Transport (since 1968)
2,000+ employees
Amsterdam, The Netherlands
TIP Trailer Services (TIP) is a leading provider of industrial equipment and services within Europe and North America, with a fleet of more than 110,000 vehicles and 140 maintenance and repair workshops across 17 countries.
TIP are experts in providing all services a customer will require during the life cycle of a trailer, tanker or other type of equipment. In addition, TIP has over 30,000 vehicles under maintenance contract from customers.
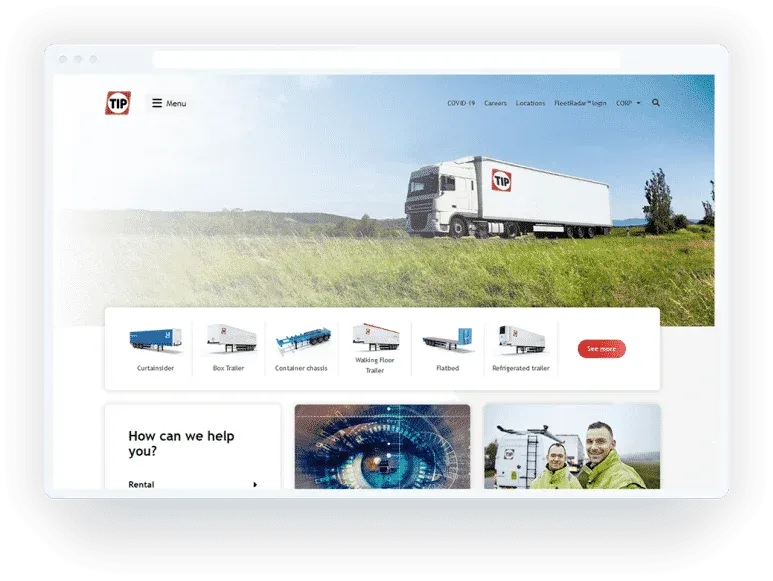
There are many frameworks for reliability improvement. Most are unnecessarily complicated.
The best performing plants in the world are the best, because they focus on the few basics that really matter.
We created a simple, yet proven framework to improve reliability focussing on just 4 Essential Elements:
Increase your maintenance workforce by 35% without hiring anyone. Reduce costs, improve safety and increase morale.
Learn more aboutPlanning & Scheduling
40% - 60% of PMs add little value. Learn how to eliminate them to reduce workload, reduce costs and increase uptime.
Learn more aboutPreventive Maintenance
80% of failures that occur in a plant have occurred before. Fix them forever and stop forever fixing.
Learn more aboutDefect Elimination
70% of change initiatives fail. Without Leadership, you'll get nowhere. Without Culture, you won't sustain anything.
Learn more aboutLeadership & Culture
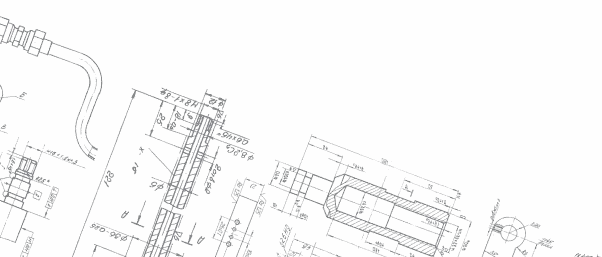
With a goal to improve efficiency and reduce maintenance costs, Didier Felice, Vice President Mediterranean Region, explored Maintenance training solutions to implement across the TIP European workshop network.
“Although we specialise in leasing and rental, maintenance has always been at the heart of our activity”, said Didier. “The better our equipment is maintained, the longer it can be leased; the better the quality of our repairs, the more customers trust us to maintain their equipment.”
An internal audit conducted in 2019 revealed significant gaps in the TIP maintenance processes. Maintenance teams had delivered suboptimal wrench time and the work environment was highly reactive, not prepared, planned, or scheduled. Too many jobs were deemed urgent, and processes were wasteful, resulting in inefficient utilisation of many of the mechanics and technicians.
This outdated way of managing workshop maintenance had to be urgently revised and improved, leading Didier to source simple and scalable Maintenance and Reliability training for the TIP teams.
-Didier Felice, Vice President Mediterranean Region
The solution
The Maintenance Scheduling and Planning course from Road to Reliability stood out from other courses due to its value, not only in teaching the basics of the discipline, but also for the assistance and support provided to ensure successful implementation.
Approximately 100 employees in France, Italy, and Spain, from all levels of the organisation ranging from Branch Directors to Workshop Managers, Sales, Senior Management and all Maintenance Team members completed the course.
Having a large cross-section of participants was key to generating a shared understanding of the requirements for world-class maintenance services and helped demonstrate how each member of the team had a critical role to play in the maintenance environment.
New rules were introduced, and tasks and responsibilities were thoroughly defined and clarified, for example, the roles of Scheduler, Planner, and Supervisor within TIP’s maintenance environment.
The many tools and templates within the course provided great value and allowed much faster implementation.
Since implementation, TIP Maintenance organisation and processes have been transformed and new roles and tools implemented. Immediately, participants were aware of the emergence of a reliability culture that moved to permit better planning and scheduling and drive continuous improvement.
With this new mindset, a pattern of sustained positive indicators emerged, including almost 100% schedule loading, 20 points improvement in scheduling compliance and optimal use of resources as well as a more stable, more positive and less stressful working environment.
Results
Regions undertaking the Road to Reliability training experienced an overall productivity improvement of 15% since the beginning of 2020, compared to an improvement of only 6% to 9% in non-participating regions.
Direct Productivity has increased by 16%
Total Productivity (Direct + Indirect) has increased by 7%
Indirect Hours have decreased from 10% to 5%
Sickness Ratio has reduced by 33% despite COVID-19
Faster turnaround times due to reduced backlog and less urgent work
Better team alignment through shared understanding and unified vision
Easier on-boarding of new employees
The regional implementation of Maintenance Planning and Scheduling Training has set TIP up for success, with potential to roll out the benefits across the whole organisation Europe-wide. Quality standards and KPIs help to maintain and build upon this improved status as more of the company becomes involved. Course updates and ongoing support from Road to Reliability continue to promote improvement.
Reduced equipment downtime, increased safety and reliability and lower maintenance costs have resulted in improved Total Cost of Ownership (TCO) for customers who are now educated by TIP on their role in helping to prioritise maintenance work and deliver equipment on time for repair. Road to Reliability’s Planning and Scheduling has given TIP the perfect toolbox to be a world-class service organisation.
Going forward, their next focus will be on efficient and effective Preventive
Maintenance, using Road to Reliability™’s next online course, in order to continue improving the availability of TIP’s assets and further reduce their TCO.
Change your strategy from reactive crisis management to efficient, productive operation with a Maintenance Planning and Scheduling Course from Road to Reliability™.