When people talk about predictive maintenance, it is often used as a synonym for condition-based maintenance. But in my view, with the advent of artificial intelligence, lower cost of equipment sensors, and machine learning—there’s a clear difference between predictive maintenance and condition-based maintenance.
And that’s what I’ll be talking about in this article. I’ll discuss what predictive maintenance is, the difference between condition based maintenance and predictive maintenance, and how our industry has grown to use machine learning and AI to better predict impending failures.
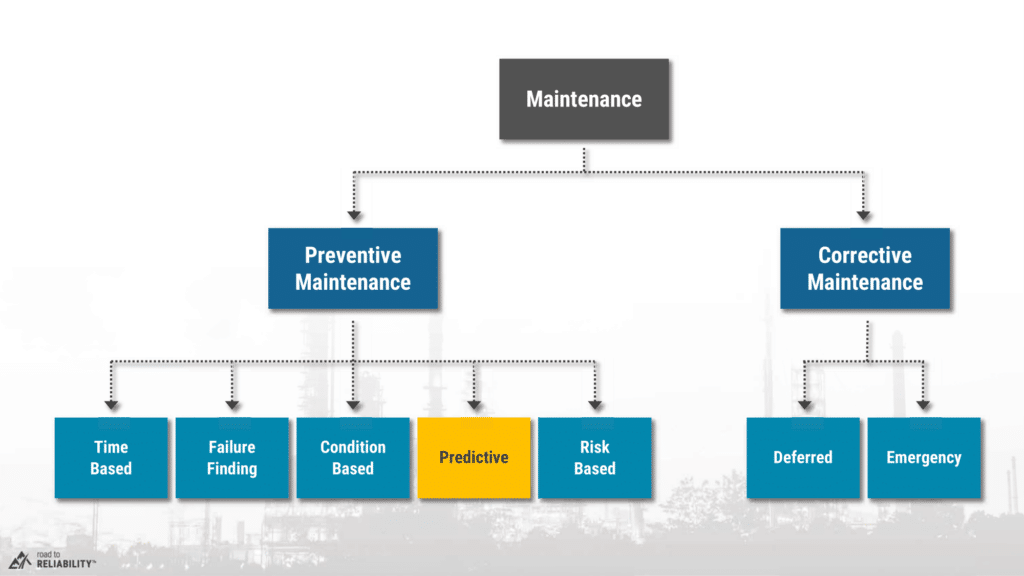
As we’ve discussed in the article, “The 9 Types of Maintenance: How to Choose the Right Maintenance Strategy”, predictive maintenance is a form of preventative maintenance because it is something we’re doing BEFORE failure has occurred.
I see predictive maintenance as a more advanced form of condition based maintenance, where we use different process parameters to determine if our equipment is moving away from stable operating conditions. We also rely on advanced systems to make predictions about the remaining operating life and when we need to intervene.
That means predictive maintenance is only effective when you have various measurements you can use to determine if the failure is becoming more imminent. And if you have a valid model used to make predictions.
Shift in Technology
Now, there has been an enormous shift in technology since the 1990s with cheaper and more powerful computers coming into the market, which is what you can see represented by the green line in the graph here:
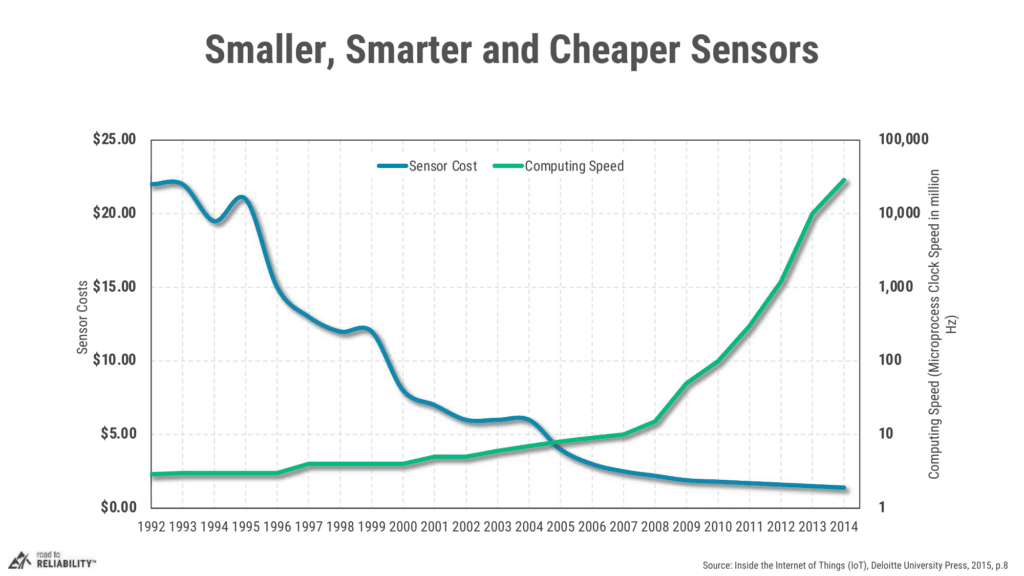
Since the early 1990s, microprocessor speeds have increased more than 10,000 times. At the same time, the cost of almost any type of sensor has come down dramatically too. The internet has become mainstream, cloud computing has become the norm, and in the last decade or so, machine learning and artificial intelligence have moved ahead in leaps and bounds. As a result, we’re now seeing a rapid move towards more condition-based and predictive-based maintenance.
Evolution of Maintenance: 4th Generation
This rapid shift in technologies enabled the development of the fourth generation of maintenance.
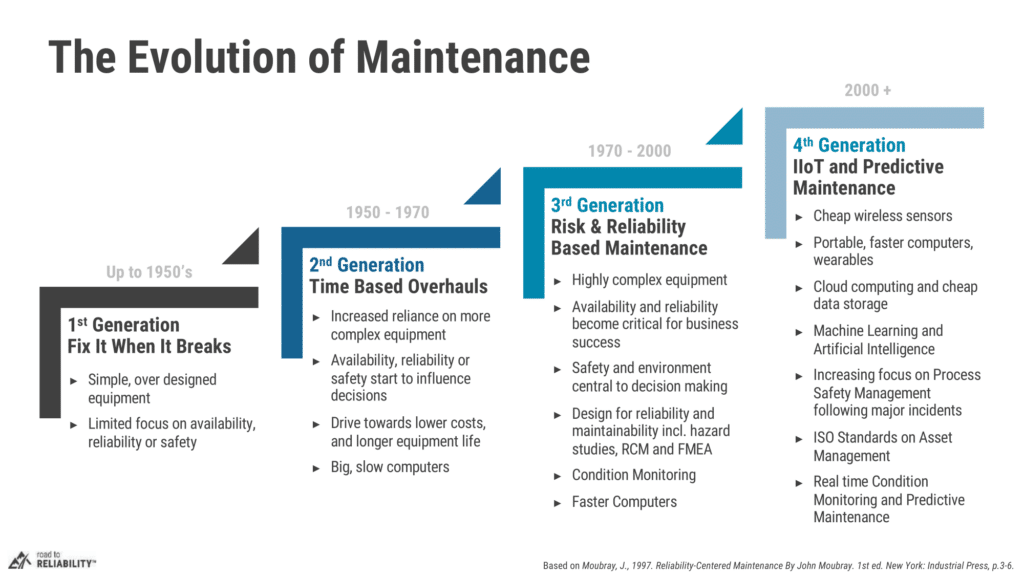
The problem is that many plants worldwide waste resources chasing fourth-generation maintenance practices when they still don’t have the basics in place. They try to leapfrog from a reactive first-generation state to advanced predictive maintenance. As a result, they spend hundreds of thousands of dollars on software and technology but gain little to no improvements in reliability.
Instead, you need to build an effective and efficient preventive maintenance program. And that will be a mixture of second, third, and eventually, fourth-generation maintenance practices. And as I discussed in the article, “9 Principles of Effective PM Programs based on Reliability Centered Maintenance (RCM)”, some failure modes will effectively be managed with time-based maintenance. Others will require condition-based maintenance, and only a very small portion of your failure modes will benefit economically from predictive maintenance.
Condition-based Maintenance vs. Predictive Maintenance
Condition monitoring is a big component of predictive maintenance. The data we collect from condition monitoring provides a lot of information about the current and historical state of your plant and equipment.
With predictive maintenance, we take this data and combine it with actual failure data to develop a model that describes how our equipment might degrade, when it might fail, and when an intervention is required.
So, the big difference between condition-based maintenance and predictive maintenance is that with predictive maintenance, we have a machine learning or artificial intelligence-based model that predicts if failure is likely to happen and when a maintenance intervention is required.
4 Step Process of Predictive Maintenance
Condition-based maintenance is a three-step process of detect, analyse, and rectify. But for predictive maintenance, it now becomes a four-step process. That is because we now have a prediction step where we take the analysis results and extrapolate those results to determine what intervention should be made and when.
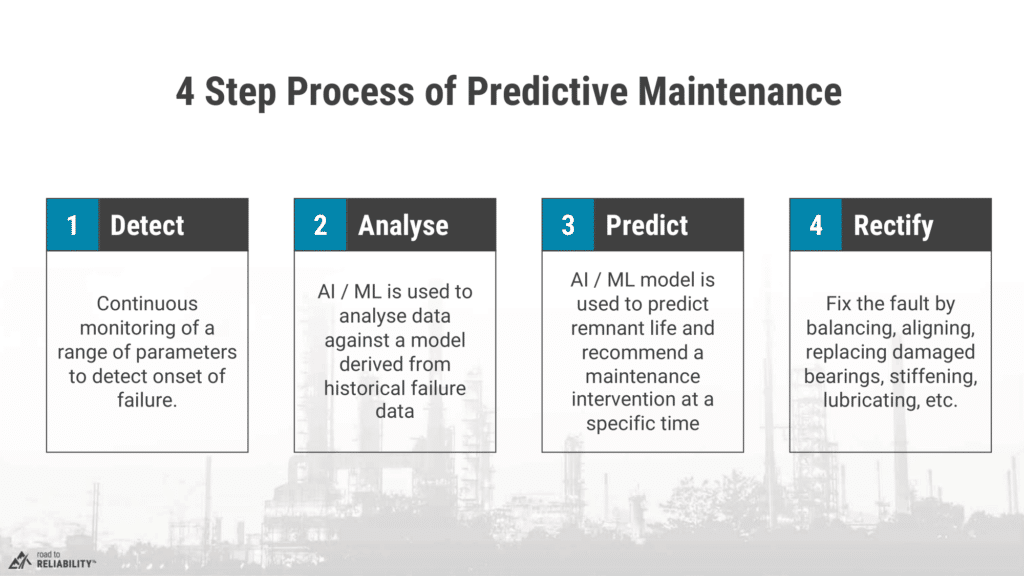
Condition based maintenance and predictive maintenance are very similar in many ways, but this machine-learning and artificial intelligence-based model sets predictive maintenance apart from condition-based maintenance. It is this exact model that makes predictive maintenance difficult and expensive to implement for several reasons.
First of all, you need to have a sizable set of failure data to train your machine-learning model. Now that’s not always possible. And in some cases, even not desirable.
Secondly, developing these models takes a lot of time, effort, and expertise. And that expertise does not come cheap and therefore it’s only warranted in complex or high-value applications.
Now with that said, the field of predictive maintenance is developing rapidly. So, it’s worth keeping your eyes on it. I strongly recommend that you don’t let all the sales talk out there in the market influence you too much. You need to keep an eye on the fundamental basics of good maintenance. Because for most assets out there, predictive maintenance should NOT be a priority early in their journey.
Evolving your PM Program
Now, when it comes to developing or improving your preventive maintenance program, don’t immediately rush to get predictive maintenance or other advanced software. It is important to start with the basics and build on those progressively. If you’re just starting and you’re looking to escape the vicious cycle of reactive maintenance, the first step is to get some basic preventive maintenance in place.
Go identify those age-related failure modes and get time-based PMs in place. Introduce failure-finding tasks for hidden failure modes, especially for your protective functions. Shortly after that, look at simple but effective condition-based maintenance practices to deal with the majority of your failure modes that have a constant rate of failure.
And at this point, you need to make sure you have an effective maintenance execution process in place to make sure you get issues remedied on time. Otherwise, you’re not going to be able to benefit from the value condition-based maintenance brings you. And that means you need to have a sound planning and scheduling process in place.
As you progress, it is time to start looking at whether you can leverage the relatively low cost of sensors and see if you can get more condition assessments to come in and expand the value you get from your condition-based maintenance. And maybe you can benefit from implementing risk-based maintenance. Only once you have done all that, it is time to start exploring whether predictive maintenance would add value to your business.
In short, you want to start simple. You need to build on what you have. For most businesses, predictive maintenance should be one of the last improvements you implement when it comes to your preventive maintenance program.