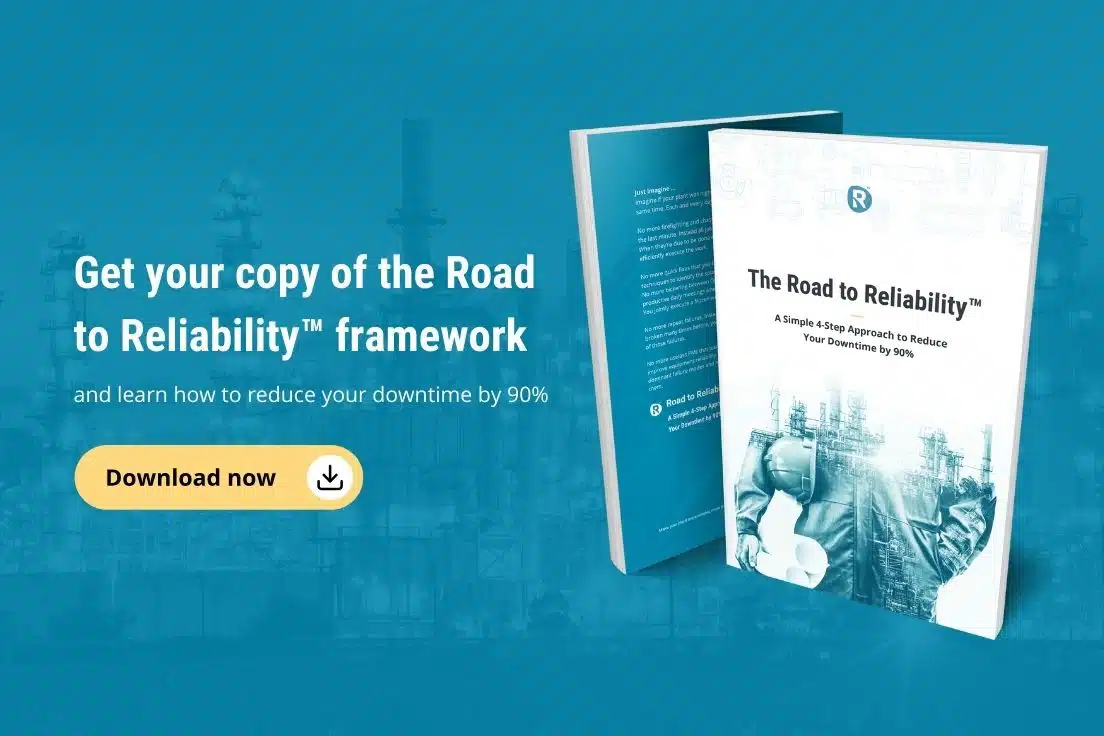
Step 3: Optimise your PM Program
Step 3 is to tackle your PM program. Most PM programs contain a lot of activities that don’t add value. So we need to get rid of those and ensure we deploy our scarce resource wisely. And at the same time many PM programs are missing tasks that should be included. So we need to add those. In the end improving your PM program is all about building capability in your team. Getting them to understand the principles of reliability, and what makes for an effective and efficient PM Program.
Now there is an important reason why we focus on improving our PM Program AFTER we have fixed our planning & scheduling process and AFTER we have created a more stable, more productive working environment.
You see an effective and efficient PM program will contain a lot of condition-based maintenance, because the majority of failure modes we deal with are actually not age-related, and therefore best managed with some type of condition assessment. But condition-based maintenance when done right tells us weeks if not months in advance that we have an impending problem. That that bearing on that pump is going to fail in 4 months. Guess what’s done with that information in a reactive firefighting environment? Exactly! Nothing!
In reactive, fire fighting environments the weak signals that come from CBM programs are routinely ignored. And we’ve all seen it. The pump fails, the manager says, why didn’t we see that coming? Our CBM program should have picked that up? And then your reliability engineer tells you “well we did see it coming, the work request was raised 4 months ago”… but it was ignored. Sound familiar?
So that is why we focus on our PM program after we have improved our working environment through better planning & scheduling. If we do it the other way round, well then – as the famous saying goes – we’re putting the cart before the horse.
Step 4: Implement Defect Elimination
And then the 3rd work process we need to get working is defect elimination and root cause analysis so we eliminate the repeat failures and prevent small issues from becoming bigger issues. Reactive organisations are usually not good at implementing and sustaining defect elimination and root cause analysis. For this process to work you need to build a culture that focusses on learning. A culture that focuses on fact-based problem solving. A culture where you are not routinely blaming people when things go wrong, but a culture where you focus on systemic issues. Establishing a culture like this takes time, but becomes much easier when you have made some progress on your journey to a Reliable Plant.
As we implement our core work processes, we progressively build and implement the right elements of our reliability culture. We are clear on our values and what is important. We set clear expectations around the work we need to do, how we do the work and we reward the right behaviours. Step by step we build, implement and refine a culture of reliability.
Step 5: Continuous Improvement
And once we have those 3 core work processes implemented, working effectively, and efficiently and being supported by the right values, the right behaviours and we have the right role models and rewards in place that’s when we start looking at a range of more advanced practices and tools. Because in the end, continuous improvement is the name of the game.
And that is the roadmap to creating a reliable plant. Now if you have been on our website you will have seen a simpler version of this roadmap where we combine all four elements of creating a Reliability Strategy into a what I call a “Reliability Strategy Sprint” and we simply show the leadership and culture elements as one block where the focus shifts from leadership to culture as you progress through the implementation. And so the Roadmap to Creating a Reliable Plant comes down to implementing 4 elements. To conducting 4 Reliability Sprints.
How do we get this done?
Now, at this point you might be thinking:
OK, great framework, it’s simple, it’s logical. It’s founded in research. I like it. But HOW the heck am I going to get this done? Do I need an army of consultants? That will never fly…
The good thing is – NO, you don’t need an army of consultants to get this done. In fact, based on my own 20+ years of experience in industry and now working with clients for several years via the Reliability Academy I very strongly believe that the BEST way to implement your reliability strategy is with your own team. You Can and you SHOULD implement your Reliability strategy with your own team.
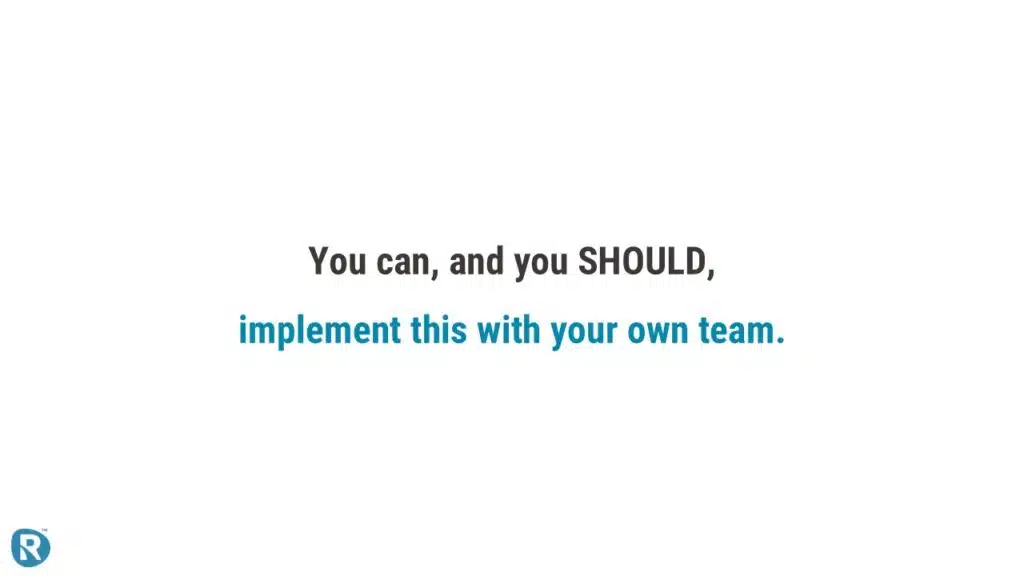
I have seen again and again how processes that were implemented by consultants fall apart over time as there wasn’t enough buy-in in the organisation. 3, 6, 12 months after the consultants leave, you start hearing people say “I never really agreed with that anyway.” And before you know it, a lot of the good work that was done is eroded. But… When your team implements these improvements themselves, there is ownership, there is buy-in, and the improvements last over time. Now, to be clear, this approach does initially take longer than bringing in an army of consultants. But in the end it gives a much more sustainable result. And it costs a lot less to implement too.
At the Reliability Academy we train your team in the core processes of Planning & Scheduling, Preventive Maintenance, and Defect Elimination. And in our training we not only provide the knowledge to really understand those processes, but we also teach members of your team on how to successfully implement those processes in your organisation. And that is pretty unique in the market.
To make it more visible how we work together with our customers we’ve created this chart:
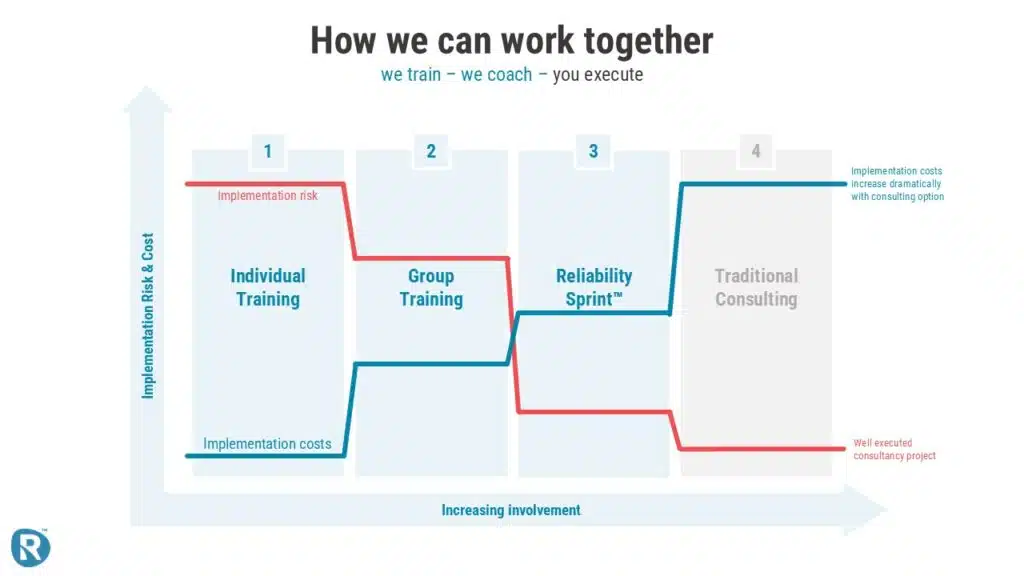
What you see here are the different ways we can support you and your team. Ranging from individual training, to group training to helping you execute a Reliability Sprint. As you can see the final engagement model on this chart, the traditional consulting, is greyed out as that is not something we do. The lines on this chart show two key factors: the blue line shows you the cost of implementation and the red line show the risk associated with the implementation.
- So the first option is where you would have 1 or 2 individuals in your team go through our training and they would then drive the implementation for you. That approach can work if you have the right people. It’s low cost, but it is a hard model to make work and carries the most implementation risk.
- The next approach would be to train your whole team through a group training program. The costs go up, but you also see a big decrease in the implementation risk. Once everybody has been trained, and understands what should be done, how and why, implementing the required process just becomes so much easier.
- And the final model we offer are our Reliability Sprints. This is where we add an ongoing coaching element to a group training program. What we found over time is that not all clients have the discipline to stick to the implementation processes we teach. And so to help guide them through the implementation, and increase their chances of success we offer a solution where we will assign an implementation coach for 6 or 12 months to help your team successfully implement the process. This will significantly reduce the implementation risk and in terms of costs it is not that much more compared to group training. But because of the increased level of involvement this is something we can only offer to a few clients per year.
Now one last thing I just want to mention is that we don’t do the traditional consulting route, but if you do decide that is the best solution for you make sure that you obviously have the budget to support this as it’s an expensive approach and it always takes longer than you think, but most importantly make sure you engage consultants who have a proven track record in making change stick. Who are good at engaging your team and will ensure you really get lasting benefit from this approach. And that you don’t end up with a done-to-me syndrome.
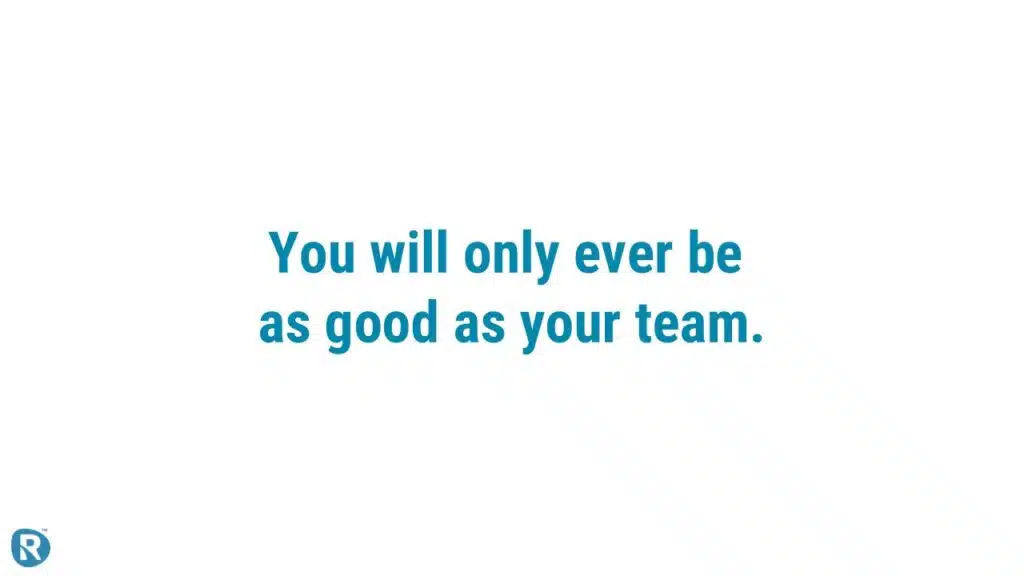
There are many ways to approach improving reliability in your plant. I strongly believe that taking an approach that makes reliability simple will really increase your chances of success. But I also strongly believe the saying that “You will only ever be as good as your team.” Which means you need to invest in your team. Train them, coach them, guide them.
And I know that training your team can sometime seem as a big investment with an uncertain return. But if you do it well, pick the right training, that is practical and can be easily applied you will create a big return on investment with lasting change and ultimately a Reliable Plant.
As Henry Ford said: “The only thing worse than training your employees and having them leave, is not training them and having them stay.”
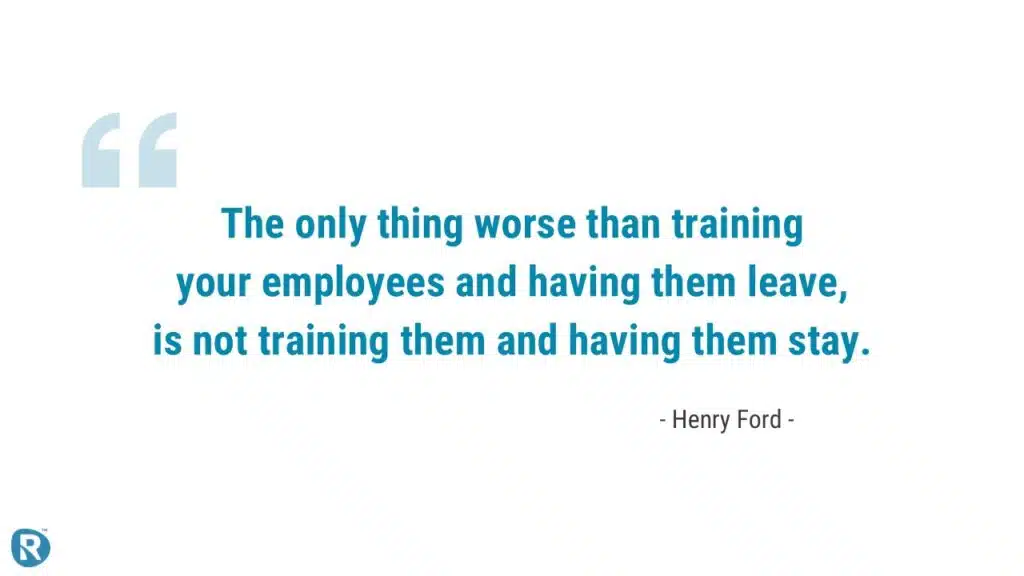
But if employee turn-over is a big issue for your organisation, we now offer you a 24-month turnover guarantee. If someone we have trained leaves your company within 24 months of starting our training we will train their replacement free of charge.
And if you’re concerned about whether online training will work for you and your team, we offer a 30-day no questions asked satisfaction guarantee. So if you are not happy with the training your team is receiving for whatever reason simply let me know within 30-days of starting and we won’t charge you. Easy.
So if what I have shared with today in terms of our framework, the roadmap, and how we work with our clients, sounds of interest and you’d like to see if this would be a good fit for you and your team then simply book a call and we can discuss your situation in more detail. It’s really easy, just head over to www.reliabilityacademy.com/call and pick a day and time that suits you and the tool will schedule a Microsoft Teams Meeting.
My calls are not high-pressure sales calls. It will be a simple conversation where you explain where you are, what problems you’re facing and I’ll share my thoughts and advice on how to tackle those problems. And if we come to the conclusion that what we offer at the Reliability Academy might be a good fit then great we can discuss that in more detail. But if not, that’s not a problem. At least you will have gained some valuable advice and for us – well to be honest I just enjoy having these conversations.