This article first appeared in reliable plant. You can read the first version of this article here.
Many maintenance organisations around the world are reactive. They experience excessive breakdowns, low productivity, and high maintenance costs. To break this reactive cycle, a common solution organisations implement is Condition-Based Maintenance. The problem is this strategy rarely works. They pay for CBM solutions but get the results of a run-to-failure strategy. Here’s how to avoid that.
Condition Based Maintenance (CBM) technologies are some of the most sold solutions in the field of maintenance. And with the recent interest in AI and the Industrial Internet of Things (IIoT), the market has now expanded even more with Predictive Maintenance (PDM).
It’s easy to understand why organisations opt for CBM or PDM solutions. The market tells us these platforms can pick up failures months before they happen. Plus, there is A.I. to tell them what to do and when, the software is easy to use, and it often integrates well with their CMMS.
Clearly these CBM and PDM platforms are the best thing since sliced bread.
But the truth is, when a reactive maintenance organisation invests in one of these solutions, it never delivers the promised value. The organisation continues to experience too many unacceptable failures that could have been prevented.
Here’s the shocker – it’s not because the technology is faulty, does not work, or that the vendor has delivered a poor-quality solution.
The problem is most reactive organisations are not ready to manage the solution they purchased. They are too reactive. Too busy with today’s emergencies to respond to the information their CBM system is providing.
In the rest of this article, I will discuss Condition Based Maintenance in greater detail, why you can’t achieve a reliable plant without it, the reason why most CBM efforts fail, and what you need to do to ensure that your Condition Based Maintenance delivers value to your organization.
First, let’s have a quick look at what Condition Based Maintenance really is.
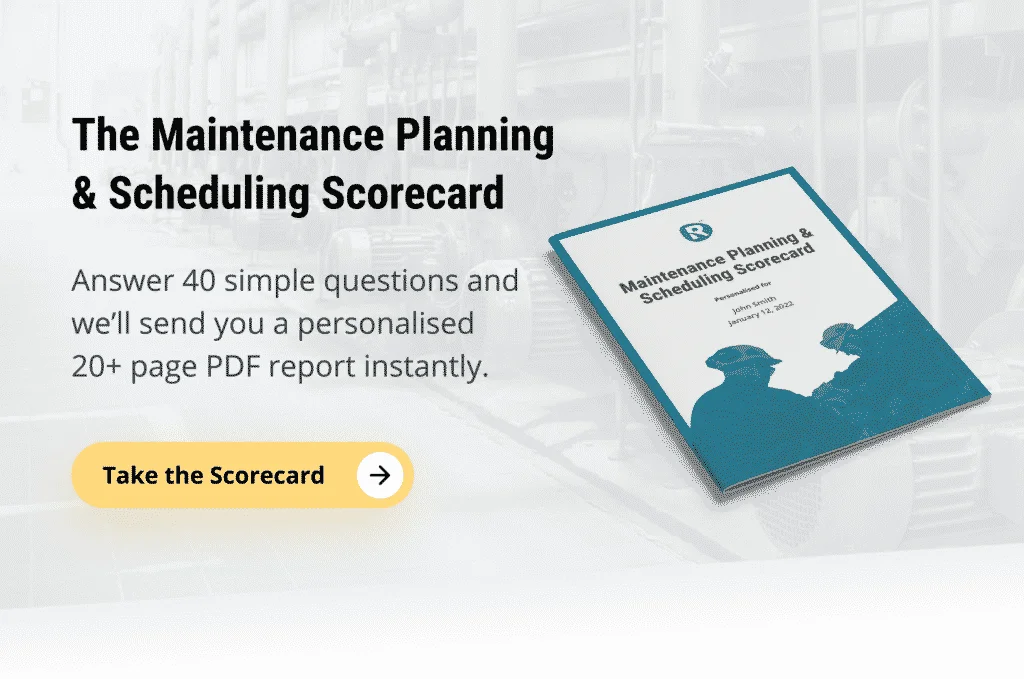
What is Condition Based Maintenance (CBM)?
Most failure modes are not age-related (more on that later). However, they do give some sort of warning that they are occurring or are about to occur. If we can find these signals, we can take preventive action to minimize the consequences of failure.
So as a strategy, CBM looks for physical evidence that a failure is occurring or is about to occur. When you think of CBM this way, you can see broader applications outside its more common uses like vibration monitoring.
An important concept within Condition Based Maintenance is the P-F curve shown in the figure below:
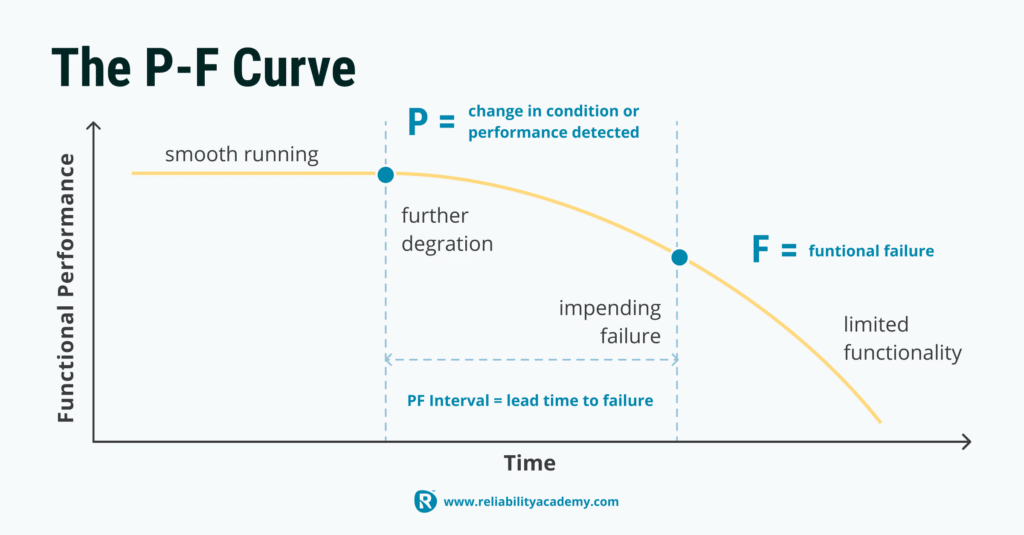
Source: 9 Types of maintenance: How to choose the right maintenance strategy
This conceptual diagram shows that the functional performance of equipment deteriorates over time to a point where a failure can now be detected (point “P”).
If the failure is not mitigated, the equipment continues to degrade until a functional failure occurs (point “F”). The time range between P and F, commonly called the P-F interval, is your window of opportunity to detect the imminent failure and address it.
The length of the P-F interval varies depending on the failure mode under consideration and the condition monitoring technique you are using.
You want to use a condition monitoring solution that gives you a reliable, repeatable indication early enough, so you have time to respond.
Why implement Condition Based Maintenance?
Condition Based Maintenance lets you know that a failure is about to happen. Which means you can now plan for it and pick the best time to address the pending failure.
For example, let’s say that next month, you have a scheduled outage. And according to your CBM, the drive-end bearing of your export pump is about to fail in about 3 months.
Without CBM that failure would hit you unexpectedly and you would have to deal with it as a breakdown. Breakdown maintenance is inefficient and expensive.
But with CBM you can choose to fix your pump during the scheduled outage. The work can be planned and scheduled properly. Meaning we get it done safer, faster, and at a lower cost. And we reduce production impact because we combine it with an existing outage.
So, to be very clear – the value of CBM is not that it prevents failures. Its identifying failures before they occur. As a result, you can make a timely intervention that can reduce production impact, reduce costs and improve safety.
But not all failure modes and all equipment will benefit from Condition Based Maintenance.
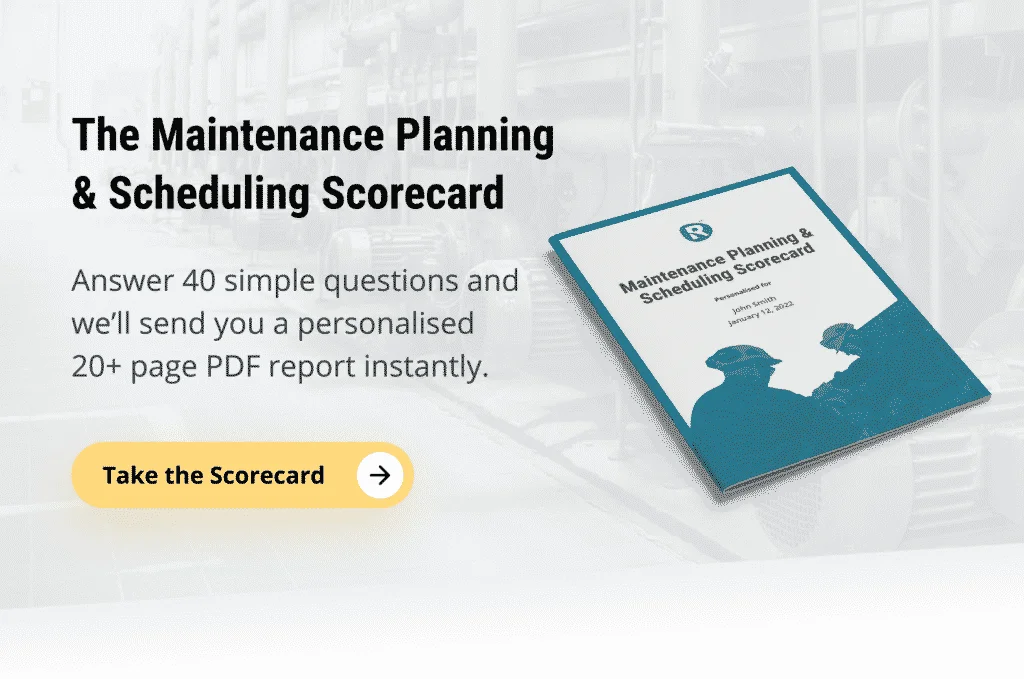
Time-based Maintenance vs. Condition-Based Maintenance
Failure modes that are clearly age-related are often best managed with a time-based repair or replacement task. If you know a component will wear out every 12 months, you simply replace it in time.
You’re not going to make a condition assessment every few months to determine if the component needs replacing. But research across different industries (airlines and military) has shown that somewhere between 70% to 90% of all failure modes are not age-related. For these failure modes the likelihood of failure does not (significantly) increase over time.
This research is summarized in the six different failure patterns shown below:
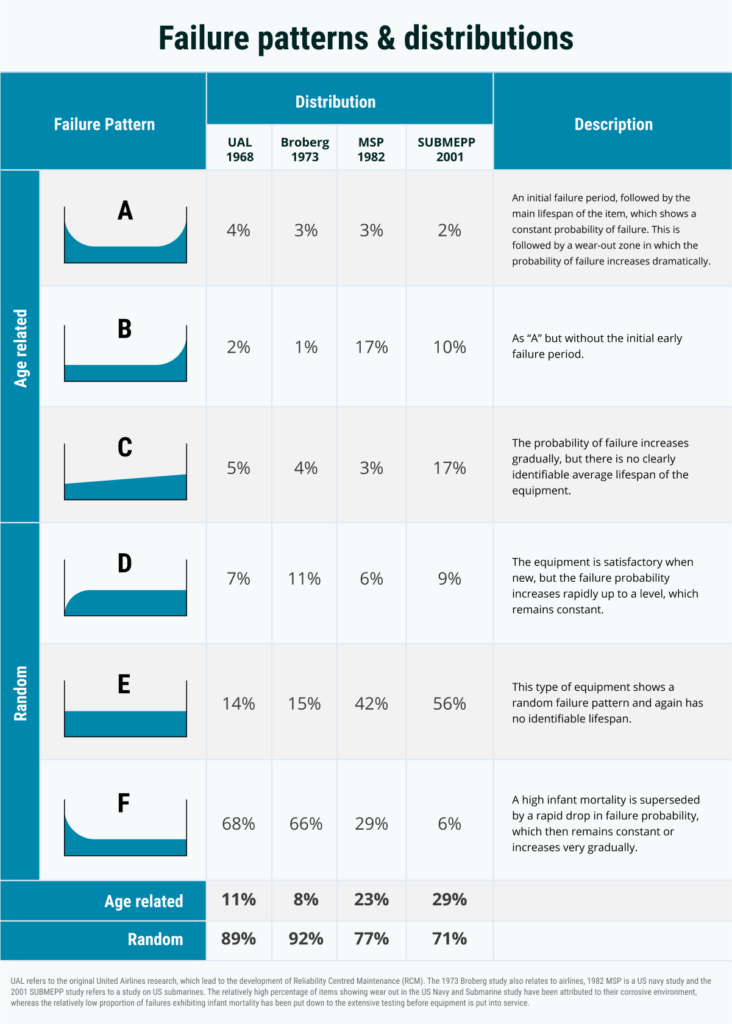
Source: 9 Principles of a modern preventive maintenance program
This has major implications for our PM programs which are filled with time-based maintenance tasks. Because if most failure modes are not age-related, then we should be addressing these failure modes by some type of Condition Based Maintenance instead.
And so, a very large part of your PM program should be Condition Based Maintenance. In other words, CBM is essential to creating a reliable plant. You will not succeed without it.
The Problem with Condition Based Maintenance
Effective condition monitoring generates ‘weak signals’ i.e., signals of potential failure weeks if not months in advance. But guess what happens to those weak signals in a reactive maintenance environment? They get ignored.
People are too busy dealing with today’s emergencies to worry about a pump bearing that might fail in 6 months’ time. So, 6 months later that exact same pump breaks down due to a bearing failure.
Management asks why that bearing problem wasn’t captured through the condition monitoring program. Only to be told that it was – the report with the vibration trends is there. The CMMS work requests were raised. But… nothing was done about it.
This is the worst of both worlds. You’re practicing run-to-failure…except it’s more expensive because you’re adding the cost of CBM to it.
Sadly, this is the reality in many places and to be honest, I have personally experienced it myself. To resolve this, organisations need to ensure they have an effective planning & scheduling process in place so the work environment becomes more stable and can act on the ‘weak signals’ that come from the CBM program.
Planning & Scheduling BEFORE Condition Based Maintenance
As we saw, for CBM to be effective as a strategy, early intervention is essential. This requires an efficient and effective process for data gathering, data analysis, decision making, and finally ensuring timely intervention is made. It is this last step, timely intervention, where reactive maintenance organisations typically fall down. These early interventions just don’t survive in the daily reality of many maintenance organisations, they are not seen as urgent enough until it is too late. For your CBM program to be effective you need to have a stable working environment:
- without too much reactive breakdown maintenance
- with clear and objective methods to prioritize work requests
- with an agreed way to load work into a Frozen Weekly Schedule
- where that Frozen Weekly Schedule is adhered to and actively protected
In other words, you need an effective planning & scheduling process in place before you implement a CBM strategy. It’s like building a house. You need to have the foundation in place before you add anything else. In the same way, you first need to have planning & scheduling in place so when you specify CBM as part of your PM Program, you can be sure that any required interventions will be executed on time. When I speak to CBM and PDM solution providers I hear this issue over and over again: their technology is flagging pending failures, but the maintenance teams are not getting to them in time. Their clients are not getting the value they expected and are not happy.
Planning & Scheduling Reduces Waste
In most maintenance organisations productivity is often poor, typically around 20% – 30%. This means that during a typical 10-hour workday, your technicians only spend 2 to 3 hours doing actual maintenance work. Sometimes even less. This is not because people don’t work hard enough. It’s because our systems and processes are inefficient and ineffective. Our day-to-day maintenance work is full of all kinds of waste:
- Poor quality work instructions that lead to delays and lost time during the completion of jobs.
- Incorrect identification of materials resulting in false starts, delays, or makeshift repairs.
- Poor co-ordination between work groups resulting in excessive waiting and idle time (e.g., waiting on equipment isolation).
Maintenance organisations are often tightly resourced as it is, and then having a typical productivity of 20% to 30% means our maintenance teams really struggle to get the work done. That eventually leads to a vicious cycle of reactive maintenance where the work that gets done first is the work that is shouted about the loudest – and guess what?
That won’t be our CBM work requests because nobody is super excited about a pending failure that is 3, 6 or 9 months away.
But with an effective maintenance planning & scheduling process you can remove a lot of this waste. My experience shows that relatively easily you can increase productivity from 30% to 45% and that is the equivalent of increasing your team by 35% without hiring anyone.
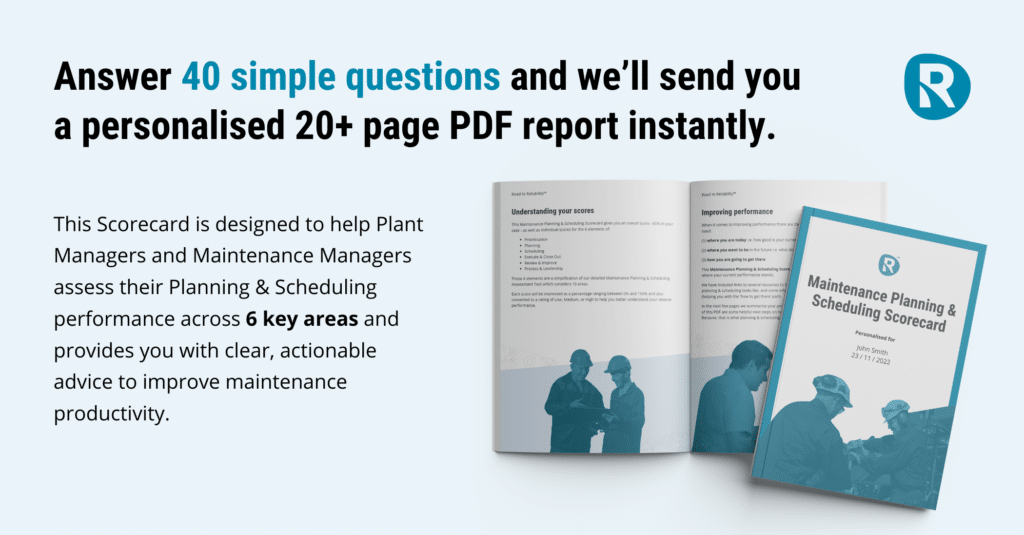
But not only that, if you implement a robust, effective process, your work environment also becomes less reactive. Teams finally find the time to get rid of those recurring problems. Your people are less frustrated and start to see the benefits of a reliability-based culture. And those early warnings from your CBM program will get the attention they deserve.
If you want to know where your gaps are when it comes to maintenance planning & scheduling, then you can use this scorecard that provides personalized feedback and recommendations on how to improve: Maintenance Planning & Scheduling Scorecard.
Achieving Success with CBM
Let’s be clear, Planning & Scheduling is an essential prerequisite before you implement a Condition Based Maintenance program – without it your CBM efforts will fail. But there is of course a lot more to creating an effective CBM program.
You need to understand the failure modes and failure consequences of the equipment you’re managing so you can make a sound assessment of what CBM solution is appropriate.
You clearly need to understand the condition monitoring techniques you are planning to use.
Your team needs to be trained to use the equipment, analyse the data, and make robust recommendations on when and how to intervene.
You may need to implement new software solutions.
And you certainly will need to manage the implementation of your CBM program as a project with a clearly defined scope and success criteria.
All that falls well outside the scope of this article.
Final Thoughts
Condition Based Maintenance is essential to creating a reliable plant because most failure modes are not age-related and can only be effectively managed with CBM.
The problem most organisations face, however, is that they operate in a reactive maintenance environment and are unable to effectively deal with the ‘weak signals’ that CBM provides.
Implementing CBM too early is a waste of time and money. To make CBM successful in your organisation, you first need to have a stable working environment in place so that you can act in a timely fashion on the early warning signals that your CBM program will provide.
You create that stable working environment with an effective maintenance planning & scheduling process.