increase in availability
0
%
increase in productivity
0
%
decrease in operating costs
0
%
When you increase your plant’s reliability,
you increase your production. Increase your production and you increase your company profit.
That increase in company profit is often even bigger than just the production gain, because Reliable Plants operate at lowe costs. And experience shows that reliable plants are safer too. Higher reliability leads to less safety incidents. That’s why I like to say that when it comes to reliability improvement you can have your cake and eat it.
But the best news? Improving plant reliability requires relatively small investment. And if done well reliability improvements offer huge returns on investment.
In short, improving your plant’s reliability is one of the best investments you can make.
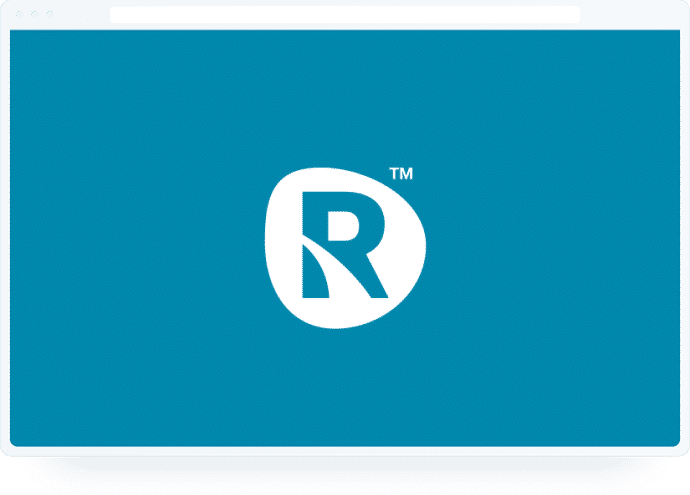