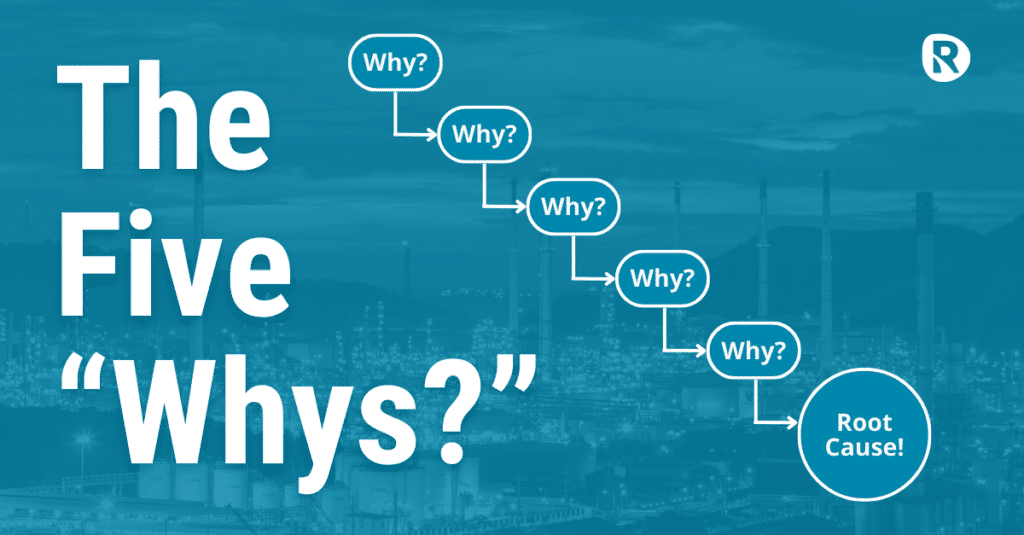
As maintenance practitioners, we’ve all have heard about the 5 Whys.
And chances are, many of us have used this approach to execute Root Cause Failure Analysis at some point in your career.
While it may seem like a simple and easy-to-use tool to look for root causes, you need to approach the 5 Whys with a deeper understanding of the process and the desired outcome.
In this article, let’s explore what the 5 Whys process is, the misconceptions surrounding the 5 Whys, and discuss how to effectively utilise it in your organisation for effective root cause failure analysis.
What is Root Cause Failure Analysis (RCFA)?
Root Cause Failure Analysis (RCFA) or Root Cause Analysis (RCA) is a method used to investigate, understand, and resolve failures in a systematic way. Its main goal is to identify the fundamental reasons why a failure occurred, and address these reasons to eliminate root causes and prevent future failures and safety incidents.
Root Cause Failure Analysis is widely used in various industries such as manufacturing, aviation, oil and gas, and transportation to improve safety and reliability, quality improvement, reduce costs, and enhance operational performance. It’s a proactive tool that not only fixes problems but also fosters a culture of continuous improvement.
What is the 5 Whys approach for Root Cause Failure Analysis?
The 5 Whys (sometimes called 5Y) is a simple analysis process developed in Toyota to conduct root cause failure analysis by simply asking ‘why‘ five times.
The creator of the Toyota Production System, Taiichi Ohno, described the 5 Whys as—
“The basis of Toyota’s scientific approach… by repeating ‘WHY’ five times, the root causes of the problem as well as its solution become clear.”
Many professionals view the 5 Whys process as an easy and convenient tool for frontline staff to identify the root causes of a failure.
Here’s an example:
- A pump failed. Why?
- Because a bolt came loose. Why?
- Because of a mechanical error. Why?
- Because the technician was tired. Why?
- Because he/she didn’t get enough sleep.
With the 5 Whys, you don’t use a complicated process or software like when you do an Apollo root cause analysis. You don’t need the 2–3-day training to learn the Apollo RCA process either. And you don’t need to do any complicated fault tree analysis.
The 5 Whys process doesn’t require statistical data collection, data analysis, or advanced tools. It quickly helps you get to the root cause of the problem. Anyone can use it. And it encourages a structured approach to problem-solving, which can be beneficial in various contexts.
Not only that, but it also encourages team collaboration by allowing you to discuss and question together. Teams can converge on the root cause and collaborate on solutions, maintenance procedures, and appropriate maintenance tasks.
5 Whys are quick and easy.
They are just what we need for an effective root cause analysis of our equipment failure! Right?
But are they really?
Despite its apparent simplicity, the 5 Whys may not be as straightforward as it seem. To make the most of this technique, you must be aware of its limitations and avoid oversimplifying the problem-solving process.
The Problem with the 5 Whys
The main problem I see with 5 Whys when used to conduct root cause failure analysis is that people focus on the tool, instead of the process and the desired outcome.
People somehow assume that just because the impact of a failure is low, the root cause can be easily established.
Also, some complex problems may have multiple root causes or causal factors. And the 5 Whys might make it seem like there’s only one, making us overlook potential failure modes. And so there’s a danger of stopping at symptom-level causes without getting to the true root cause, which ultimately leads us to the wrong conclusions.
And that’s where we go wrong.
We must understand that getting to the bottom of a major failure can be simple. And at the same time, analysing a minor failure could actually turn out to be technically complex.
To avoid this pitfall, you need to approach the 5 Whys with flexibility and openness to other techniques if the initial analysis indicates a more complex issue.
Using the 5 Whys Effectively for Root Cause Failure Analysis
To maximise the potential of the 5 Whys for root cause analysis, you can use it for what appear to be ‘simple’ failures on the surface. But be prepared to adopt a more rigorous technique.
If your initial WHY shows that there is a lot more to the story than you initially thought, don’t hesitate to adopt a more comprehensive approach to root cause analysis, such as Failure Modes and Effects Analysis (FMEA) or Fault Tree Analysis (FTA).
And always, always have a proficient reliability engineer review all your 5 Whys to ensure quality. Even better, have him or her attend as many 5 Why sessions as possible to provide valuable input and guidance on your root cause analysis.
Final Thoughts
The 5 Whys approach, while simple, is a powerful tool for getting to the root causes of a problem and conducting root cause analysis. The problem is, using this approach makes you prone to underestimating or overestimating the real root cause of the problem you’re analysing. That’s why, like any tool, it’s essential to be aware of its limitations and use it properly.
By combining the 5 Whys with other problem-solving techniques, you can create a comprehensive approach to tackling your problems head-on. If your initial WHY shows that there is a lot more to the story than you initially thought, don’t hesitate to adopt a more comprehensive approach to root cause analysis, such as Failure Modes and Effects Analysis (FMEA) or Fault Tree Analysis (FTA).