Last week, I talked about how different sources of waste are impacting your maintenance performance and your plant’s reliability.
This week, let’s get into more detail on how waste is reducing the efficiency of your day-to-day maintenance execution. When you take a look at the Weekly Schedule of your maintenance crew, it will be full of productive work …
… but when you look at what an actual day for your crew looks like, you’ll see plenty of unproductive work. You’ll see plenty of time spent on
… meetings
… looking for parts
… waiting on permits
… waiting on instructions
… waiting on other trades
… waiting on Operations to isolate the equipment
In short, the days of your maintenance crews are full of delays. Delays during jobs. And delays between jobs.
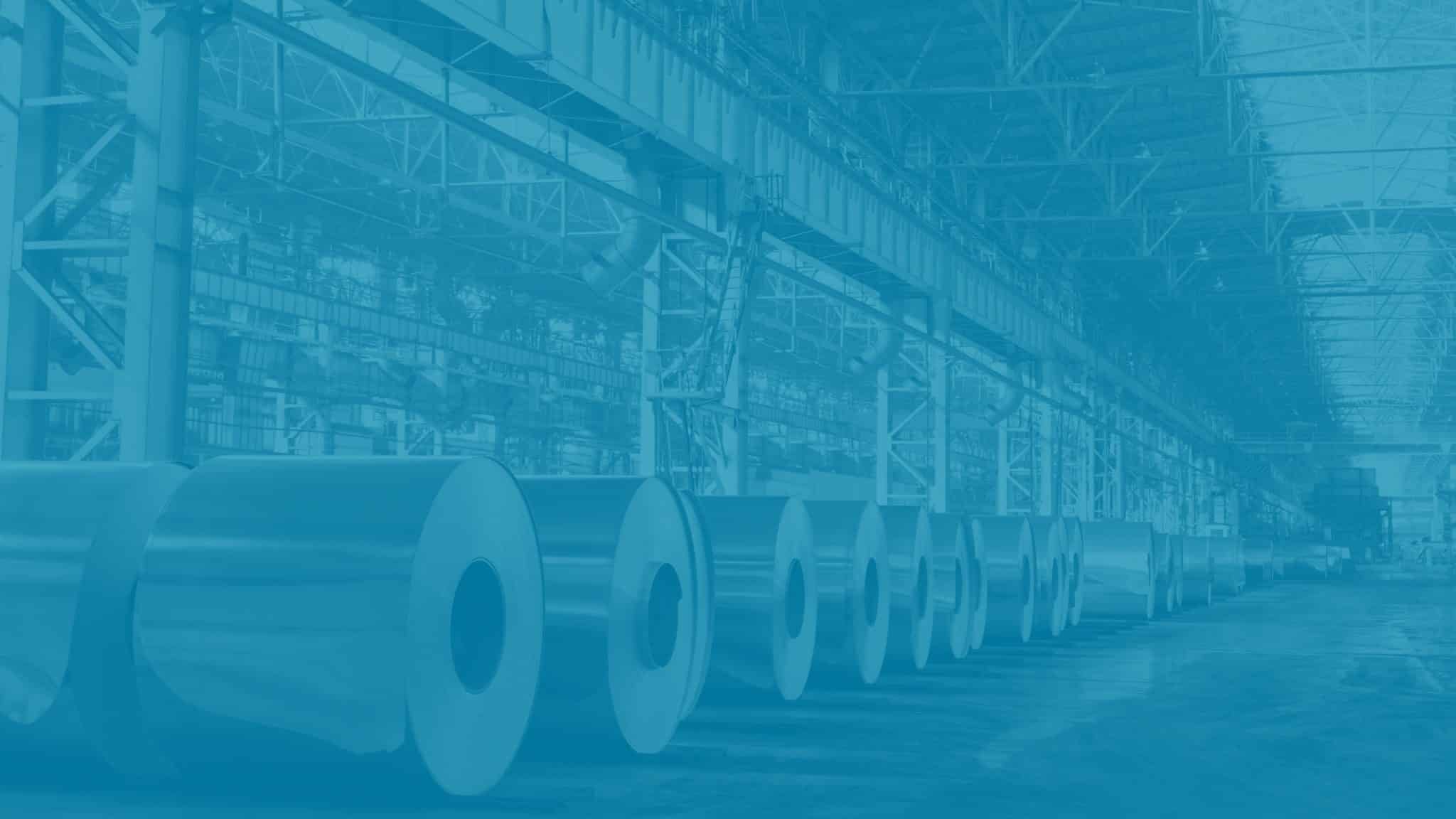
You can eliminate many of these delays by implementing a proper Planning & Scheduling process – increasing your wrench time from a typical 30% to 45%
Which is the equivalent of increasing your workforce by 35% – without hiring anyone! There are many versions of this process out there… but, in essence, they all come down to the same basic steps.
Here is an overview:
Step 1 – Identify & Prioritise
The process starts with identifying the work and creating quality work requests.
Poor quality work requests could result in incomplete work plans, missing parts ,or other delays. To get high-quality work requests, train your people to a standard, and quality-check all new work requests.
Once you have quality work requests that have been reviewed, prioritise which ones need immediate attention. This is where a lot of organisations go wrong – they don’t use an objective method of prioritising work. Whoever shouts the loudest gets their job done. The result is a highly reactive maintenance environment.
Getting your prioritisation fixed is key to protecting your schedule and escaping the vicious cycle of reactive maintenance
Step 2 – Plan
The next step is the actual planning process. Have a planner identify all resources, materials, and services required to do a job. This will minimize any on-the-job strategizing and running around looking for parts.
Once that’s done, your planner creates a work pack, containing all the required information needed to do the job, like:
- drawings
- procedures
- list of spare parts and consumables
- list of special tools or equipment
- access or lifting requirements.
It’s the Planner’s duty to prepare the most effective, efficient, and safest way to do a job
Step 3 – Schedule
Next, a scheduler prepares the Frozen Weekly Schedule that lists all the work due the next week. Schedule the work in a way that optimizes your workflow by grouping together related jobs…
… jobs that need the same parts, tools, or people, or jobs on the same equipment or location. Productivity increases if staff can easily move from one job to a nearby job. Or do multiple jobs on the same equipment.
Step 4 – Execute
Next is maintenance execution. Everything we’ve done so far is to make execution safe and efficient. The maintenance crew executes the work based on the work packs provided by the Planner.
This step essentially revolves around a cycle of:
- allocating work
- executing work
- managing emerging work
- reporting daily progress
- and reinstating equipment
If there are missing parts, emergency maintenance, or changes in methodologies during this step …
… then it is the Maintenance Supervisor’s responsibility to adapt to the changes.
It is important to give the planner feedback on what went well and what went wrong so that they can improve the job plans for next time. Continuous improvement is key to your success!
Step 5 – Close out
After the crew has finished doing the work, the next step is reporting the technical history, work history, and areas for improvement. This is one of the most important steps in the process. Without it, there is no improvement. Unfortunately, it is also one of the steps that many ignore.
As part of this step, the Supervisor:
- Confirms all work is complete and meets the required quality standards;
- Reviews and approves the technical history in the CMMS;
- Makes sure the Planner receives feedback on the quality of the job plan;
- Initiates a Root Cause Analysis if required;
- Ensures unused materials are back in the warehouse;
- Initiates payments.
Step 6 – Review and Improve
Finally, the key to increasing your productivity is reviewing and improving your performance. You won’t jump from a low 20% or 30% productivity to world-class performance overnight. That takes time. Continuous improvement is the name of the game.
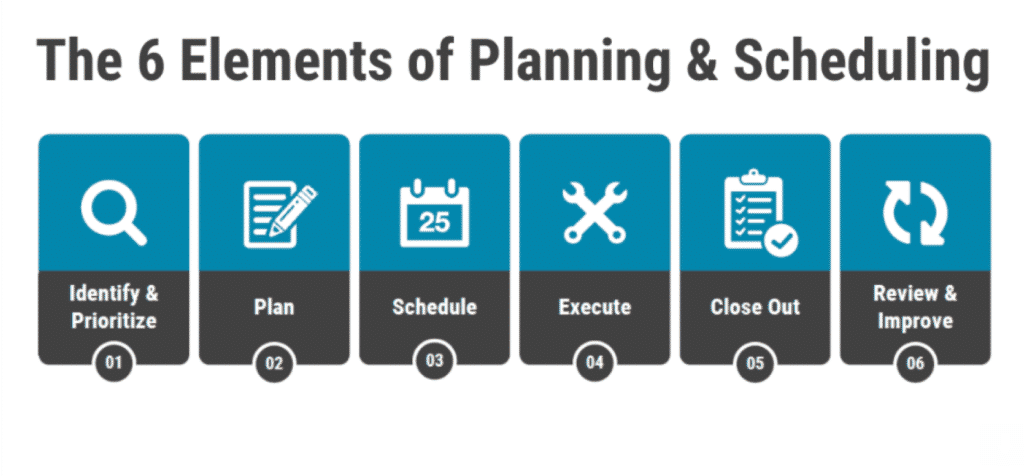
Again, everything that I mentioned so far is just a summary.
If you want to learn more, you can read the rest of the article or check out our online course on Maintenance Planning & Scheduling.