Is doing more maintenance ‘good’?
It’s common to think so. I mean, it makes sense that the more maintenance you do… the less likely your equipment is to fail.
Right?
But if that’s the case…
Why do we still suffer from poor reliability?
Why do we still struggle with emergency breakdowns?
Why do we struggle with expensive maintenance costs?
“Can’t we just do more maintenance to improve reliability?”
Unfortunately, it’s not that easy. And research shows otherwise. Waddington and his research team proved just how wrong that conventional thinking really is.
In this article, I talk about the ‘Waddington Effect’, why it is important in today’s modern maintenance programs, and what the implications are when it comes to how we implement maintenance.
What is the Waddington Effect?
In an article called “The Waddington Effect”, Dr. James P. Ignizio discusses the research work done by C. H. Waddington during World War II.
He coined the term “Waddington Effect”, which shows that preventive maintenance inspections of British bombers increased the rate of breakdowns immediately after their maintenance.
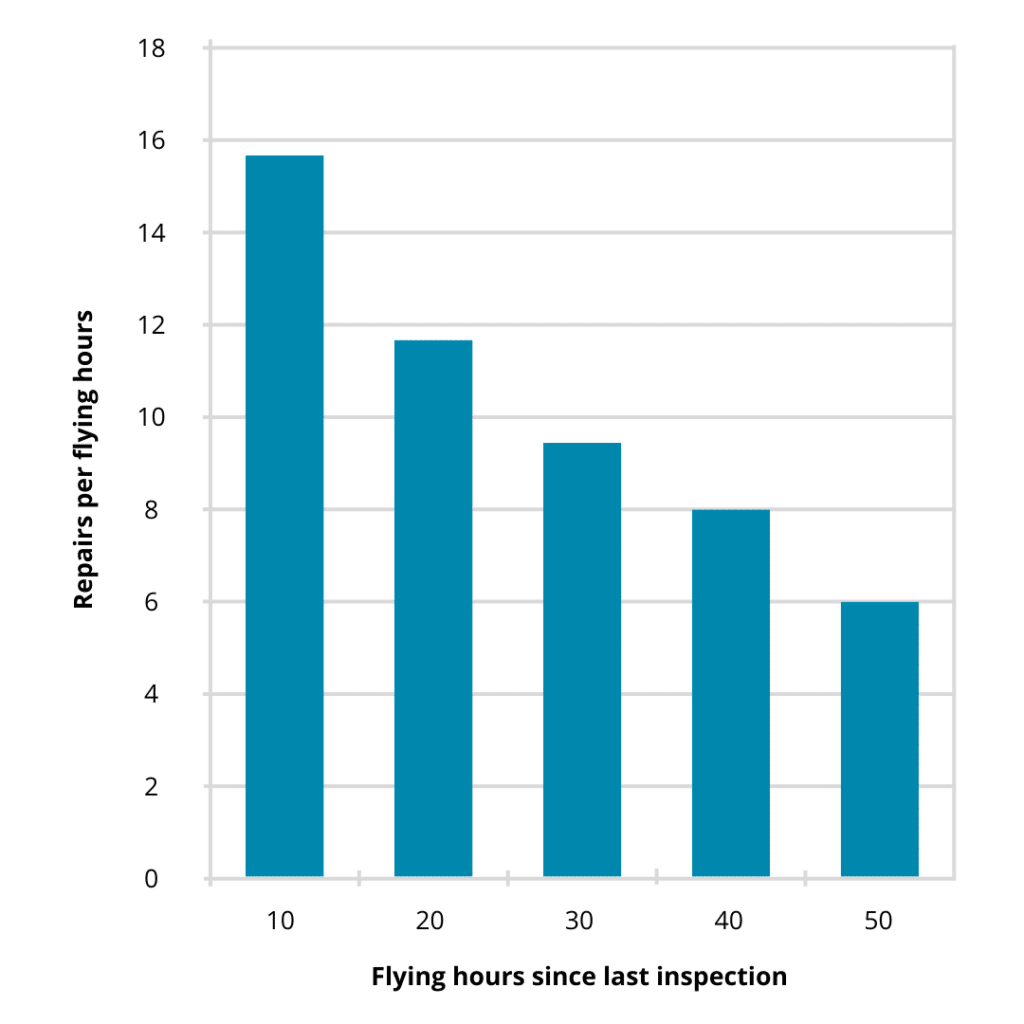
Figure 1. The Waddington Effect with Bomber Command (Taken from the article: The Waddington Effect, C4 U-Compliance, and Subsequent Impact on Force Readiness)
“As Waddington observed, the number of repairs increased after maintenance, ultimately settling down to roughly 6 repairs every 10 hours – at about which time the next maintenance event was scheduled.”
You can read the full article on Waddington’s work here:
The Waddington Effect, C4 U-Compliance, and Subsequent Impact on Force Readiness
But to summarise…
Waddington and his team concluded that maintenance inspections actually led to MORE equipment malfunctions due to the disruption of an otherwise satisfactory condition.
They argued that PMs were too frequent, and that it could be the cause of, rather than the solution to, emergency repairs.
To solve this, they proposed and ultimately accepted improvements to the maintenance schedule:
1. extending the time between repairs
2. identifying components that need to be included or excluded in a particular maintenance event
3. better allocating and scheduling maintenance staff
4. and developing clearer, more concise, and unambiguous documentation.
Implementing these recommendations resulted in a remarkable increase in airplane availability and the effectively increased the size of the British Coastal Command air fleet by over 60%…
…but much less costly and time-consuming than actually increasing the aircraft fleet.
What does this imply for our preventive maintenance programs?
The findings from Waddington’s research have great implications for our modern maintenance programs.
The Waddington Effect provides modern maintenance programs with a blueprint for how to approach asset management in a way that is efficient, cost-effective, and maximises equipment lifespan. And to achieve that, there are three things you need to understand and apply:
1) First, you can’t maintain your way to reliability.
This is very evidently shown in Waddington’s research.
In fact, he showed that doing more maintenance actually results in more emergency repairs.
That’s because maintenance can only preserve your equipment’s inherent design reliability and performance. If the equipment’s inherent reliability or performance is poor, doing more maintenance will not help.
No amount of maintenance can raise the inherent reliability of a design. To improve poor reliability or performance that’s due to poor design, you need to change the design. Simple.
When you encounter failures that relate to design issues, you need to eliminate them. Sure, the more proactive and more efficient approach is to ensure that the design is right, to begin with. But all plants startup with design defects. Even proactive plants. And that’s why the most reliable plants in the world have an effective defect elimination program in place.
2) Second, the more intrusive maintenance you do, the more human errors you introduce.
Which results in more defects.
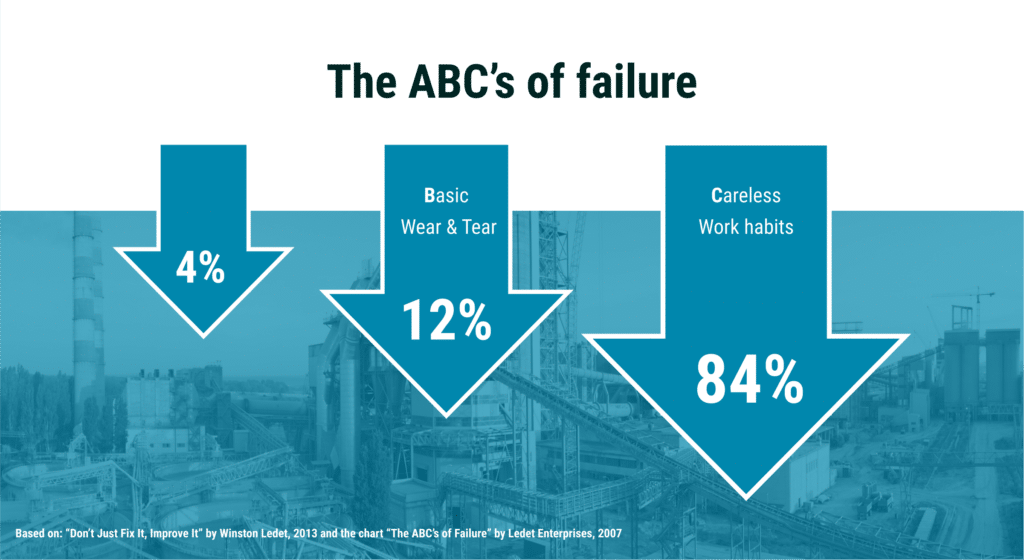
As I discussed in the article, Defect Elimination: Why you can’t do without, up to 84% of all defects are caused by careless work habits, which become failures over random periods of time.
You see, we introduce defects at every stage of a plant’s life cycle: during the design, construction, and commissioning of our plants.
Including the operation and maintenance phases.
If you don’t tackle these defects, they will eventually lead to failures.
3) And lastly, documentation is important.
Interestingly, the British Operational Research team was particularly surprised at the significant impact that proper documentation had on achieving these results.
I discuss in my course how documentations like job plans and work instructions are key to your success because they help you manage human error, reduce variability, and improve safety.
Summary
The Waddington Effect suggests that more maintenance is not always the solution to poor reliability and emergency breakdowns. In fact, they concluded that more maintenance inspections actually led to more equipment malfunctions. And that’s because of disruptions to an otherwise satisfactory condition.
To solve this, they proposed improvements to the maintenance schedule, such as extending the time between repairs, identifying components that need to be included or excluded in a particular maintenance event, better allocating and scheduling maintenance staff, and developing clearer, more concise, and unambiguous documentation.
The findings from Waddington’s research have implications for modern maintenance programs. To achieve this, three things need to be understood and applied: 1) you cannot maintain your way to reliability; 2) more intrusive maintenance introduces more human errors, which results in more defects. Careless work habits cause up to 84% of all defects, which eventually lead to failures.
Lastly, proper documentation is important. Job plans and work instructions help manage human error, reduce variability, and improve safety. By implementing these recommendations, modern maintenance programs can achieve more efficient, cost-effective, and maximised equipment lifespan.
Now, with that said…
Is your PM program optimised to follow these principles?
If not, then there’s room for improvement.
If you want to train your team to do LESS maintenance but still improve your overall reliability…
If you want to avoid intrusive maintenance tasks so you introduce less human error…
If you need tools and templates to properly implement and document your preventive maintenance process…
Then schedule a call with me.
Let’s discuss how we can train your team in optimising and developing your preventive maintenance program.