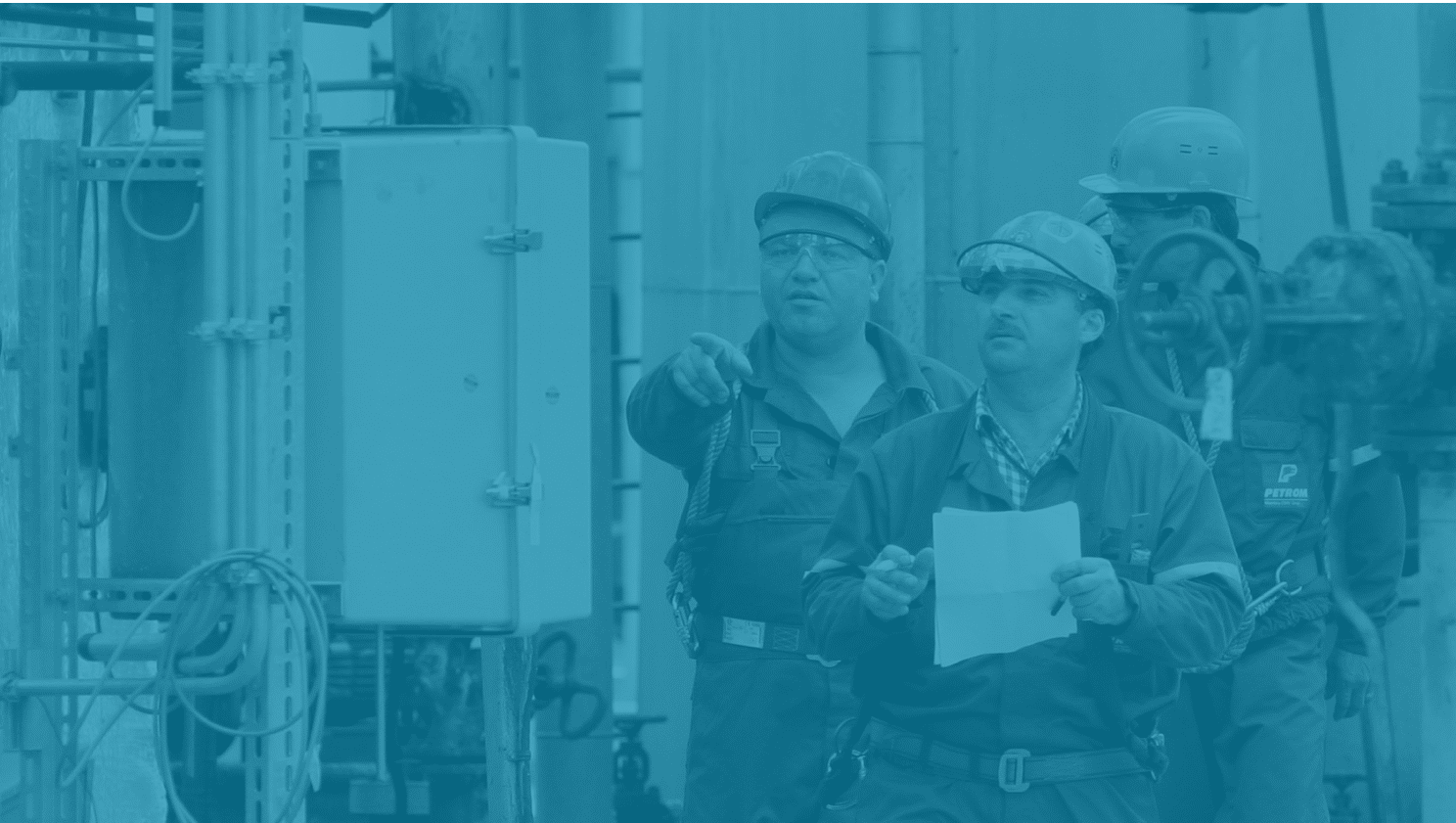
Why Most Maintenance Planning & Scheduling Efforts Fail
Maintenance Planning & Scheduling (MPS) is one of the key elements of a reliable plant. When done right, it increases your workforce productivity by at
Getting planning & scheduling in place – and working well – is a critical step in fighting your reactive work environment. It increases your maintenance productivity. And gets you ready for your next step on your journey to higher plant reliability.
The typical industry productivity or wrench time is somewhere around 30%. With proper maintenance planning and scheduling, you can drive this up to 45%. The ‘Best of the Best’ achieve productivity levels up to 60%, but don’t aim for that just yet.
Problems with maintenance productivity?
Do you know your wrench time or how to improve it? Do you have any idea how much improving your maintenance productivity could be worth to you organization? Want to know how to implement planning & scheduling successfully?
This Scorecard is designed to help Plant Managers and Maintenance Managers assess their Planning & Scheduling performance across 6 key areas and provides you with clear, actionable advice to improve maintenance productivity:
This is a quick and practical alternative to our full-blown Planning & Scheduling Assessment Tool which consists of over 140+ questions over 10 elements.
In the 1980s DuPont commissioned the largest benchmarking study of maintenance and reliability practice over done. It covered 3,500 sites across North America, Europe and Japan. It was so extensive that it’s still referred to today.
The study showed that the top 5% of these companies – the “Best of the Best” – do the basics very well. And those basics included Planning and Scheduling.
The DuPont study – and many studies since then – have shown that maintenance productivity levels of 20% – 30% are typical across industries.
That means you get 2-3 hours actual maintenance time out of a technician working a 10-hour shift. But, it doesn’t have to be like that. You don’t have to settle for low levels of maintenance productivity. Implementing an effective planning and scheduling process allows you to improve your productivity to 45%.
Improving your productivity from 30% to 45%, is the equivalent of increasing your workforce by 35% without hiring anyone.
It’s been done around the world. Over and over again. It’s not rocket science and you can do it too using our online training and proven implementation framework.
Learn what maintenance planning & scheduling is, how it creates value in an industrial environment and how to successfully implement it.
We offer a suite of courses on Maintenance Planning & Scheduling tailored for those leading an implementation (PS100), practitioners like planners and schedulers (PS200), managers (PS300), and frontline staff like Operators and Technicians (PS400).
Many implementations of maintenance planning and scheduling fail. Often because senior management was never on board to begin with.
In this article, I’ll show you how to fix that. I’ll show you how to sell planning and scheduling to your CEO. And in such a way that he actually wants you to implement it successfully.
I’ll talk about your ‘CEO’, but it could also be your Plant Manager that you need to convince.
Planning and scheduling is one of the 4 Essential Elements on the Road to Reliability™. Planning and scheduling or work management as it’s often called, ensures the right work gets done, at the right time, with the right tools, materials and people.
Without an advanced planning and scheduling process you’ll never achieve high reliability. In this article I’ll explain why that’s the case. I’ll also give an overview of what a work management process should look like.
Most organisations that implement maintenance planning and scheduling do not achieve the long-term results they expected. Often the improvements don’t last, even when the initial implementation seemed successful.
But, it doesn’t have to be like that. This article outlines a structured, proven
approach that has worked in many organisations. An approach using basic project management principles. Combined with a strong focus on change management.
Maintenance Planning & Scheduling (MPS) is one of the key elements of a reliable plant. When done right, it increases your workforce productivity by at
There’s a big difference between busy and productive. A lot of times, maintenance technicians are busy juggling hundreds of tasks in a day. They’re busy
How’s your maintenance budget? Chances are you think it’s not enough. And you resent that it’s been cut back for the umpteenth time. Every organisation
Contact Us:
Call in Australia: 1 800 312 402
Call from overseas: +61 2 836 626 74
Email: [email protected]
Address:
Level 14, 167 Eagle Street
Brisbane, QLD 4000
Australia
© 2017-2023 R2 Reliability Pty Ltd.
All Rights Reserved. | Privacy Policy | Terms of Use | Cookie Settings
© 2017-2023 R2 Reliability Pty Ltd.
All Rights Reserved. | Privacy Policy | Terms of Use | Cookie Settings