What is Reliability Centered Maintenance?
Have you ever wondered how efficient we can get with our preventive maintenance tasks? Is there some sort of maximum efficiency that only the Gods of maintenance know of? Maybe.
But for mortals like us, there is what I call a gold standard that we can strive for. It’s called Reliability Centered Maintenance (RCM). To maximise equipment reliability, minimise the frequency with which equipment failure occurs, and experience reduced maintenance costs, it’s important to optimise maintenance tasks and consider implementing a Reliability Centered Maintenance (RCM) program.
As maintenance professionals, you’ve probably seen this maintenance strategy in your organisation or at some other plant. And you’ve probably heard of the praises that RCM processes get. But what is it really about?
What is Reliability Centered Maintenance (RCM)?
There are plenty of definitions out there, including many poor ones. To save us time, I’ve taken the definition from various reputable sources such as Weibull, Aladon, John Moubray, and Anthony ‘Mac’ Smith. And mixing in my personal experience with reliability centered maintenance as a maintenance strategy, I’ve summarised what RCM is:
Reliability Centered Maintenance is NOT a tool or a piece of software.
It is an internationally defined, structured decision-making process.
We use it to define or optimise our PM program, focusing on preventing system failures rather than preserving equipment availability.
When done well, RCM will deliver highly effective and efficient preventive maintenance programs.
Now, applying RCM principles allows us to determine the appropriate maintenance tasks for each asset, ensuring that the maintenance strategy directly addresses the unique operational context and reliability requirements of your system.
And when it comes to developing & improving PM programs, RCM is the most robust and standardised process that is proven to yield exceptional results when done well. However, reliability centered maintenance does have a few drawbacks.
Drawbacks of RCM
A successful implementation of reliability centered maintenance requires two things:
- Deep knowledge and experience of both the RCM process, as well as the plant and equipment that is being analysed.
- Significant resources and effort to yield results.
Because of this, you need to be wise about when, where, and how you deploy RCM. You don’t want to implement it everywhere in your organisation. If you don’t pick the right situation and deploy it when it is not the most appropriate, you’ll unnecessarily bloat up your maintenance costs without getting the results you’re looking for.
Many organisations don’t realise this and try to implement reliability centered maintenance everywhere. As a result, it does not become a cost effective maintenance strategy. And when they fail, or see that their RCM program is too expensive, that’s when they say things like—
“Enough of this RCM nonsense, it’s too expensive.”
And that brings me to another definition of RCM that maintenance practitioners often have in their minds:
Resource Consuming Monster.
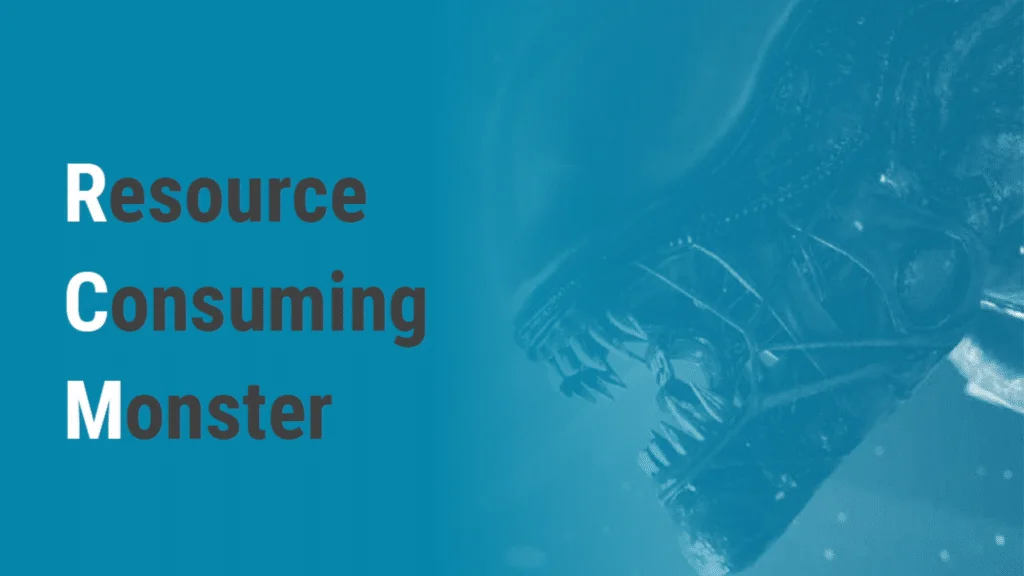
And as funny as it may seem, it’s actually quite tragic. Because RCM is one of the most valuable and powerful maintenance strategies we have in our arsenal when it comes to optimising our PM programs.
RCM’s Bad Reputation
Reliability centered maintenance as a cost effective maintenance strategy is so badly understood, so badly implemented in so many places around the world, that it has gotten a bad reputation. And that poor reputation is the result of inexperienced people. Whether they are staff, contractors, or expensive consultants… they lead RCM projects, whilst they—
1. don’t fully understand the reliability centered maintenance process
2. do not have the resources to successfully implement it
3. they don’t have the ability to effectively lead the implementation
4. they don’t fully understand your plant’s operational context such as your maintenance management processes, your maintenance tasks, your bad actors, and your working environment
And the result is poorly executed projects where a lot of time and money have been spent for relatively few gains (no wonder many people end up giving it a bad name). But when executed by a team of experienced and knowledgeable professionals, RCM will give you the best possible output.
International Standards: SAE Standard, JA1011
To ensure that our reliability centered maintenance programs are cost effective, we have to adhere to a standard evaluation criteria for reliability centered maintenance. Yes, our gold standard has associated performance standards to adhere to as well. And the Society of Automotive Engineers (SAE) have developed two widely accepted international standards to define what RCM is and how to apply it.
- The SAE standard. JA1011 titled Evaluation Criteria for Reliability Centered Maintenance Processes – outlines the criteria our process must meet before it can be deemed an RCM process
- And SAE standard, JA1012 titled, A Guide to The Reliability Centered Maintenance Standard – provides a lot more background and explanation to help you understand the first standard.
Let’s look at the SAE standard, JA1011.
The JA1011 outlines the requirements a process must adhere to if it’s allowed to call itself an RCM process. And really, it all boils down to answering seven questions.
The Seven Questions
The most fundamental requirement of RCM processes is that they must adequately and completely answer the following questions:
- What are the functions and associated design performance standards for the asset in its current operating context?
- In what way can the asset fail to fulfill its functions?
- What causes each possible functional failure?
- What happens when each function of failure occurs?
- In what way do each equipment failure matter?
- What should we do to predict or prevent each equipment failure?
- What should we do if a suitable proactive task cannot be found?
These seven questions form the backbone of your reliability centered maintenance strategy. And they’re relatively straightforward and easy to understand. But, when you start looking at what is required around these seven questions, you’ll see that the standard JA1011 does actually add in a lot of additional requirements that you need to meet to do an RCM analysis. Now, those additional requirements are too detailed to discuss in one blogpost. So, I summarised it all in this chart.
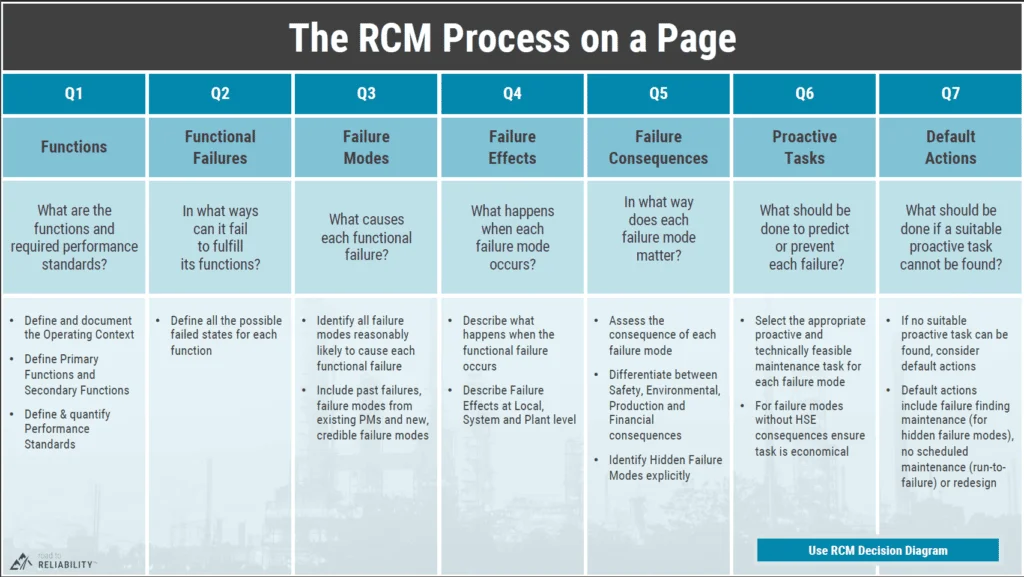
I discuss each point in greater detail inside my course. But for now, it’s enough that you understand the high-level view of what RCM processes are.
Recommendations
If you really need to conduct a reliability centered maintenance program (RCM), here are a few recommendations to get you started on the right track.
- RCM analysis should only be done for a small number of your equipment—the most troublesome, most expensive, or most impactful.
- Make sure the person leading the implementation is really an expert at RCM. Ideally, you should find a proficient RCM facilitator to help you. If you can’t afford that, then don’t bother doing it yourself. You’re going to waste time and won’t get the results you’re looking for. You’re better off trying other maintenance strategies.
- Be careful when looking for people to help you with your RCM program. There are many service providers that say “Yeah we can do RCM analysis,” but really they can’t. They lack experience, expertise, and knowledge.
By knowing about RCM yourself, you’ll know what questions to ask when looking for your RCM facilitator. Yes, reliability centered maintenance programs are the gold standard when it comes to maintenance strategy. But it does carry a steep price. So make sure that you are well informed of what this maintenance strategy entails before investing huge amounts of resources in it.