Download our eBook now and learn the Road to Reliability™ Framework
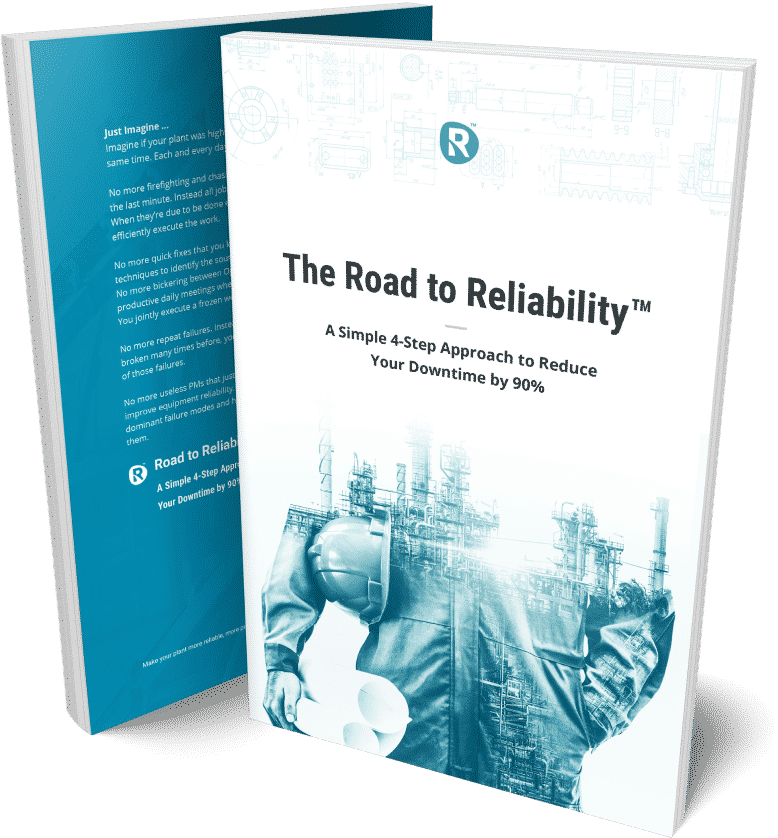
Mining & Metals is one of the world’s oldest industries provides an essential input into many other industries. As of 2019 the combined revenue of the top 40 global mining companies amounted to 692 billion U.S. dollars. The industry has a wide range of plant types from open-cut and underground mines, to fixed plants, smelters, and refineries. The mobile equipment used in the mining is of a scale not used in any other industry and sets unique requirements and challenges. The fixed equipment is unique in some ways and tends to see strong wear and tear.
What is not unique is the importance of generating value from capital-intensive assets and the need to drive high reliability, high availability, whilst optimising costs, and ensuring safety.
And that’s exactly why the Road to Reliability™ framework is highly relevant to many companies operating across the Mining & Metals industry. It is a simple, but effective framework based that will help you to get the basics in place, the basic that really matter and that will significantly improve both your availability as well as your reliability:
And it doesn’t really matter whether you operate an offshore platform, an onshore LNG plant, a refinery or unconventional oil or gas fields, in all cases these basic practices will drive significant value. And in all cases, you can make huge improvements using your own staff.
If you want to know more about how the Road to Reliability™ framework can help you and your team improve your maintenance & reliability performance download the Road to Reliability™ eBook. Or if you’re a manager and want to train your team to make real improvements that improve your organisations bottom line Schedule a Call.
Contact Us:
Call in Australia: 1 800 312 402
Call from overseas: +61 2 836 626 74
Email: [email protected]
Address:
Level 14, 167 Eagle Street
Brisbane, QLD 4000
Australia
© 2017-2023 R2 Reliability Pty Ltd.
All Rights Reserved. | Privacy Policy | Terms of Use | Cookie Settings
© 2017-2023 R2 Reliability Pty Ltd.
All Rights Reserved. | Privacy Policy | Terms of Use | Cookie Settings